Low-down on low migration
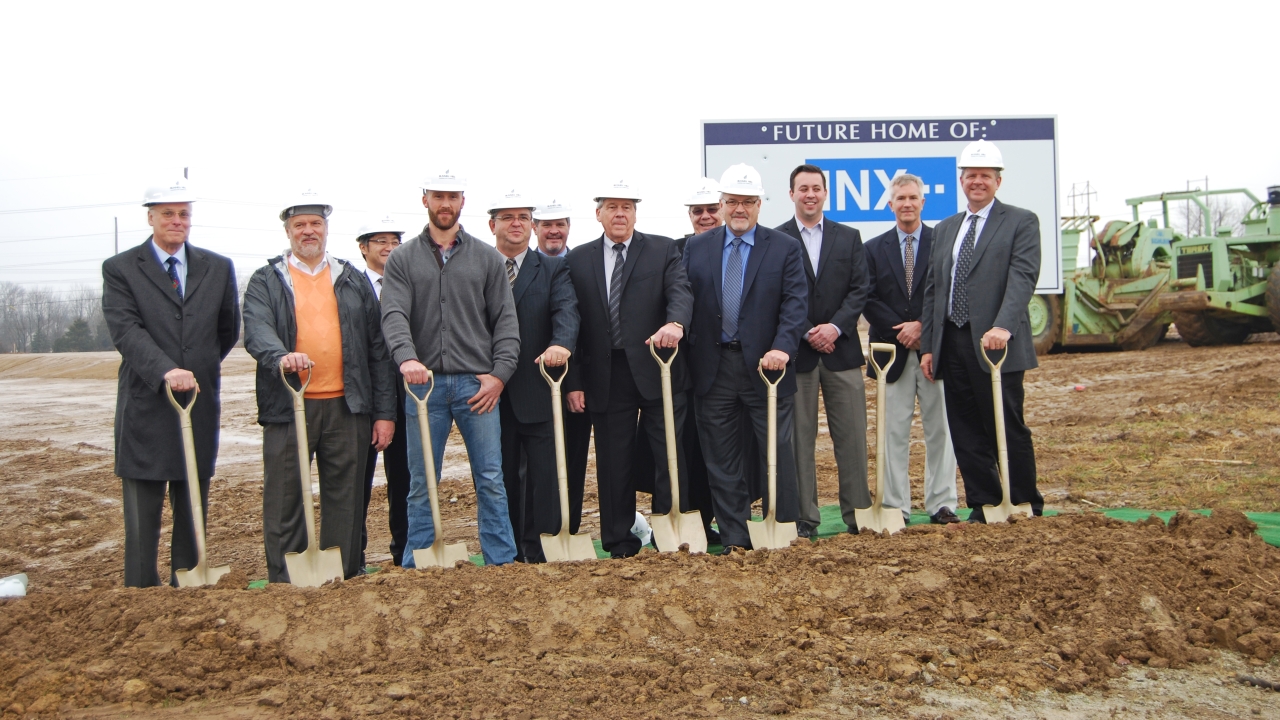
But perceived or otherwise, such risks have led many brand owners and packers to demand low migration (LM) inks and coatings for food packaging where some form of radiation curing is used. Extension of such demands to include the pharmaceutical, cosmetics and healthcare sectors cannot be ruled out.
UV ink and coating manufacturers have reduced migration levels by using photo-initiators that have a higher molecular weight, augmented with suitably modified acrylate monomers and binding agents. But this is only part of the story. Other factors include: packaging specifications; the converter's choice of substrate; the validation of the printing process; and validation of the final packaging by the food processor. Full cooperation is naturally required at every stage in the supply chain, including the design and pre-press stages.
‘The concept of low migration does not really apply to ink, as “migration” refers to the transfer of various components from the finished package into the food product. LM inks really refer to products that have been developed by ink suppliers to help the printer achieve desired results in accordance with current regulations,’ says Jonathan Graunke, VP – Energy Curable Technology, at INX International Ink. ‘Utilizing packaging designed for fitness of use is part of the brand owner's responsibility.’
In a similar vein, Jonathan Sexton, Sun Chemical's European sales and marketing director for screen and narrow web, agrees that the definition and interpretation of 'low migration' can differ among material providers: ‘Migration depends on the whole printed structure, not just the ink or other individual material. Our position is that low migration means ink products that have been specifically formulated to limit migration to the minimum parts-per-billion levels through their chemical composition, even where the package itself offers no or limited barrier properties.’
Toothless regulations?
In Europe the use of UV-cured inks in food packaging is regulated by EC 1935/2004. Regardless of the printing method or curing process, it requires that 'food contact materials must not transfer their components into food in quantities that could endanger human health, change food composition in an unacceptable way or deteriorate its taste and odor.' However, unlike the forthcoming European Union food labeling legislation governing consumer information, there are no mandatory requirements for UV-cured LM printing inks, lamination adhesives, cold-foiling adhesives, and lacquers. Instead there is the Good Manufacturing Practice (GMP) which refers to the consistent control and production of components so they conform to the rules. The European Ink Makers Association, which reviews inks and coatings for legal compliance, is a good source of information on this, as well as the legal requirements (www.eupia.org).
Although only legally binding in Switzerland, the Swiss Ordinance SR 817.023.21 casts a large shadow. Backed by the GMP directive, it sets out the permitted substances in food packaging inks, as well as a list of permissible inks, that show migration levels below the published Specific Migration Limits (SMLs) of from 10-50 parts per billion (ppb). The huge Nestlé organization bases its standards for food contact materials on the Swiss Ordinance.
What about a North American equivalent? According to Rebecca Lipscomb, regulatory manager for Food and Pharmaceutical Packaging at INX International Ink, there is no FDA equivalent. Relevant legislation in the USA under direction of the FDA would be FDA Title 21 CFR or FCN – Food Contact Notification.
‘Food packaging regulations exist to prevent the adulteration of food. The main concerns for the food packaging chain include pre-market clearance for direct food contact and non-food contact inks/coatings (indirect food contact). Direct food contact such as printing inks/coatings that are intended by design to be in contact with food, must be regulated under 21 CFR parts 173-178.’
Non-food contact inks and coatings (indirect food contact) such as those printed on the outside packaging may require a functional barrier to eliminate migration, says Lipscomb. ‘This type of contact does not necessarily require compliance with pre-market clearance or indirect food additive guidelines. Mere contact of a food product does not necessarily trigger compliance needs. The contact must be reasonably expected to result in an ink or coating becoming part of the food product. Printing inks and coatings must never be direct food additives.’
Besides PS labels, typical packaging products include shrink or wrap-around sleeves on plastic bottles, in-mold labels for dairy products or film-based pouches and sachets. Packaging based on aluminum foil or metallized plastic film may be borderline, depending on the application of any UV-cured coatings. Ironically, the case for using the latest ultra-thin films may be weakened in the context of packaging for high-fat content foods. By contrast, aluminum cans, glass containers and PET bottles of a suitable thickness form a functional barrier and can be printed with conventional UV inks and coatings.
Specialized laboratories usually determine the actual barrier properties of the secondary and primary packaging materials. Under standardized conditions they use gas or liquid chromatography and spectroscopes to establish target compliance requirements. The process also identifies migration profiles as the basis for risk assessment data. The four main causes of migration are:
• Penetration of a migrant substance through the packaging layers to the reverse side of the printed surface to contaminate the product, before or after filling (diffusion migration).
• Set-off migration when, under pressure, the printed surface migrant transfers to the non-printed, reverse side of wound labels or stacked sheets which comes into contact with food. It is therefore essential to prevent under-cures to minimize the risk of set-off.
• Gas phase migration, where volatile substances are transferred in the space between the product and the packaging.
• The condensation extraction of critical components during a heating process. Each of these methods can potentially create risks to human health, or cause some unacceptable change in a food product's composition or odor.
Interestingly, the board for offset-printed food cartons traditionally contained a large recycled newsprint content, which was later seen as unacceptable for food packaging compared with virgin board. When BPIF Labels, a UK trade body with a membership of 40 converters and suppliers, sought to issue guidance on the migration problem it used a template – complete with a version of the Good Manufacturing Practice – from its sister organization, BPIF Cartons.
As many food label printers know, implementing a full LM programs is an expensive undertaking. LM inks and coatings presently cost roughly 30 to 50 percent more than conventional products, although in mitigation they represent no more than 5 percent of the printed package cost. The higher costs are expected to diminish as volumes grow, but they still represent yet another charge on doing business in a competitive, albeit large volume, label sector.
Furthermore, deep-clean press wash-ups, including anilox rolls and ink pans, are costly and time-consuming, which is why LM operations use dedicated UV flexo or offset presses. The UV curing rates, ink control systems, and operational speeds remain broadly similar to those of conventional UV curing.
Chesapeake Bristol, a leading UK producer of food labels and part of the Chesapeake group of European packaging printers has several years of LM experience. It recently upgraded its system by being the first UK converter to adopt so-called ultra-low migration (ULM) inks made by Paragon Inks in Scotland. This follows independent tests in accordance with the Swiss Ordnances.
‘We now offer the new inks as standard for all our customers,’ said Andy Walter, managing director. ‘Pressures are building on brand-owners to treat migration issues seriously and we think the improved ULM inks gives them extra safety and assures them of our commitment. After all, they can source labels for their pan-European brands from all over the world. Should a smaller label printer with only domestic food-based customers need to adopt LM inks? Probably yes, but probably not just now.’
In Sexton's view, volumes of low migration products are clearly growing every year, but the majority of food packing is still printed with standard products. ‘In many cases migration testing and risk assessment could provide sufficient justification for this, but clearly there is significant further progress to make.’
Ironically, the inherent risks that UV curing may bring to food packaging can be turned into a strength: ‘What makes UV unique is the ability to clearly identify the components that may migrate into food stuffs,’ said Graunke. ‘The formulators of UV inks and coatings have done a good job of developing products that meet or exceed regulations. The toxicological profiles of specific materials, such as certain photo-initiators, have actually provided evidence that the evaluated materials are benign to certain levels. The use of UV for packaging will likely increase since it has the best available control technology when used properly.’
The LED-UV low-down
LED-UV curing is the most energy-efficient of all curing processes, and offers many benefits. The compact size of the curing units offer greater flexibility compared with conventional UV systems, while lower heat levels facilitate the handling of temperature-sensitive films. The combination of reduced energy consumption and longer lamp life should also reduce running costs.
‘On the downside, the UV output from an individual LED lamp has a very narrow bandwidth, with the bulk of the energy distributed over a narrow range of wavelengths,’ says Jon Harper Smith, a marketing manager with Fujifilm Speciality Ink Systems. ‘However, in the future inks will cure at longer wavelengths and lower film weight. LED technology will evolve and broad spectrum devices will be developed, increasing the range of applications for which this becomes the most suitable process.’
We have already seen LED-UV curing progress solely from inter-color pinning, where the low intensity UV radiation helps reduce the risk of the ink droplets spreading to introduce dot gain on inkjet presses. The technology's emitting units can now reach a peak radiant power of 12 or 16 W/cm, allowing a practical move into mainstream label printing.
How does LED-UV curing stack up when it comes to migration? Don P Duncan, research director at Wikoff Color, places the process in context: ‘In general, electron beam (EB) curing will give lower migration numbers than conventional UV curing, and this in turn will give lower migration numbers than with LED-UV curing, which is still a fairly new concept in this area.
‘As for the ink technologies, energy-curable offset-litho inks generally give lower migration levels compared with UV flexo inks, which in turn produce lower levels compared with UV inkjet inks. This is due firstly to the high amount of cross linking that occurs during curing. It minimizes migration, but creates a high-viscosity ink. Secondly, while higher molecular weight ink components will minimize migration, they also produce higher viscosity inks.
‘Offset-litho inks are very viscous and can maximize both of these factors. Inkjet inks are very fluid and are at the opposite extreme, with flexo inks in the middle. So the hardest thing to do is to make low migration inkjet inks that are cured with UV-LED. Many people are working on it and much progress has been made. For example, they are much lower in migration then they were even two years ago, but currently there are no UV-LED inkjet inks being commercially used for LM food labels.’
As for the hardware, EFI Jetrion was among the first to introduce a dedicated LED-UV inkjet press with the modular, end-to-end 4950LX model. It features Phoseon lamps and inks from Flint Group Narrow Web. The inks are said to be compliant with indirect food contact regulations.
Epson's first single-pass industrial press, the SurePress L-6034VW, offers the technology with inline digital varnishing and high-opacity white using its own LED-UV inks. INX Digital combines water-cooled LED curing on the six-color NW140 inkjet press with air-cooled LED pinning. The parent INX Corporation manufactures the inks and coatings. Shiki's PicoJet features LED curing supplied by Kyocera, which also supplies the print heads.
Although limited to a varnish unit, in 2011 Gallus broke new ground by fitting a LED-UV curing unit on an ECS 340 in partnership with Phoseon Technology. Today it offers the technology on all of its narrow web combination presses. Ink maker Siegwerk in fact demonstrated a six-color Gallus EM280 using iSicura Flex LEDTec inks at the last Labelexpo. The new Screen LEDTec ink series includes a non-yellowing relief varnish with a relief height of 250 microns. It was shown on Codimag's six-color Viva 340 Aniflo waterless offset press (the final Stork screen unit used IST's LED-UV modules). Siegwerk also supplies LED-cured inkjet inks for the Gallus/Heidelberg Linoprint L.
Last year Mark Andy's introduced the ProLED curing system on a six-color Performance Series P3. The system gained it the Label Industry Global Award for Innovation, shared with Flint Group Narrow Web, supplier of the Ekocure LED inks. Another press-related LED-UV offering debuted at the show was Z+ G's offset inks, developed in cooperation with Muller Martini, IST Metz and Integration Technology. Miyakoshi offers its own version of the curing technology on the new variable-sleeve, MHL13A-300 narrow web offset press.
An interesting LED-based development is the curing of adhesives, including the application of cold foils to shrink sleeves. Flint Group, in association with K Laser Technology, has extended its Ekocure system for this purpose. Besides the normal energy-saving benefits, the process allows faster running and curing through dark-colored foils.
Some LM products
Around 30 or so companies manufacture inks and coatings commonly defined as having migration levels below those published in the Swiss Ordinance guidelines, and complying with the EuPIA Good Manufacturing Practices. The major suppliers are a good source of information on the regulations with several offering useful .pdf downloads.
Flint Group Narrow Web's established Flexocure Ancora ink series for UV flexo printing includes Flexocure XS Opaque White for various shrink-sleeve applications, as well as specialty metallics, coatings and adhesives. Lithocure Ancora is a new series of mono-pigmented range of rotary offset inks. Claimed benefits include a high color strength for formulating clean and accurate color matches. They join Ultraking 4500 LM Premium and Ultraking 4600 LM PLAS Premium, the group's latest low-odor and low-migration inks for sheet-fed offset for the North American market.
Zeller + Gmelin's extensive offering of LM inks and coatings for UV-cured letterpress, offset and flexo includes the new Uviflex Y71 for CMYK plus orange, green and violet. Besides offering an expanded color gamut for brand owners' food products, the series also gives users a greater opportunity to match colors produced on HP Indigo seven-color digital presses. (The Adare Group has adopted Z + G LM inks, see Issue 5, page 52.)
Sun Chemical’s SunPak LMQ flexo inks have low odor, off-flavor and migration levels. The company offers full printing guidance and analytical support to help converters meet legislative requirements. Besides updates for offset and UV flexo LM inks and coatings, the company is adding a wider portfolio of enhanced electron-beam curing products for the increasing number of EB-equipped offset presses within the packaging market.
The SunJet division offers LM inkjet inks that meet the guidelines of the European Printing Ink Association (EuPIA) and the Swiss Ordnance on Materials and Articles legislation, They do not utilize materials specifically excluded on the Nestlé Packaging Inks Specification. They comply with the Swiss Ordinance and Nestlé's specifications for food contact materials including PP, and PE, foil and shrink sleeve films.
Durst offers the new inks as an alternative to standard SunJet inks on the seven-color Tau 330 inkjet press. By achieving migration limits of <10 ppb, they are suitable for food, healthcare and pharmaceutical applications. Suitable applications include unsupported foils, such as blister packs, yogurt lids and many more. The press can run with an optional chill roller when running heat-sensitive materials.
Siegwerk's extensive Sicura LM series puts it among the market leaders. A new product is Sicura Plast Nutritec, a low-odor LM series developed for offset printing on film-based substrates for food, healthcare and cosmetic applications. It is paired with Sicura WL Nutritec, a waterless offset version. The company also produces a LM laminating adhesive.
Stay up to date
Subscribe to the free Label News newsletter and receive the latest content every week. We'll never share your email address.