Henkel invests pro-actively in the Indian market
India holds a key position for Henkel’s global adhesive business as part of its long-term growth strategy both as a domestic market and a base to serve other international markets
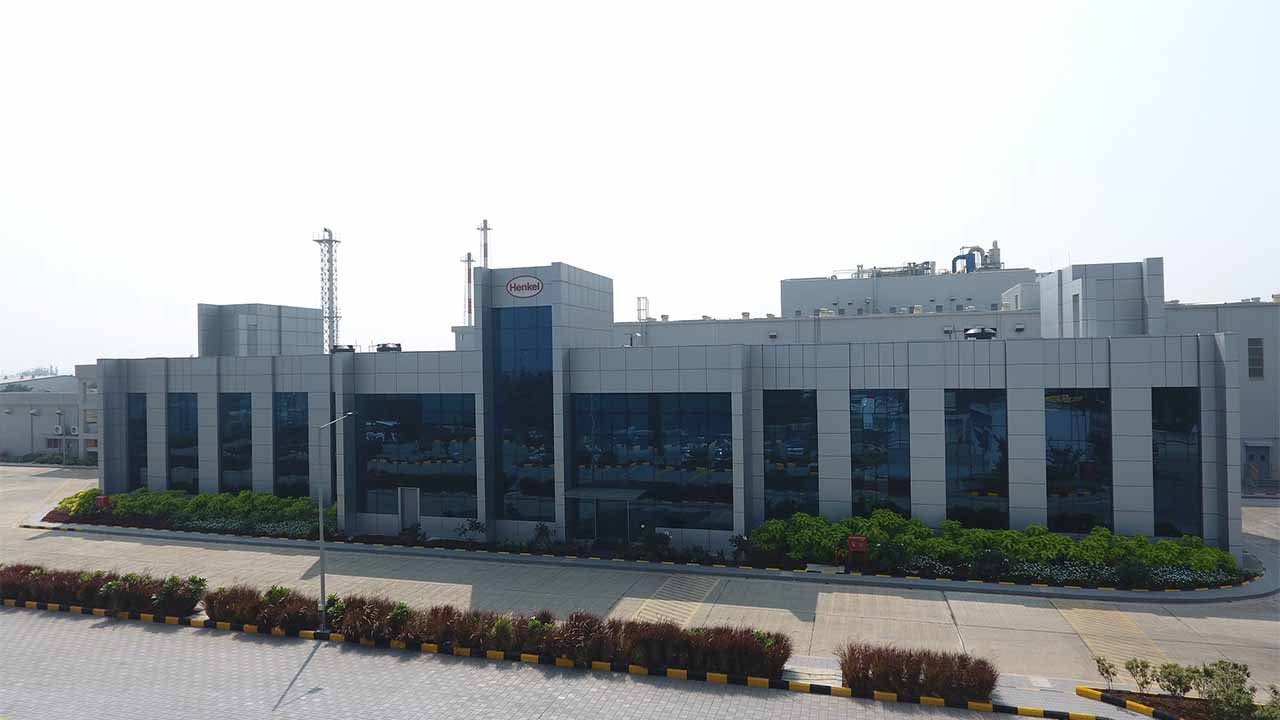
Henkel's Kurkumbh site
With the launch of its manufacturing facility in Kurkumbh in the last 3 years, Henkel has created capacity to meet the demands for its products in India as well as markets such as the Middle East, Africa, South Asia and beyond.
Sunil Kumar Sathyanarayanan, country president, Henkel India and regional director packaging IMEA, Henkel Adhesive Technologies says: ‘India’s strong GDP growth track record underpinned with right investments and a strong focus on values such as sustainability is impressive and aligns strongly with Henkel’s values. We have proactively invested in India for the last 10 years and more keeping the above in perspective. We have set up and expanded our manufacturing sites in the country. Our sites in Kurkumbh, Thane, Rudrapur and Chennai are focused on various technologies and produce different products to serve our customers.’
‘Our largest adhesive manufacturing site in India is in Kurkumbh near Pune. The first and second phases of this multi-technology and state-of-the-art site are up and running. This site enables us to localize our product portfolio and reduce imports while bringing the best global technology to India,’ he adds.
The Kurkumbh site is Industry 4.0 (MES – Manufacturing Execution System) enabled ensuring fully automated, data-controlled production environment, providing traceability and process correction flexibility. It is among the few chemical manufacturing sites to be awarded the LEED Gold certificate by the US Green Building Council based on a holistic energy efficiency concept.
Process automation
The key focus area in shop-floor management is to ensure availability of process and operational KPIs in a transparent and instantaneous manner. This can be ensured by avoiding processes being managed in multiple environments such as spreadsheets, databases, web tools and non-integrated systems including DCS/PLC systems.
Henkel has set up a smart factory in its Kurkumbh manufacturing site to bring all systems onto one standardized platform, besides enabling benchmarking, eliminating waste, increasing agility and attaining manufacturing maturity. It has a fully integrated environment from vendor to customer. It provides a seamless and transparent view of the entire process right from the receiving gate to warehousing, SHE (safety, health and environment), manufacturing, quality, maintenance, packaging, storage and shipping.

‘Our experience across global sites has shown an improvement of at least 10 to 15 percent reduction of cycle times, greater cost savings and a huge reduction in rejection of batches and manufacturing ‘right the first time’ in a short span after deployment,’ Sathyanarayanan adds.
Customer Experience Center and Academy
The company has also set up Customer Experience Center and a Flexible Packaging Academy in its Thane, Mumbai plant.
‘In this competitive industry, technical know-how and applications knowledge is of key importance, which if properly addressed can result in significant quality improvement, profit and growth for a company. The Flexible Training Academy focuses on achieving this through proper training,’ Sathyanarayanan says.
Based on the training modules of the Flexible Packaging Academy in Germany, Henkel has been offering a five-day Flexible Packaging Training program at its academy in India with the Indian Institute of Packaging (IIP) in Mumbai as its knowledge partner. The academy strives to elevate participants' knowledge on current global standards. The modules include practical hands-on experience on industrial scale lamination machines and theoretical classroom sessions.
The training covers all aspects of flexible packaging that have an impact on the lamination process including printing, lamination and finished product testing. By successfully completing the training, participants become a Henkel and IIP-certified specialist in lamination techniques for flexible packaging. The academy also offers services such as analysis, testing, and research and development.
The IMEA Customer Experience Center (CEC) in Mumbai is designed to inspire joint collaboration and co-development of new products with our customers, partners, suppliers and others.
‘Our aspiration is that the IMEA CEC will maximize business value for our customers and partners, besides opening doors for future growth opportunities while tapping into our core values of efficiency and sustainability, know-how, broad solution portfolio, and global capabilities,’ Sathyanarayanan explains.
Adhesives for labels – a growing segment
Henkel has been witnessing an increase in demand for its range of adhesives in the labels segment, owing to several factors including the growth of the consumer goods and e-commerce markets. Considerations that impact the final choice of adhesive technologies include convenience, recyclability and adherence to a range of substrates under different conditions.
The company has developed a broad portfolio for labeling applications under its brands Aquence and Technomelt including hotmelt rubber, UV curing, water-based and solvent-based acrylics. Its labeling adhesive portfolio also includes adhesives that are safe for use on food packaging.
Its products are created with consumers in mind. One such product is Technomelt PS 8001 developed for the Indian market.
Manufactured in its Rudrapur plant, Technomelt PS 8001 is a hot melt pressure-sensitive adhesive for tapes and label stock application. It displays high tack and good peel strength performance
‘We recommend this product for use across all standard roller or nozzle applicators as it brings in a strong value-added benefit to our customers,’ Sathyanarayanan adds.
Stay up to date
Subscribe to the free Label News newsletter and receive the latest content every week. We'll never share your email address.