A new digital revolution for the package printer
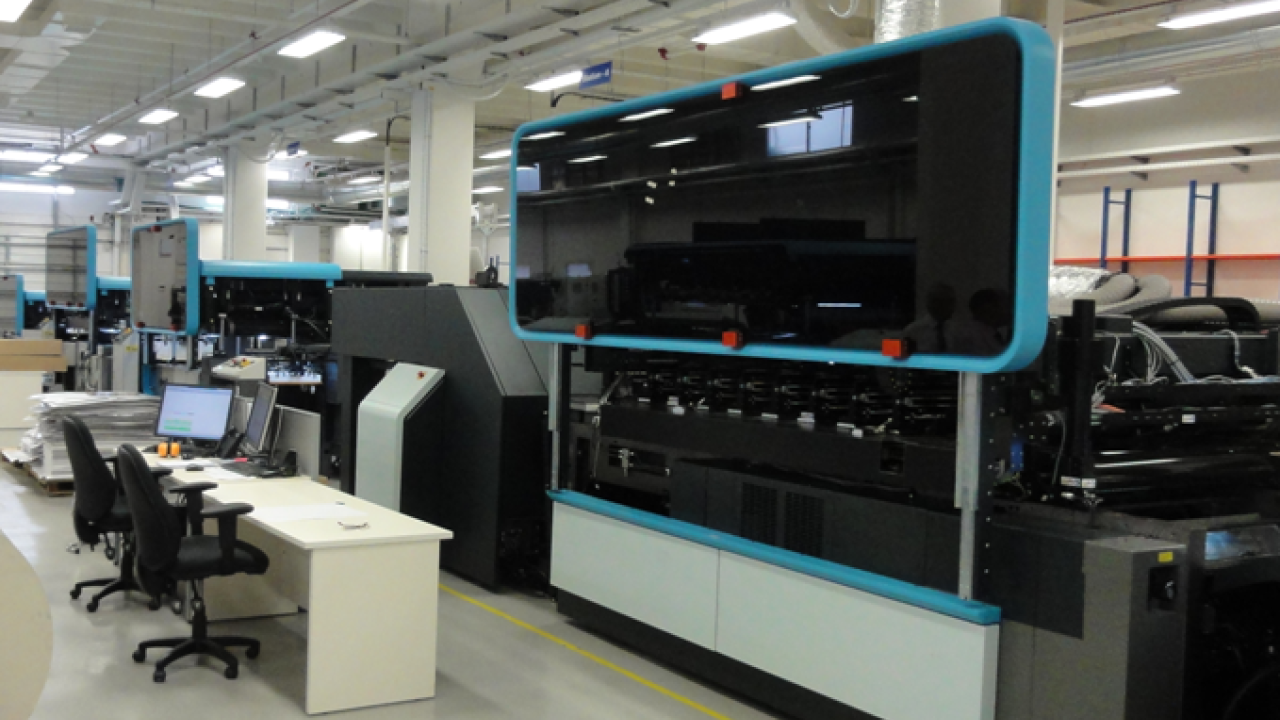
A new printing process that promises much in terms of quality, performance and cost-effectiveness was introduced at Drupa to much acclaim. Mike Fairley visits Landa in Israel to find out more about this exciting new technology.
It’s approaching 20 years since the first print-on-demand digital color presses began to create interest in the package printing and label marketplace; around 15 years since the first early installations, and some 10 years since digital color press sales began to escalate following new, higher performance generations of digital toner presses were introduced by HP Indigo and Xeikon. More recently, interest and installation of inkjet technology has also begun to grow.
Today, there are an estimated 2,000 plus print-on-demand color presses installed worldwide, predominately in the narrow web label sector, but with perhaps five percent or so of installations already being used for some form of package printing – small folding cartons, sachets, sleeves, flexible packaging, tubes, etc.
Few printers in the higher print industry growth sectors of folding cartons, flexible packaging and labels today would doubt that digital color printing – and all that it offers in terms of mass customization, versioning, personalization, enhanced brand protection, consumer interaction – will continue to grow and have a considerable impact on the way brand owners, major retail groups, private label companies and even end-user customers regard their packaging in the future.
Package printers have been slower to adapt to what digital technology can offer in comparison to their label counterparts, not necessarily because they don’t believe in the future of digital printing but because, until now, they have not regarded digital press widths as being wide enough, presses not fast enough, or they have had issues with food contact inks/toners.
Quality of print too, has not necessarily been regarded as acceptable for, say, folding carton production where printers are rather more traditional in what they can achieve.
However, it looks as if the impact and reaction to new digital package printing presses on show for the first time at Drupa 2012 may now at last irreversibly change the way that folding carton and flexible packaging printers around the world begin to view their future press and technology investments. Indeed, some have already placed letters of intent for the purchase of these new generations of presses when they finally hit the market over the next one or two years.
Perhaps at the forefront of stimulating the package printer visiting Drupa into thinking and moving into a digital future was Landa.
Founded by Benny Landa – following the acquisition of his Indigo company by Hewlett-Packard in 2002 – six new generation (three sheet-fed and three web-fed) Landa Nanographic Printing presses were announced at the show to much media and industry acclaim.
Offering output speeds close to offset presses and employing NanoInk colorants that create unprecedented image qualities “Nanography” undoubtedly has the potential to fundamentally change package printing as it is known today – especially when the process is said to offer printers the capability of producing short-to-medium runs at an unmatched cost per page.

Benny Landa (pictured, above with Tarsus labels and packaging group managing director Roger Pellow, left, and Package Print Worldwide international publishing director Mike Fairley, right), chairman and chief executive officer of Landa, states: ‘Nanography is a new technology for applying ink to paper.
In developing our Nanographic Printing process we had to re-think and re-invent the printing press.
‘The result is digital printing with remarkable performance – from a family of presses that share stunning ergonomic design, a small footprint and some of the most advanced user functionality available in the market.’
Certainly anyone looking at the Landa S10 B1 sheet-fed folding carton press (pictured, below) at Drupa cannot fail to have been impressed by its quite stunning design and oversize touchscreen user interface (UI) that claims to allow even untrained operators to quickly master the press.


Able to print single- or double-sided in up to eight colors, plus spot and speciality colors, at up to 13,000 sheets per hour on any off-the-shelf-stock, or straight forward printing (simplex) for folding carton production at up to 6,500 sheets per hour on virgin and recycled carton board, metallized stock and plastic foils, the press is targeted at delivering short-to-medium run lengths at an unmatched cost per page.
Undoubtedly the press will have its place in the carton plant of tomorrow. ‘Landa Nanographic Printing presses are not intended to replace offset printing, but to complement it,’ Landa says.
‘For the foreseeable future, offset printing will continue to be the preferred method for producing run lengths of tens of thousands or hundreds of thousands. But the market is demanding shorter and shorter folding carton run lengths – and that’s where nanography comes in – to enable print service providers to produce those short to medium run lengths economically – at offset speeds. That’s why we say that Nanography brings digital to the mainstream.’
Like the sheet-fed presses, the Landa web-fed presses also print in up to eight colors. The Landa W10 Nanographic Printing press should be of particular interest to mainstream flexible packaging converters as it uses Landa NanoInk, which is expected to be FDA-compliant for food packaging.
This press, which has a 1,020mm (40in) web width, can print single-sided on film stock (12-250 microns) and on paper (50-300 microns) at up to 200m/min (650ft/min), so offers flexibility and performance for shorter run flexible packaging.
A narrower web press of 560mm (22in) width, the Landa W5, is designed for printing at up to 200m/min (650ft/min) on plastic films and shrink sleeves and on label stocks, tube stocks, aluminum foil and paper (50-300 microns). Certainly, label converters have been some of the first to place letters of intent for Landa presses.
At the heart of the process are Landa NanoInk colorants: water-based inks incorporating nano-pigment particles that offer ultra-sharp dots of extremely high uniformity, high gloss fidelity and the broadest color gamut of any four-color printing process.
During the printing process, billions of microscopic droplets of the ink are ejected onto a heated blanket conveyor belt.

This dry film image is then transferred to any kind of ordinary paper or board, coated or uncoated, or onto plastic packaging film, without requiring any pre-coating. The filmic image layer instantly bonds to the substrate surface, forming a tough, abrasion-resistant laminated layer without leaving any residual ink behind on the blanket. Since the ink layer is already dry, there is no need for any form of post-print drying.
The press itself features the Landa Touchscreen, an oversize UI with press controls appearing on both the left and right sides of the screen. The right side is dedicated to job management, enabling the operator to organize job sequences for maximum press utilization. The left side of the screen is dedicated to press functions and shows in real-time the status of all press functions. Because the press is so highly automated it is claimed that a single operator can manage two, three or even four presses at a time.
Having created the interest and letters of purchasing intent, Landa is now working towards the customer fulfillment stage. Machines are being built and installed in its facility in Israel.
These will go through an intensive period of testing, qualifying, learning, materials and quality performance trials, re-evaluation and regulation accreditation over the coming nine months or so, followed by trials with customers and the first beta installations by the end of 2013/early 2014.
Many package printing companies will undoubtedly be watching with interest to see how the trials, testing and beta installations progress before making their own commitments to this revolutionary printing process and market solution.
Assuming everything progresses as anticipated, then 2014 should be a busy and exciting year for Landa – and the beginning of a new era for the world of package printing.
Read more on Landa here
Read more about digital technology here
Read more news from the Middle East here
Read more features from Package Print Worldwide here
Register to receive both the printed magazine and Package Print Worldwide fortnightly e-newsletter for free here
Stay up to date
Subscribe to the free Label News newsletter and receive the latest content every week. We'll never share your email address.