Leading with standardization and automation
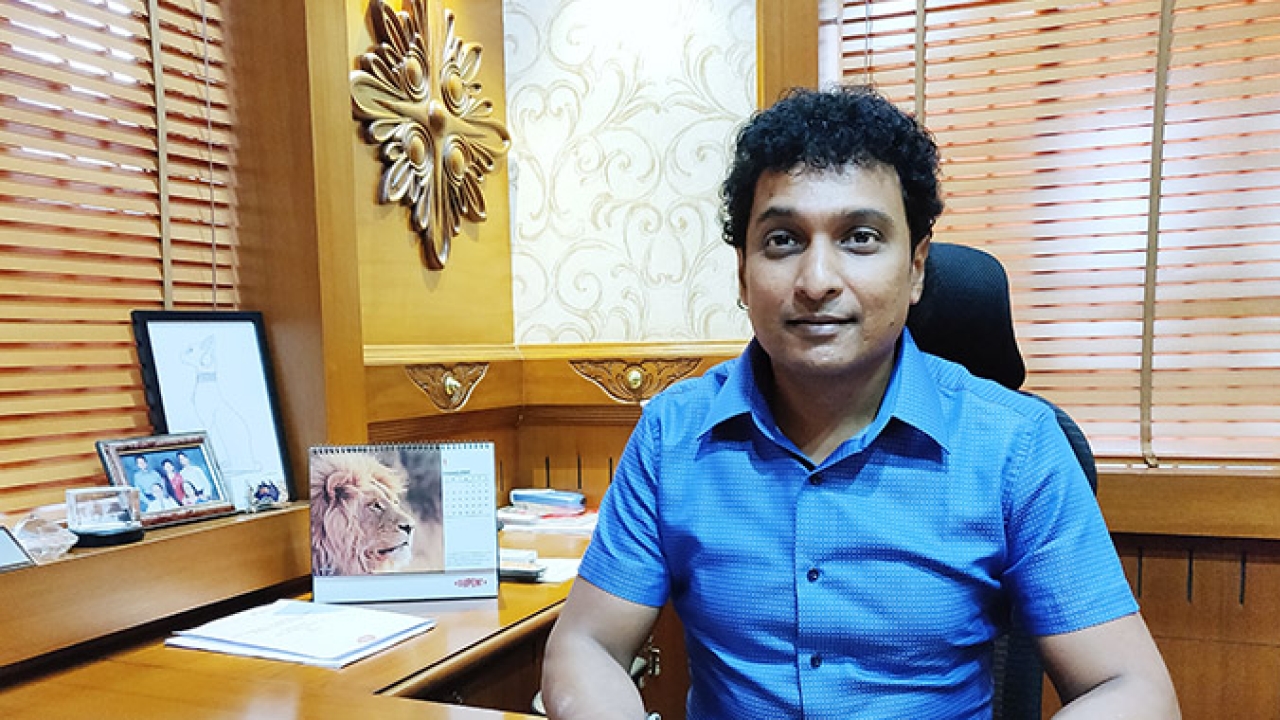
The first is the importance of having a great team. Jaichandra, popularly known as JC, says: ‘You can invest in the best equipment and infrastructure, but the business can never be efficient if you don’t have the right people. It is the production teams that deliver commitment to quality which in turn establishes and maintains good client relationships.’
Known for being employee centric, Veepee Graphics provides a positive work environment. It runs an employee recognition program to keep staff motivated and runs regular training to enhance skills and ensure safety. It was the first flexo tradeshop in the country to be Sedex and Disney certified in 2018.
‘You throw peanuts, you get monkeys! I strongly believe in this statement,’ says Jaichandra. ‘It takes a long gestation period to train people to the highest level and to keep them motivated we need to ensure that they are given a good remuneration and an excellent work environment. You need good, efficient and loyal people, rather than just technology, to run a business.’
The second strategy is adopting technology and processes that keeps it ahead of the curve. In 2005, the company took the first major step of going paperless and today with the Veepee App, live status of jobs can be tracked until plates are delivered to the customer. ‘We want to differentiate ourselves from the competition and the only way to do this is evaluate, update and upgrade. This is one of the reasons why we are a preferred beta-testing site for some of our vendors. Our feedback and evaluations are taken seriously,’ says Jaichandra.
Not only does Veepee Graphics get to understand technology not yet available in the wider market, it allows the company to be an early adopter which in turn justifies the charging of a small premium while maintaining internal efficiencies.
Ensuring printer efficiency Before printers send their respective jobs to Veepee Graphics, Jaichandra visits their factory and ‘fingerprints’ their presses for standardization. ‘We started doing this back in 2005. I travel a lot not for marketing, but for technical support and standardization. I personally create the profile for clients and set standards in my office. Only then it is passed to my staff for them to manage it,’ says Jaichandra. Fingerprinting implies standardizing all press variables such as substrates, ink and anilox rollers to make error-free and high-quality plates. ‘On average five profiles per press are made, one for each substrate. We then customize our pre-press according to the machine and request the printer not to change any settings without prior dialog. This scientific approach allows our customers to get high-quality predictable prints, first time, without any errors,’ he explains.
He insists that managing variables in flexo printing is possible with standardization: ‘With fewer variables compared to other methods of printing, flexo is one of the easiest and versatile printing technologies available in the market today.’
When it comes to gravure-to-flexo conversion, according to Jaichandra, ‘It is possible to get to 85 to 90 percent of the print quality, but here the marketing pitch should be about providing sustainable packaging solutions with lower cost and faster turnaround, and encapsulate the advantage of printing on certain materials which are difficult to print in gravure.’
Veepee, while ensuring the standardization of printers’ presses, offering high-quality plates, good customer service and technical support, demands a premium on the platemaking. In a market where most of the players, at large, succumb to price pressure, Jaichandra has carved a niche.
Automating in-house efficiency
One of the key factors to successfully implementing automation while enhancing output quality was putting in place stringent quality checks at each stage. ‘We have streamlined operations at all our three plants in Bengaluru, Pune, and Colombo, Sri Lanka. We follow systems and processes and try our best to ensure all jobs that leave our facility are error-free,’ says Jaichandra.
The company has a cause and preventive action (CAPA) form that has to be generated whenever there is an error anywhere in the process. ‘The CAPA evaluation is carried out with the team every week and is part of our internal training process. In case we see repeated mistakes of the same nature, necessary changes are done in our ERP to ensure the corrective action becomes a part of the workflow to eliminate such errors again.
The ERP identifies each job with a unique number. The job is then routed to pre-press followed by quality checks, customer reviews and finally plate-making.’
Veepee even lets customers track the status of their respective jobs with a customer friendly mobile application launched at Labelexpo India 2018.
‘The mobile app and the ERP together have automated each step at our facility. The ERP, through the mobile application, sends a notification to the customer’s mobile and email from the time we receive the file till the plates are delivered. We have continued to make a comprehensive and interactive ERP system that is continuously evolving with a lot of controls.’
Jaichandra explains that mature markets are highly design focused because customers buy what looks appealing, especially when they want to try something new. ‘In most of the flexible packaging in countries like Australia where flexographic printing is widely popular, printing is of acceptable quality. The importance is given to the design and attractiveness of the product on the shelf. That is because customers either know exactly which product they want or they choose a pack based on the design aesthetic or key information,’ he elaborates.
‘Of late, with the increasing demand for added value and embellishments in the folding carton segment, and with brand owners pushing for just-in-time supply, it is opening up a new opportunity for the flexo industry. Understanding the process and printing technology makes all the difference,’ Jaichandra concludes.
Stay up to date
Subscribe to the free Label News newsletter and receive the latest content every week. We'll never share your email address.