Labelexpo Europe review: Tooling advances improve press productivity
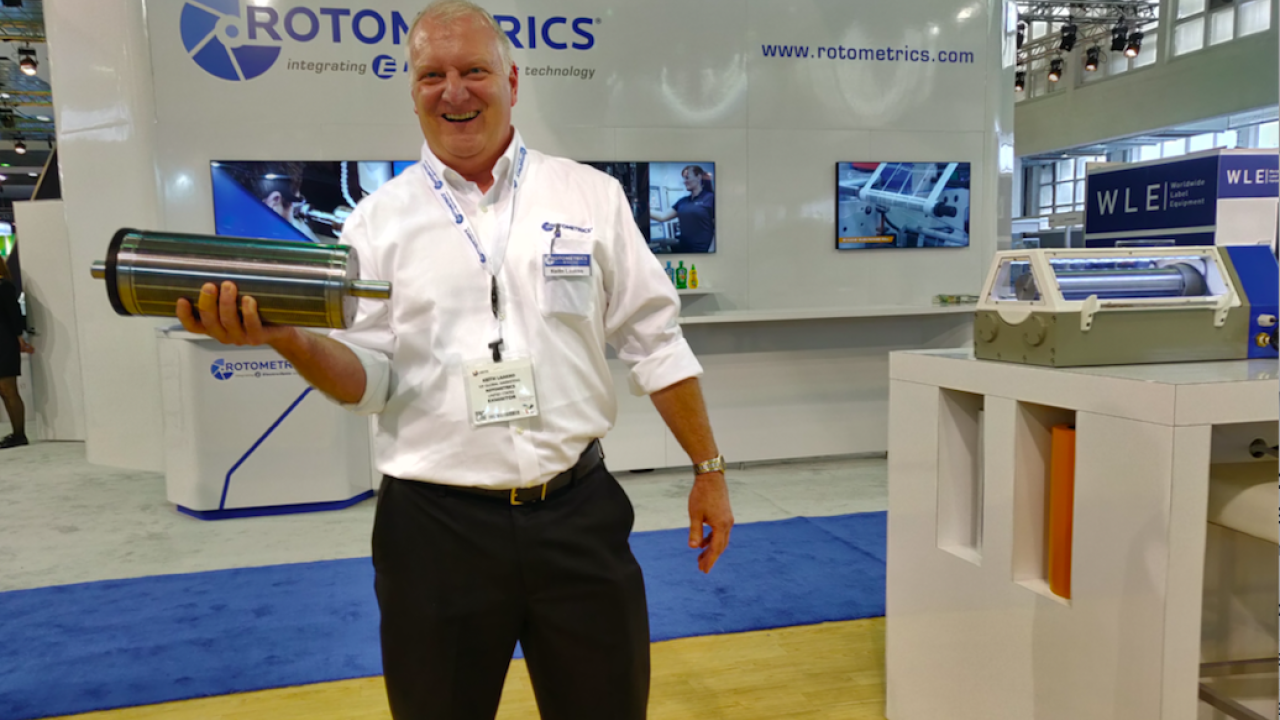
Applied Laser Engraving introduced nano-second 500-watt harmony laser engraving machine. This technology allows the end user to laser engrave metals, ceramics and polymerics all on a single laser engraving machine. This gives access to a variety of applications including security, optical film, gravure, embossing, anilox, flexo, letterpress and applicator rolls, all engraved on a single machine.
Indian manufacturer Diehard Dies showcased its print cylinders and sold rotary dies.
Harper Corporation of America showed numerous engravings available for anilox rolls alongside its QD Proofer, an ink proofing and flatbed ink proofing system which uses flexo and gravure processes. It can be configured at four different speed units. The maximum travel speed is 150ft/ min and the travel distance can be adjusted anywhere from 12 to 33 inches in one-inch increments. It is available in either a 2.75in or 5in proofer width.
Kocher + Beck showed its latest GapMaster design, which allows for both front and back cutting and is now available in a magnetic cylinder version for semi-rotary presses. Also shown at the show was the UR Precision non-stop winding technology, demonstrated in a fully equipped non-stop off-line cutting configuration. The company’s TecScreen division showed its new screen printing mesh, as well as a compact cleaning unit. Also on show was the new generation of Kocher + Beck’s Gluex Coating which gives an improved non-stick result with less adhesive residue on the cutting edges.
Rotometal showcased its portfolio of magnetic cylinders, printing cylinders, sheeters and cutting units.
RotoMetrics showed EZ Clean idler roll and EZ Clean stripping roll at Labelexpo alongside the newly launched Versa-Cut adjustable anvil. On display was the company’s RotoRepel technology, a non-stick coating available on its solid and flexible dies.
Idler roll features a patent-pending design that improves web tracking, minimizes ink transfer and therefore reduces cleaning time. Lifted labels and adhesives do not stick to the roll. Another feature of idler roll, that enables presses to run longer and faster, is that breakdown of waste matrix does not stop the press: it continues to run as if nothing happened. A stripping roll minimizes label blocking and lifting, thus reducing the waste and minimizing damage on dies.
RotoMetrics’s Keith Laakko said: ‘Converters see significant improvement in productivity using our idler rolls. Using it in combination with stripping rolls and RotoRepel can make their presses run even faster.’
RotoMetrics also showed a light-weight magnetic cylinder that Laakko easily lifted with one hand to demonstrate the claim. He says these cylinders reduce inertia by 30 percent on a press which results in less pressure on motors.
Also new, Versa-Cut adjustable anvil adheres to thickness inconsistencies in materials. It allows precise control of cutting depth for optimal liner strike and is stable enough to convert films. These are being manufactured and shipped worldwide from RotoMetrics’ plant in Missouri, with manufacturing due to begin soon in Brazil, Europe and Australia.
Spilker presented S-Con Starline CLS 500 converting machine for production of core linerless labels. The capabilities of the machine were demonstrated with the support of Ritrama and Omet. It is designed for cutting and inspecting printed materials at high speed. Two vacuum pull stations ensure optimum web tension during the process and enable the cutting of open adhesive and the processing of CLS material. Also on display were the latest versions of the MicroGap adjustable anvil cylinder, allowing fine adjustment in steps of 0.5 micron. The automated version with electronic actuator offers maximum ease of use and minimizes the risk of damage to the cutting tool.
UEI Group demonstrated the NW SpeedChase NXT system that claims to change the way engraved hot stamping and embossing flat dies and counter forces are set-up on a flatbed narrow web press. According to the company, narrow web press operators now experience easier lock-up, quicker changeover, lower overall costs, increased speeds, and improved overall efficiency with the new system.
Wink highlighted the enhanced line of SmartGap adjustable anvils that allow cutting depth to be adapted to different liner thicknesses. The SmartGap Advance has been developed as the basic version of the system and can be upgraded to the digital SmartGap Touch. Also launched at this year’s show was SmartGap AutoControl, where a sensor bar continuously monitors the die-cutting result and automatically adjusts the die-cutting depth, if necessary.
Stay up to date
Subscribe to the free Label News newsletter and receive the latest content every week. We'll never share your email address.