Improving plastic film adhesion with corona
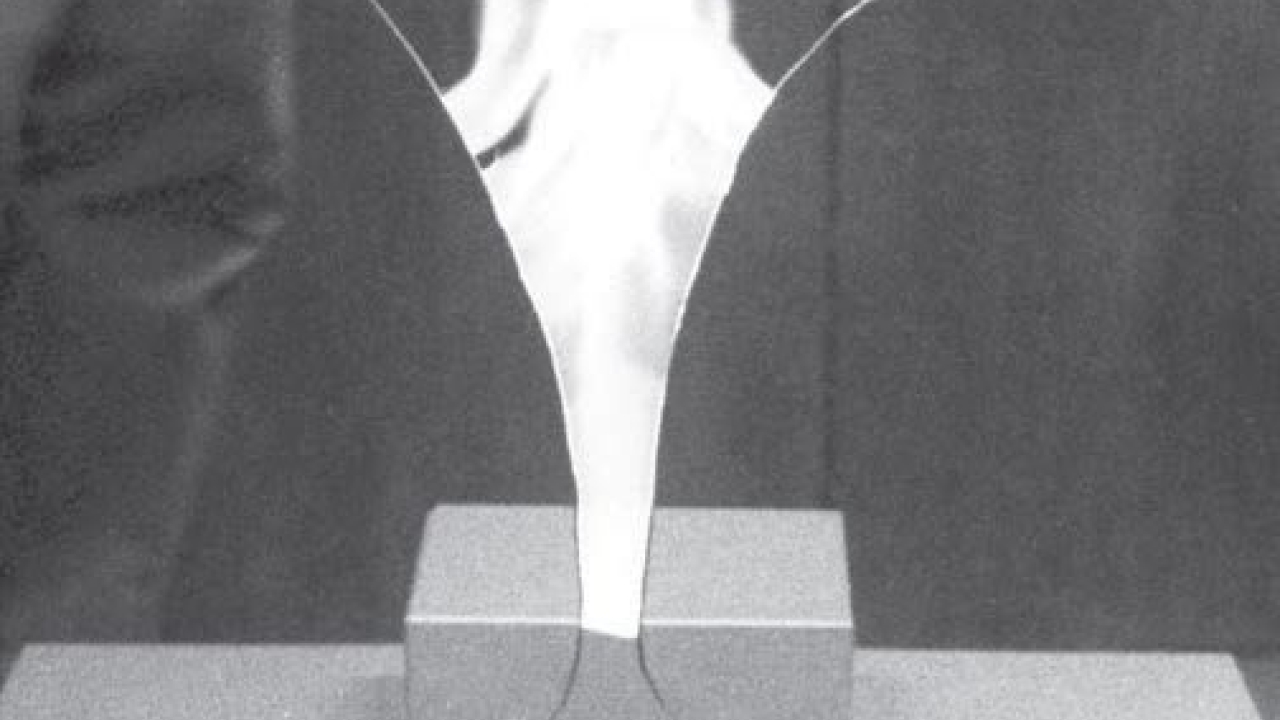
The problem with writing or printing on plastic films is well known; you have a plastic bag and you would like to write on it with a pen but the ink doesn't stick since untreated plastic has a structure that makes it impossible owing to poor adhesion. Corona treatment is the solution, writes Vetaphone sales manager Jan Eisby.
Whether a liquid wets a material well or poorly depends primarily on the chemical nature of both the liquid and the substrate.
Wetting is defined as the ratio between the surface energies of the liquid and substrate. In general, the following rule is true: a material will be wetted if its surface energy (dyne/cm) is higher than the surface energy of the liquid. If not, there will be an adhesion problem.
Avoiding adhesion problems
The pre-treatment offered by corona is necessary to obtain sufficient wetting and adhesion on plastic films or metallic foils before printing, laminating or coating, with a corona discharge unit the solution to optimize wetting and adhesion. This corona technique has proved to be highly effective, cost-efficient and able take place in-line.
Plastic is a man-made synthetic material, which contains long homogeneous molecular chains that form a strong and uniform product. The chains of molecules are normally joined end-to-end forming even longer chains, leaving only a few open chain ends, thus providing a small amount of bonding points at the surface. The small amount of bonding points cause the undesirable low adhesion and wettability characteristics , which is a problem in converting processes.
When Verner Eisby, a Danish engineer and founder of Vetaphone, was asked about a solution to this problem, he came up with the theory that a high-frequency charge would provide both a more efficient end controllable method of increasing the adhesion and wettability of a plastic surface.
During corona discharge treatment, electrons are accelerated into the surface of the plastic causing the long chains to rupture, producing a multiplicity of open ends and free valences to aid adhesion.
The ozone from the electrical discharge creates an oxygenation, which in turn forms new carbonyl groups with a higher surface energy. The result is an improvement of the chemical connection (dyne/cm) between the molecules in the plastic and the applied media/liquid. This surface treatment will not reduce or change the strength. Neither will it change the appearance of the material so not causing . The corona only changes the top molecule chain, which is 0.00001 micron thick.
Determining treatment levels
The effectiveness of the corona treatment depends on the specific material being used. Different materials have different characteristics and different amounts of slip and additives, which will determine the effect of the corona treatment. There are no limits with regard to the materials that can be corona treated. However, the required intensity of the treatment (watt/min/m²) may vary significantly. The treatment level can be calculated by using the following formula: P = T x S x W x M, where P is the total power (watt) required, T is the number of sides to treat, S is the line speed in m/min, W is the film width in meters and M is the material factor, or required watt per m² per minute.
The exact value is best determined by testing a sample of the actual film that is used for a specific application.
Automatic power regulation
Power regulation is required to ensure even treatment of all the material, regardless of the speed or width of the film to be treated. For example, Vetaphone’s own Corona-Plus treaters are equipped with an automatic power regulation system that, when the required treatment level (watt/min/m²) has been determined, will automatically regulate the power needed so the film is influenced by the same energy regardless of the speed or the width of the film.
Durability
Over time the obtained dyne level will decrease and it can be necessary to corona treat the material again just before use. When a material contains slip, the dyne level will fall faster, as it will for thicker and older film stocks which are more difficult to treat as slip agents may have migrated to the surface. Also, storage conditions and temperatures can affect the decay of the corona treatment.
Generally speaking, the more difficult a material is to treat the quicker it is likely to decay. It has been established that films with very high slip additives (over 1,200 parts per million) can be totally resistant to printing just 24 hours after treatment, and it may be necessary to process the film immediately following treatment, or place the treatment in-line with the printer.
Material which has not been treated under extrusion can be difficult to treat afterwards. Therefore it is recommended to treat film just after extrusion, and then use a refresh treatment just before the liquid/media is applied to the surface.
Maintenance
It is important that corona systems are maintained properly in order to preserve the same effect of the treatment, and thereby obtain the desired dyne level. The maintenance will create down time in production, but there are solutions available to minimize this.
Vetaphone offers the quick change (QC) cartridge system, which will minimize set-up time of electrodes and maintenance.
The complete corona electrode is mounted in a specially designed pull-out/push-in cartridge.
Read more features from PPW here
Stay up to date
Subscribe to the free Label News newsletter and receive the latest content every week. We'll never share your email address.