Pressure on productivity? Try automation
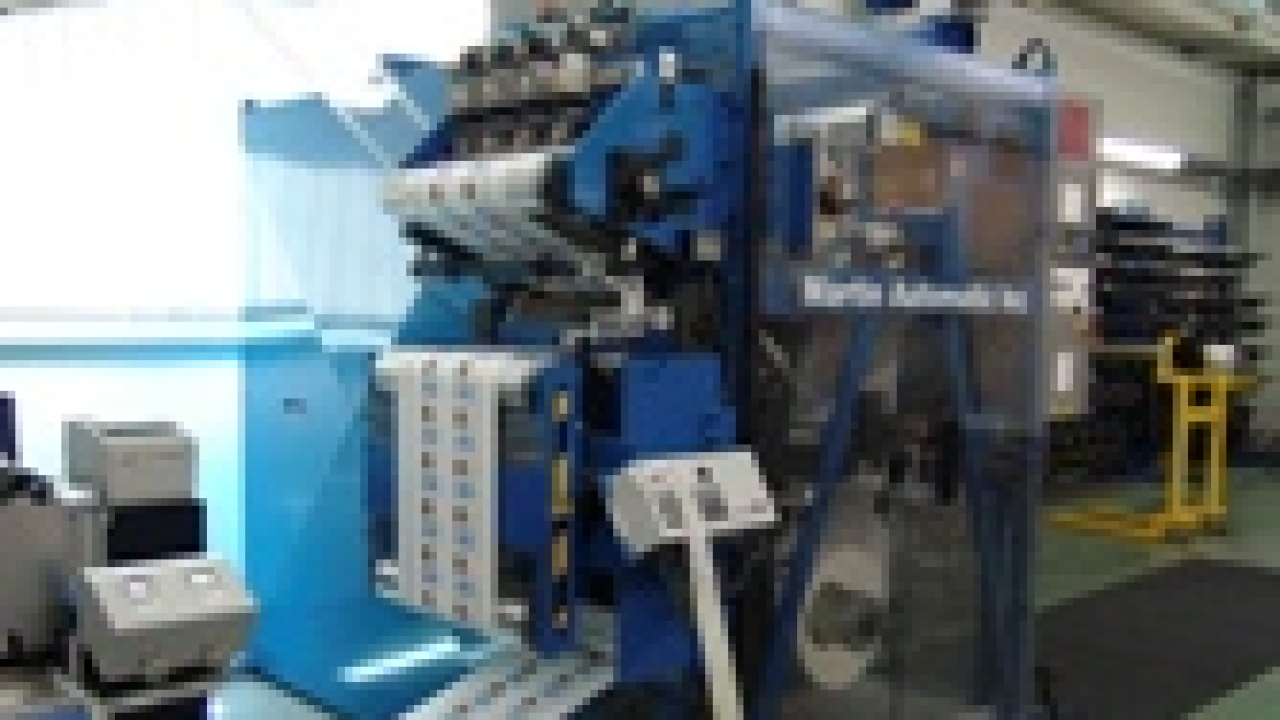
How can roll change automation make a difference to boosting profitability? Gavin Rittmeyer, vice president of sales and marketing at Martin Automatic, tells Nick Coombes.
Current economic data has some indicators pointing up, some pointing down, while others show no discernable pattern at all. Whatever conditions converters and printers face now, they need to focus on key questions that never change. What else can I do to boost profitability? How can I do things better? What tools do I need to accomplish both of these?
In a sound economy, when orders are strong and margins are comfortable, wasteful processes and habits tend to be overlooked. In a soft economy, printers have to look more closely at ways to eliminate wasteful practices to maintain or improve their profitability.
On web-fed presses, material waste is generated every time the press is stopped. Material that is discarded rather than converted to a finished product is both lost potential revenue and wasted working capital. ‘Take a typical web press,’ says Gavin Rittmeyer (pictured, left), vice president of sales and marketing at Martin Automatic. ‘Stopping for a manual roll change will waste at least one press length of material and maybe more, depending on the type of press and work being done. Automating these roll changes can save at least three to six percent, often more.’ He points out that clever printers will also make savings through better use of stock – using a splicer for staging rolls gives faster job changes, and makes more efficient use of butt rolls on repeat or future jobs.
Another factor that may be overlooked or go unaddressed is how much useable stock is thrown away at the end of a roll.
One method of reducing material loss at the core in certain automatic splicers is through the use of a waste reduction system (WRS). This enables a printer to run the maximum useable material from a roll by exercising additional control over the web. ‘The more expensive the substrate being used, the faster the return on investment, so liquid or aseptic packaging, or products made from expensive laminates, like toothpaste or cosmetics tubes, make good candidates for WRS,’ he explains.
Automatic roll changing also improves the labor component of manufacturing.
There are many ROI approaches to calculate how much labor is wasted by changing rolls manually, and how much this could be improved with automation.
Automatic splicing also has a beneficial effect on labor savings in subsequent processes, as one customer comments: ‘A single manual roll change on a print job means over 30m of stock has to be edited out of the print run. It also wastes ink, and we need extra post-press time to edit the bad material out of the final roll.’
Rittmeyer says: ‘I want to emphasize that automating the unwind, rewind and tension control elements of a process is not about eliminating press operators.
Rather, the converter who produces inefficiently – that is, without automation – will find it difficult to stay in business and maintain margins, as he is faced with downward pressure on price and upward pressure from material costs. If he follows that course, he will sustain losses that will force him to cut back on hours, then on people and finally shut down. The objective of automatic roll changing is to avoid this by making existing employees more efficient and productive.’
Improving process
Process improvement can be measured in a number of ways. In terms of net production speed, the addition of automatic roll changing typically results in increases of 10 percent or more. This is because the press no longer needs to slow down, stop and speed up at every roll change. The operators also feel more comfortable running the press faster because they know that roll changing does not require frequent monitoring, or constant brake and tension adjustment.
Measured in throughput, the improvements from automatic roll changing are in the 11-33 percent range.
According to Rittmeyer, one film printing customer, who has installed a Martin Automatic splicer and automatic transfer rewind to his servo-driven press, says: ‘We can now achieve in a day what used to take us a day and a half. It is like adding extra hours of production capacity to each and every shift.’
In addition to pushing work through the press faster, automatic splicing can improve process quality. By maintaining speed and tension levels, images stabilize and color matches are maintained, allowing for optimum impressions from the beginning of the run to the end. And, since there is less chance of a damaging build up of solids on the plates, there is less need to clean the plates during the print run, so they perform better and last longer.
Reducing energy consumption
Running at a consistent speed also has positive effects on curing quality, as speed reductions on UV presses can often result in changes in UV power output and curing intensity. During manual roll changes, UV lamps are typically powered down to 20-25 percent, and the exposure shutters are closed.
These bulbs remain in a standby mode until the press is back up to speed. While the energy consumed in this standby mode may not be significant, the UV bulb’s useful service life is being wasted.
With automatic roll change, the UV system is powered up and stays that way until the end of the run.
‘We continue to study the effects of automated roll changes on power consumption,’ says Rittmeyer, ‘but one German printer recently came up with some interesting statistics by conducting a comparison test to measure the energy consumed by two presses running identical jobs that involved two roll changes. The first test measured the energy consumed with manual roll changes, and the second with automatic roll changes. The results showed an average of 23 percent less power per job and a reduction in electricity consumption costs of €10,000 per year, using automation.’
Extending press life
The evolution of materials toward lighter film stocks has posed a challenge to printers. For some, whose presses may still be relatively young in terms of hours, it is a painful recognition that these presses may have exceeded their useful life. However, for printers whose jobs still run well on an existing press, an investment in automatic roll changing is both affordable and productive, as well as a practical and affordable alternative to purchasing a new press.
‘Older presses tend to lose register during deceleration and acceleration, which results in additional substrate waste beyond that expected in make-ready.
With a splicer that incorporates inertia compensated tension control, additional waste is reduced by the fact that, once up to speed, the press will operate at a stable speed and tension throughout the full run,’ says Rittmeyer.
This problem is less prevalent with newer servo-driven presses. ‘But,’ he says, ‘the increase in quality may be enough to extend the life of an older press and enable the printer to stay profitable.
‘A one-size-fits-all solution is rarely in a printer’s best interest, which is why we ask detailed questions about his production environment and apply sound engineering principles to come up with the most appropriate technology.
Our aim is to optimize an automation package so that it will deliver the best performance and ROI, giving customers exactly what they need,’ Rittmeyer says.
Future – and present – growth
The ability to complete jobs more efficiently and quickly allows printers to take on business they might otherwise turn away for reasons of capacity or profitability. Automating the roll changes enables printers to increase their turnover and their opportunity for more business.
‘I’m not suggesting that automatic splicing and rewinding is the sole answer. A lot of material waste occurs before a stock roll reaches the press. For example, a lean manufacturing analysis of roll shipping, storing, and handling practices may offer opportunities for better efficiency. Training operators to remove outside roll wraps with care, rather than slabbing off unnecessary stock, can save significant money. Even keeping a cleaner shop will net big savings.
‘Many a printer has discovered the value of implementing such no-cost or low-cost improvements, and paid for automatic roll changing with the money saved.’
Stay up to date
Subscribe to the free Label News newsletter and receive the latest content every week. We'll never share your email address.