Karlville focuses on flexibles finishing
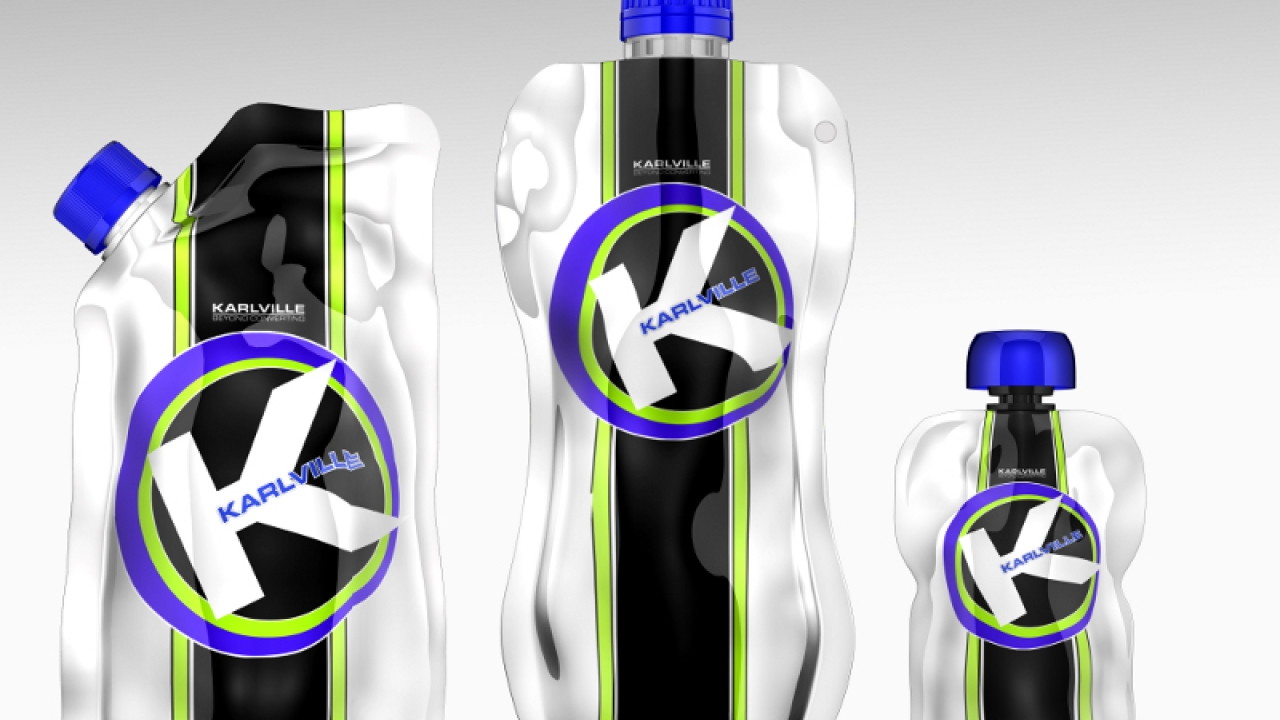
As the number of mid-web presses dedicated to flexible packaging grows, Karlville is launching new finishing systems targeting flexibles and pouch packaging markets. Danielle Jerschefske reports
Karlville Development Group is probably best known in the labeling industry for its shrink sleeve label seaming and application machinery and its slitting and rewinding equipment. But as label converters look to move into package printing markets with new mid-web inline presses, Karlville has developed narrower machines for the laminated flexible packaging and pouch converting sectors.
The global flexible packaging market is estimated to be worth around 76 billion US dollars with a five percent anticipated growth rate, while the global label market is 55 billion US dollars with growth slowing to one and two percent in mature markets. Fifty percent of flexible packaging in the US contains food, and thirty percent of this consists of pouch containers. Most of this flexible market is served by wide web converters with the narrow web industry currently contributing an insignificantly small percentage.
Last year Karlville opened an R&D facility in Elgin, Illinois, dedicated to laminating and pouch conversion. Label converters looking to diversify their portfolios beyond pressure sensitive label production will likely find these facilities to be a useful resource. Raul Matos, vice president at Karlville, says, ‘There are many label converters that claim to be pouch producers, but in reality they are purchasing pre-made pouch structures to be top coated and printed. We would not consider this to be sophisticated pouch business and much of the margin can be achieved simply with in-house solventless lamination capabilities.’
A move into flexible packaging is feasible for the label converter willing to research and invest accordingly, Matos believes. The market’s requirements differ from, and are more demanding than label manufacturing. In North and Latin America, some converters can be seen using shrink sleeve label conversion as a platform to move into flexible packaging production. A clear strategy is imperative. On a scale of difficulty from one to 10, Matos believes that shrink sleeve label production is about three, while flexible packaging is more like a seven.
Stakeholders align
The stars are coming into alignment to make mid-web packaging conversion an efficient and profitable move for a label print business. New machinery is here to manage multiple SKUs, faster turnaround and more efficient production to meet brand, retail and consumer preferences for variety and more frequent design changes.
Many of the narrow-web industry’s leading press manufacturers offer machines engineered for thin material conversion: a list would include Muller Martini, Xeikon, Omet, MPS, PCMC and Nuova Gidue, all of whom offer presses at widths between 20-26 inches. At Labelexpo Europe 2013 more players introduced mid-web offset, flexographic and digital offset 20-30 inch presses: Nilpeter’s MO-5; the Mark Andy Versa Max; HP Indigo 20000. These high-end machines are intended to capture a piece of existing consumer packaging orders coming down in run length.
Converters will be looking for production benefits against wider web printing and converting machinery including improved uptime, rapid changeover and better profitability. This can be achieved using wider ‘label’ machinery with flexible packaging industry-specific design attributes.
Says Matos, ‘The potential reward requires a change in mentality. First of all, this is production of primary packaging that comes into direct contact with food. Converters must be knowledgeable about the inks and adhesives involved and layering techniques. They must have a lab to test the complex laminations made and will need to acquire FDA and American Institute of Baking (AIB) Superior Certification compliance to service the food sector in the US.’ Separate but functionally similar certifications apply in Europe.
At TLMI’s recent Technical Conference, chemical migration of inks and adhesives was a prominent discussion as North America’s leaders looked to educate themselves on what’s at stake. A panel including Tom Hammer of Flint Group and Catherine Nielsen, a packaging attorney, spoke frankly about the attention to detail that is required for properly producing packaging that comes into direct contact with food.
Lamination
Lamination equipment is a ‘must’ for entering these markets with an added value proposition, and Karlville has developed a series of offline solvent and solventless laminating machines in both wide and mid-web widths via its Webcontrol partnership.
Offline solventless laminating offers a number of advantages including lower energy and raw materials costs and a better environmental profile. Solventless adhesive is generally applied at a lower weight and modern chemistries cure thoroughly at room temperature. Curing time too is typically shorter at around eight hours.
While inline lamination is an option for some of the latest mid-web packaging presses, only solvent, water-based and UV adhesives can currently be applied inline. Solventless Inline is relatively new to the market and Nuova Gidue was seen launching this technology at Labelexpo Europe. While current application systems use a traditional flexo or gravure coating head, solventless lamination requires a multiple smooth roll system with precise and consistent tension.
Karlville’s lamination head consists of three rollers: lamination back-up, nip and heat lamination to eliminate small dots. The entire coating head includes five rollers with three independent motor drives for the feeding roller, dosing and application. Already available in 1,000mm and 1,300mm wide options, Karlville showed its latest 800mm wide system at Labelexpo Europe. It can reach speeds up to 400m/min and can include a corona treater.
Pouch systems
Karlville’s KSG multiple format inline pouch converting machines are available in twin lane and single lane formats. For liquid packaging, machines come equipped with modules that allow for two pouch formats. Module I produces single and dual gusset shaped pouches with a front dispensing spout. Module II makes side gusset pouches with a front pour spout. Each comes with a vibratory bowl feeder and rotary spout application system.
For the mid-web market Karlville now offers its KSP Standup Pouch machine with half the footprint of the company’s existing machines to convert material widths up to 800mm (31in). This machine is an ideal partner for offline finishing of materials produced on the new range of mid-web presses.
The next step for the Karlville Group will be the introduction of pouch filling machines. The supplier specializes in catering to the needs of both packaging converters and CPG buyers or contract packagers, bridging the machinery gap between supply chain stakeholders. This strategy can be seen in its offerings for the shrink sleeve label market, and will be mimicked for flexible packaging.
Paint in a Pouch
The Association for Dressings & Sauces (ADS) named Coldec Concepts its 2012 Package of the Year Award winner. Coldec won for its Paletto Paint Mix & Shake Bag, which has possible future applications in the dressing and sauce industry, as well as potential environmental benefits. Mondi produced the bags at its Steinfeld, Germany plant, and also has the capability to produce the top spout, or NorSpoutBag, at its recently acquired location in Jackson, Missouri.
The Paletto Paint Mix & Shake Bag can hold up to 2.5 liters of liquid. Color is made by adding a tube of pigment to a pouch of either pastel or saturated paint. The consumer then mixes the pouch to produce the desired paint hue.
Sustainability: Labels vs flexibles
All supply chain stakeholders must closely review environmental claims surrounding flexible packaging. It is critical that Life Cycle Analysis used to support sustainability claims includes end of life recovery. While benefits can be found reducing carbon and energy emissions by shipping lighter materials, the recyclability and reuse opportunity for laminated flexible packaging is limited. On the other hand, the label industry is currently collaborating closely with value chain leaders to address label and rigid container recycling and contamination issues.
Stay up to date
Subscribe to the free Label News newsletter and receive the latest content every week. We'll never share your email address.