Omet promotes offset
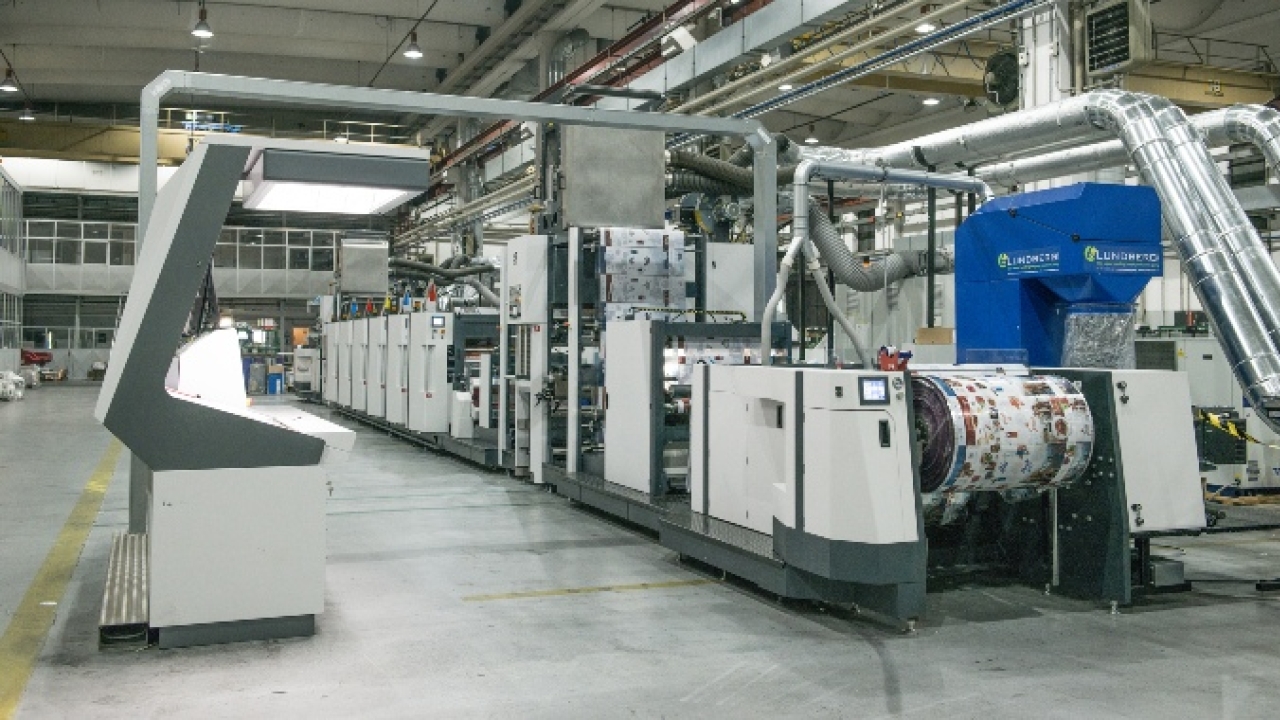
But throughout this time, offset has remained an important technology in both intermittent and rotary formats. Its niche has been at the high end of the print and decoration market, usually for toiletries and cosmetics and high value wine and spirits.
The key advantages of offset in the narrow web industry are superior print quality, cheaper plates, a ready source of skilled operators and industry-standard color matching.
“There are market niches that still need offset, first of all the wine and spirits industry. They have to print the rough and textured papers that the market requires today. We also see offset playing in the flexible packaging market due to the trend towards shorter runs and multiple SKUs”
In recent years the position of offset at the top of the print quality chain has been increasingly challenged by UV flexo, which with modern plate, anilox and automated press technology is certainly coming close to offset quality – although true fades to zero remain the exclusive domain of offset.
So it was interesting to hear that Omet has appointed a dedicated offset business manager, and this seemed a useful opportunity to discover from one of the leading narrow and mid-web press manufacturers where offset sits in its press hierarchy and how it sees the future development of offset technology.
Offset manager
Omet clearly demonstrated its view that offset needs a dedicated business development manager when it appointed Roberto Speri as key account manager and offset business development manager for the Italian market, with particular reference to the Varyflex V4 and X6 offset machines. He will also work at a global level to support the offset sector with Omet’s area sales managers.
The decision to create this role within the company’s Label and Packaging division represents ‘a response to development strategy in the flexible packaging, wine, spirits, and parallel markets where offset combined technology is required,’ said Omet in a statement.
The company is focusing on combining the offset and flexo processes on both the new Varyflex V4 and the XFlex X6. The Varyflex V4 is dedicated not only to flexible packaging, but also in-mold labels, shrink sleeves and folding cartons. The XFlex X6 is targeted at label applications in the wine and spirits market as well as high-quality printing on special substrates such as laid paper and unsupported films. Another targeted application is security printing with the use of special inks and dedicated machine configurations.
‘In recent years Omet has heavily invested in the development of offset technology because we strongly believe in its future,’ Speri tells L&L. ‘The machines currently in production, the X6 at 430-530mm and Varyflex 670-850mm, both have the potential to serve a wide range of end use sectors.’
Speri confirms that both lines were specifically designed to be modular. In addition to offset printing units, the configuration can include flexo and rotogravure, and a range of finishing units including cold foil, rotary screen and flatbed hot foil.
‘In practice these presses are always highly customized depending on the product sector,’ says Speri. ‘For example for wine and spirits labels we usually have 1-2 flexo units, six offset, one flexo, one flatbed hot foil, one flexo, and one die station combined with at least one and possibly two screen units. For packaging we usually have one flexo or one front and reverse rotogravure, six offset units, one flexo EB plus a flexo or rotogravure coating unit. The last flexo group is usually used for matt or gloss varnish or for opaque white, rarely as a spot varnish.’
Speri concedes that flexo technology has taken great strides forward in terms of print quality, fast job change and cost reduction. ‘Even inside Omet, flexo machines are the most requested, but there are some market niches that still need offset machines, first of all the wine and spirits industry. They have to print in a suitable way the rough and textured papers that the market requires today. We also see offset playing in the flexible packaging market where it could become a truly winning weapon due to the trend towards shorter runs and multiple SKUs.’
Talking about the specific advantages of the offset process, Speri cites ‘first the superior print quality – specifically with the Varyflex V2 and V4 we can print wet-on-wet. This way, beyond the superior quality, we drastically reduce paper passes and therefore waste, we reduce other costs thanks to very cheap plates compared to polymers and even more if compared to rotogravure cylinders, and do a faster job change. Now we are talking about less than two minutes per offset unit. Other savings come from modularity, reduced CO2 emissions into the atmosphere thanks to the E-beam drying, and the very wide range of workable materials.’
Speri notes that offset technology has continued to advance. ‘In recent years we have seen many improvements on offset machines from both a technical and practical point of view. To list the most important ones: the increased production speed to 400m/min; the increased print stability on different types of materials; the possibility of transforming the offset unit into a flexo one; and the reduction of set-up and job change times. Over the next five years, our R&D will certainly continue to work to define and optimize set-up times, to reduce even more waste and to balance offset print quality from machine start-up, increasing energy savings and sustainability.’
Automation
Speri also notes the extent of automation in today’s offset print process. ‘Our offset X6 and Varyflex lines have next-gen electronic drives and interlocks. On request, we can also install automatic blanket and plate washing systems, and as a further possibility, the offset unit can be converted into a flexo unit in just a few minutes. Obviously our machines are fitted as standard with all the standard automatic controls, including those for water dampening levels, automatic inking curve, management of the dampening curve, and with CIP3-4 sending PDFs directly from pre-press to the machine, for saving jobs and quality control.’
In terms of possible alternatives to ink/water systems, such as ‘short’ inking and waterless, Speri does not see any particular advantages for rotary presses. ‘Waterless system could be interesting, but it’s limited to the semi-rotary offset machines. Basically, for us the flexibility of machine management – color curve, dampening curve and elimination of ghosting – are key pillars in ensuring overall quality with any image and with any material.’
Turning to flexible packaging, what does Speri see as the advantages of offset compared to central impression flexo, gravure and in-line UV flexo? And what is the preferred web width for offset flexible packaging?
“In recent years we have seen many improvements on offset machines from both a technical and practical point of view: the increased production speed to 400m/min; the increased print stability on different types of materials; the possibility of transforming the offset unit into a flexo one; and the reduction of set-up and job change times”
‘The advantages of offset technology compared to CI in terms of construction and machine configuration are clear: first of all a more developed and structured ink train, especially on the Omet Varyflex, which allows excellent performance on any type of material at high speeds. Secondly, all printing units are independent and easily reachable by press operators, with extremely simple access to each unit both for format change and for any kind of maintenance. Last but not least, different printing technologies can be inserted along the machine including flexo and/or rotogravure units for a multi-process hybrid platform. The latest generation of offset presses, if correctly configured, are the keystone for the medium-small runs where today the big players face handling huge and expensive plates and cylinders.’
As for the ‘perfect’ mid-web width for flexible packaging, Speri says this depends a lot on the market segment and on the presses already serving the production site of the potential customer. Omet has developed two different widths for its Varyflex V4, 670 mm and 850mm, ‘and even if the most popular width for all CI flexo is 1,200-1,600mm, in my opinion the most correct width is the 850mm which contains many of those machine sizes that currently prevail on the market.’
Potential ink migration in food contact applications is a key issue for flexible packaging converters using UV inks. How does Omet’s offset technology respond?
‘Firstly, traditional UV inks are used in all those sectors where there is no contact between ink and food – which is the case for PS labels in general. Wherever inks are in contact with food, we have two alternatives: the first is low migration UV inks, now widely used but not always compliant with current regulations; the second is EB inks with an Electron Beam curing system which is totally green and approved for human food contact, as they are totally free of monomers and oligomers.’
Finally, does Omet plan to launch any new offset or combination offset technology at the next Labelexpo Europe?
‘We have not decided in detail what we will exhibit at the next Labelexpo yet, but we will certainly have some news,’ remarks Speri. ‘I can only say that we are concentrating a lot of efforts on the new headquarters in Molteno and on the Innovation Park demo center.’
Stay up to date
Subscribe to the free Label News newsletter and receive the latest content every week. We'll never share your email address.