Hyprint installs China’s first Domino/Spande hybrid press
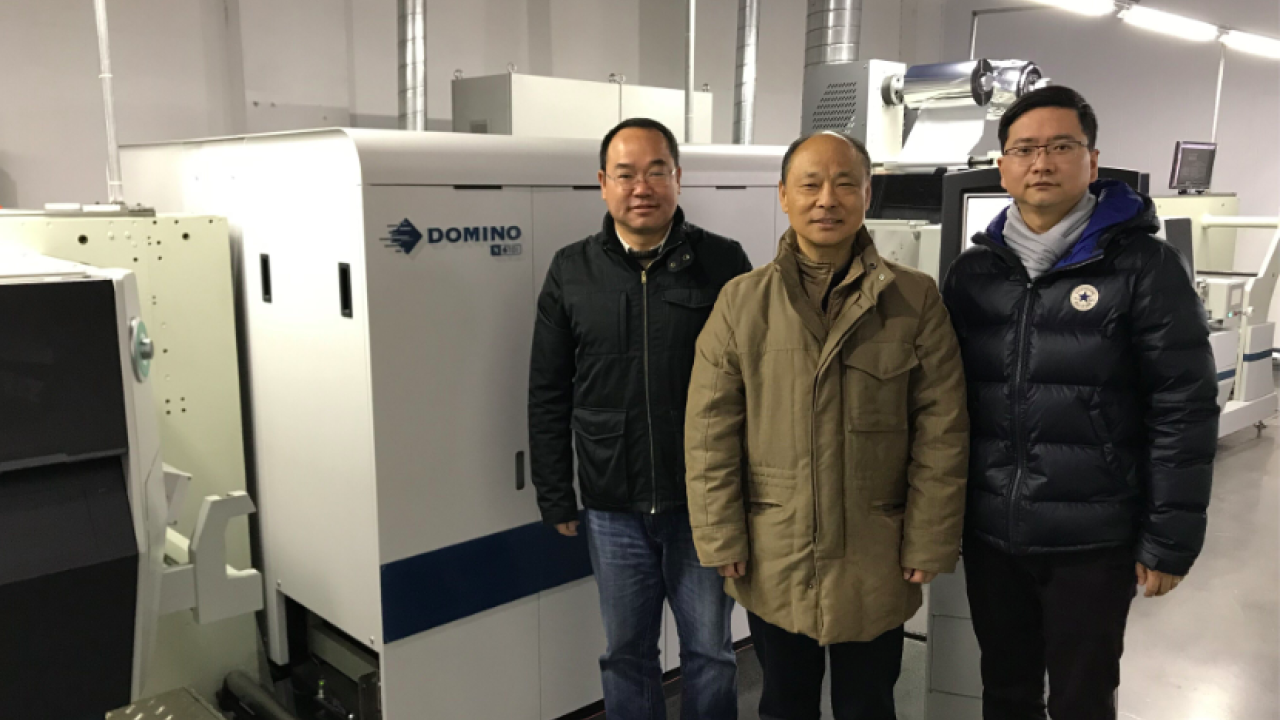
Shanghai Hungyuan Transfer Paper Co (Hyprint) was established in 1993 as an integrated supplier of high-quality labels. Today its products are used across a wide range of end use sectors including food and beverage, stationery and toys, household appliances, clothing and footwear, glass and metal products.
The converter has become an integrated label service provider for many high-end enterprises including Coca-Cola, Exxon Mobil, Nippon, M&G Stationery, Haier, Goodbaby, H& M, Zara, Adidas and Victoria’s Secret.
Ju Jinyuan, general manager of Hyprint, says: ‘In recent years, the Chinese label market has suffered multiple impacts, such as environmental pressures from national authorities, the rising cost of raw materials, and internet sourcing. These have lowered the profit rate for label converters at the same time as the demands from customers are increasing. Under such circumstance, label converters have had to upgrade or transform in order to seek new opportunities.
‘We intend to focus on providing highly cost-efficient products through investment in innovative printing technology and a green production mode. We strive to be a leading company in respect of providing comprehensive label printing solutions in this industry.’
When Hyprint was established, there was a high demand for labels in China and profit margins were relatively high. The company opened plants in Shanghai, Chongqing, Hangzhou and Tianjin. ‘I took charge of the Chongqing plant at that time, and our first product was a heat transfer label for shoes,’ says Ju Jinyuan.
But it was more difficult for the Shanghai operation. In its first two years, it received few orders and generated little profit. In 1996 Ju Jinyuan took charge of both the Shanghai and Chongqing plants. ‘We needed to explore new markets and product applications urgently at that time to turn the plant round.’
The management gathered the sales team and asked them to suggest their top three brands or potential market applications. They then decided to target the motorcycle label market.
‘After half a year carrying out research and improving our technology, we finally sucessfully applied silkscreen heat transfer labels onto the seat of a motorcycle. As a result the turnover of both the Shanghai and Chongqing companies nearly doubled that year,’ says Ju Jinyuan. With the business now stable, Hyprint transferred ownership of its Tianjin and Hangzhou companies and focused its main business efforts on the Shanghai and Chongqing companies.
Later Hyprint developed a range of new products such as heat transfer stickers for children’s products and pressure-sensitive labels for air external conditioner units. As demand for air conditioners increased in China, Hyprint’s business doubled year on year, and the leading air conditioner brands including Haier, Chunlan and Changhong were all key customers. From 1998, Hyprint started growing quickly.
Technology update
There is a clear link between business growth and investment in both the facilities and new technology by Hyprint. After two years of market research, Hyprint successfully applied a gravure heat transfer label to Chunghwa pencils. In 1999, Hyprint introduced the first Shaanxi Beiren gravure printing machine. Five years later, Hyprint successively introduced three gravure production lines.
In 2000, the company moved to a new plant, increasing production space by five times to more than 5,000sqm. In 2003 professional R&D and technology application teams were established. The company integrated its best resources in 2005 and transferred ownership of Chongqing, focusing only on the Shanghai company.
In 2007, at least 90 percent of the pencil, pen and ballpoint pen brands being sold in China were customers of Hyprint, including Mitsubishi, TrueColor, Beifa and Changlong stationery.
‘Our achievements were based on a sound external market environment,’ recalls Ju Jinyuan. ‘China has a huge population so there is a high consumer demand for large quantities of label products.’ Statistics show that 10 years ago the average annual growth rate of the Chinese label market was consistently 15-20 percent, making it one of the world’s fastest-growing. In 2009, almost 1.8 billion labels were produced in China, with a total industrial output value of 14 billion RMB, up approximately 20 percent over 2008.
‘We know that success comes from always keeping ahead, and that continuous innovation and transformation are the foundation for keeping a company alive and prosperous,’ says Ju Jinyuan. ‘As a label converter, we must own our key technology in order to achieve long term development amidst increasingly fierce market competition.’
2010 was a key year for the growth of Hyprint. ‘We developed and launched our own adhesive coating technology which cut the cost of our self-adhesive labels by more than a half,’ says Ju Jinyuan.
‘At that time, letterpress and offset dominated China’s label market, while flexo and digital printing had just got started in Europe. Hyprint’s development strategy is to integrate with international market trends.’
Hyprint installed its first digital label press, an HP Indigo WS6000 (the first in China), and China’s first ETI Converting flexo press. Subsequently, the company installed both flexo and flexo+gravure combination presses, constantly upgrading its technology.
Hybrid label press With the new generation of consumers, the market increasingly demands short-run orders, personalized labels and multiple SKUs as the number of products increases. In addition, the increasing cost of raw materials and labor mean it is ‘inevitable’ that digital technology will be the future tendency of label printing, says Ju Jinyuan. ‘Just like the automobile industry, vehicles previously driven by oil/diesel changed to hybrid then in the future to a pure electric mode. The label printing industry will also experience such a process. Hybrid formats will be an interim, combining the advantages of the two printing technologies and lowering the high cost of digital printing to a certain degree.’
In January 2019, Hyprint installed the first hybrid press jointly developed by Domino and Spande, the N610i IM.
‘Besides the excellent printing performance, accurate color rendition and running stability which fully satisfy our industrial production requirements, we chose the N610i IM mainly because of the manufacturing concepts of these two companies,’ explains Ju Jinyuan. ‘Domino and Spande have the same understanding of printing technology and production quality as Hyprint. We also believe the cooperation of the international leading brand Domino and domestic brand Spande produces a superior effect than merely “one plus one.’
The hybrid press has a wide range of application possibilities, and is specified for a range of different substrates including PE, PP, PET, PVC, lamitube and paper. The post-press units include hot/ cold stamping, die-cutting and silkscreen, and these can be used either in- or off-line. ‘It’s very helpful for improving both quality and efficiency of our company and thus to enhance our overall competitiveness.’
The turnover of Hyprint in 2018 exceeded 120 million RMB, of which export accounted for 20 percent. ‘With the installation of the Domino and Spande hybrid press, we are expecting to raise our annual production value to 200 million RMB and increase our export volume, which will further raise our competitiveness in international markets,’ says Ju Jinyuan. Hyprint has also purchased a Spande 10-color flexo press which will be installed in June this year.
What’s more, Hyprint is now building a plant in Chongqing. This new 20,000sqm manufacturing base was started in 2017. The first tranche of investment was 120 million RMB and it is estimated that construction will be finished in July 2019. The plant will be focused on production, with R&D, sales and management teams remaining in Shanghai.
‘With the growth of the national road and railway network, the traffic advantage that coastal areas previously had is weakening,’ points out Ju Jinyuan. ‘In my view, in the future China’s manufacturing base will gradually turn to the middle of the country, especially for enterprises based in Shanghai, which are suffering various pressures such as recruitment difficulty, high labor cost and stricter environment protection policies.’
The future of packaging, meanwhile, will be light-weighting. ‘The product package displayed in-store will be quite different from the package consumers take home, with maybe only a small label indicating basic product information. The label’s branding will gradually lessen while functionality will be enhanced, which is also Hyprint’s future direction.’
Stay up to date
Subscribe to the free Label News newsletter and receive the latest content every week. We'll never share your email address.