Optimized for package printing
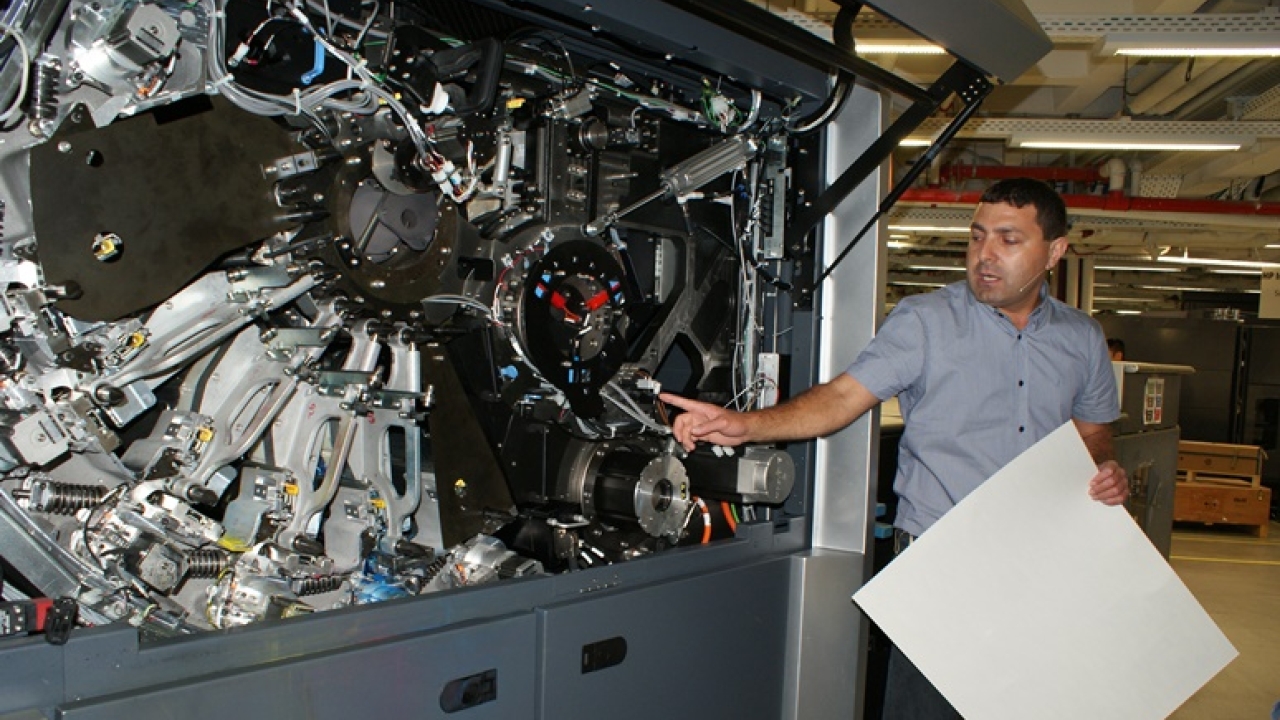
HP Indigo’s new 20000 and 30000 presses have been designed to present printers and converters with optimized digital package printing options according to their requirements. David Pittman reports
In the digital label printing market, HP Indigo is one of the biggest players, with an installed base of more than 1,300 presses worldwide.
The roots for the business were laid in the early 1990s, when Benny Landa debuted his first digital press, the E-Print 1000 at Ipex 1993, before HP acquired the business at the turn of the 21st century.
More than a decade later and Benny Landa tried to replicate the splash he made with the first Indigo press with the launch of Landa Nanographic Printing (see Packprint World, issue #4 2012) at Drupa 2012.
HP Indigo also looked to make a splash at Drupa 2012 with its fourth generation digital printing presses. This included the 10000 sheet-fed press for commercial printing, as well as the 20000 and 30000 models for packaging applications.
In early summer this year, HP Indigo hosted an event in Israel for customers and partners, with around 400 attending from around the world, to officially show the systems to current and potential customers alongside its existing portfolio of digital printing equipment, such as the WS6600.
The HP Indigo 20000 is a 30in roll-to-roll press designed for the flexible packaging market. Support for 30in-wide webs permits a 29in-wide image format and a 44in repeat length. The press can handle substrates from 0.4-10 points, and is capable of printing on film, paper and aluminum.
The 30000 model is a 29in sheet-fed press for folding carton production, and can print on any substrate up to 24 points in thickness, including paperboard, metallized board and plastics.
Both presses use HP Indigo’s ElectroInk technology to produce prints that match the gravure-like color quality standards expected by brands when it comes to package printing, especially on flexibles.
This is achieved with the help of a one-shot color process that collects all the print on the blanket before transferring it to the substrate, so permitting perfect color registration, even on heat-sensitive materials, HP Indigo states. An in-line priming station means both can use off-the-shelf substrates that are prepared on-press for the application of the ElectroInk.
HP Indigo sees the flexible packaging and folding carton markets as genuine avenues for growth, with predicted compound annual growth rates for digital printing of 31 and 50 percent in each market respectively.
Alon Bar-Shany (pictured, left addressing delegates at the global VIP event organized by HP Indigo in Israel to showcase the 30000 and 20000 digital presses), vice-president and general manager of HP Indigo, sees package printing as a largely analog process, so presenting HP Indigo with the potential to transform the market as it has done with labels.
But, he adds, the transition will be more rapid this time around, giving the example that it took some four centuries for a total of one billion books to be reached, yet Facebook took just eight years to reach one billion users worldwide.
Bar-Shany says: ‘The pace of change is different in the 21st century; the internet and access to mobile communications are driving change for everyone all around the world.’
Partners
HP Indigo is working with its industry partners to support this rapid growth, and to develop additional options for both the 20000 and 30000 presses, including an in-line coating unit for the 30000 and a new finishing line for the 20000.
The Tresu iCoat 30000 allows for both UV and aqueous post-print selective coating. Designed to match the HP Indigo 30000 capabilities, this in-line coater will offer an optimized process for the digital production environment.
German die-cutting specialist Kama will also launch a new stripping and blanking unit (SBU) to work with its DC 76, a die-cutting and foil unit with automatic registration camera for a complete, digital compatible finishing solution. The new SBU contains programmable rollers to strip waste and blank printed boxes without the need for expensive tools or cumbersome manual processes.
For the 20000, AB Graphic and Edale have teamed up to develop the Digicon 3000, a 762mm-wide finishing system for digitally pre-printed webs.
The Digicon 3000 will be integrated in-line with the press, allowing one pass for optimized production of labels and flexible packaging. Its modular design will enable users to
produce labels and a variety of flexible packaging laminates.
Edale and AB Graphic together bring over 100 years combined technical expertise; AB Graphic having worked with HP for over 15 years, and Edale with AGFA Graphics for more than 12 years. Whilst the Digicon 3000 will be manufactured by Edale, the machine will benefit from the companies' combined intellectual property.
Early adopters
US printer Nosco has already been named as a customer for the HP Indigo 30000, but a further four printers have now been named as early adopters of HP Indigo's new presses optimized for package printing.
Multi-Packaging Solutions (MPS) and AGI-Shorewood Group (ASG), both in the US, have signed up as customers for the 30000, RAKO-GROUP and Innovative Label Solutions (ILS) will install the HP Indigo 20000.
RAKO-GROUP is one of the largest and most advanced producers of self-adhesive labels in Europe and ILS is a leading US company in the pressure-sensitive label industry. Both companies are already using HP Indigo presses to produce labels and flexible packaging.
Further advances
Alongside the unveiling of HP Indigo’s 20000 and 30000, HP Scitex gave the first showing of its new flatbed industrial press, the FB10000.
Officially launched at FESPA 2013, the FB1000 uses high dynamic range (HDR) printing to enable both speed and quality by combining industrial productivity with 16 grey-level printing.
This combines large ink drops, as associated with faster printing speeds, and small drops for quality printing on the same job. As well as POP, FSDU and other display applications, the FB10000 is suitable for high-quality box printing and eliminates the litho-lam process by permitting direct-to-board printing, with printed products able to be cut, creased and folded to acute angles without the print cracking or chipping.
A number of end-to-end workflow options and product enhancements that span the HP Indigo press portfolio for labels, folding cartons and flexible packaging have also been unveiled by HP Indigo and its partners.
The new HP SmartStream labels and packaging print server, version 4.0, powered by Esko, is designed for simplified color management and automated job preparation. This new color engine transforms existing processes by automating common procedures that are time-consuming.
It also includes new imposition and variable-data tools, including dynamic marks.
Esko is expanding its digital front end (DFE) infrastructure to include dedicated packaging applications. This will enable seamless integration of the HP Indigo 20000 and 30000 digital presses into the production workflow through the Esko automation engine.
Pent up demand
Bar-Shany states that the folding carton and flexible packaging markets are more interested in the wider formats than other markets HP Indigo already serves, so the 30in 20000 and 29in 30000 provide it with an opportunity to grab the attention of new markets.
‘We have a long-term strategy for digital,’ says Bar-Shany.
‘There is pent up demand in the packaging market, but we need to show customers the technologies we have to offer, teach them about those and show them the opportunities.
‘We’re not looking to flood the market, as we have a 10-year roadmap and want steady, sustainable growth. We want to go deep and build relationships with our customers.’
Read more features from Packprint World here
Stay up to date
Subscribe to the free Label News newsletter and receive the latest content every week. We'll never share your email address.