Q&A: Suresh Gupta
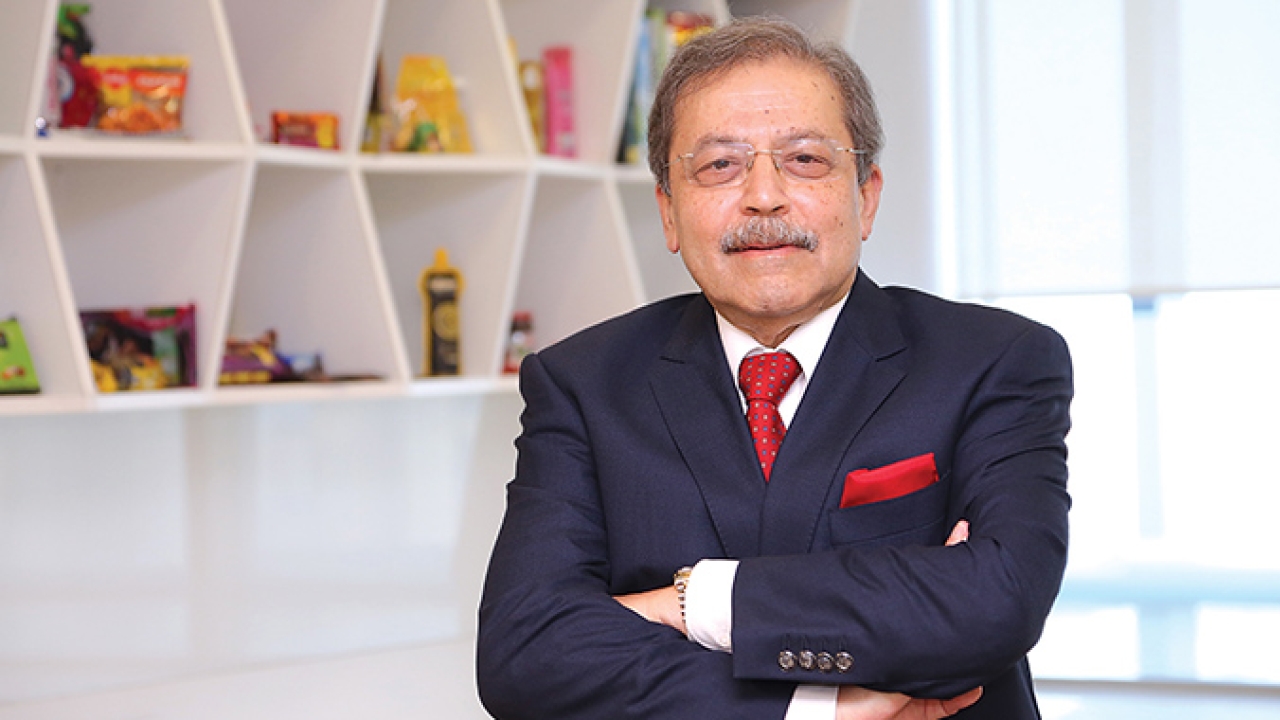
L&L: What is your prediction for the label and packaging industry in 2020 and beyond?
SG: The label and packaging industry is linked to the status of the economy, because we are involved in every sector. The industry is doing better than the Indian economy as we continue to increase the market size and find more usages of packaging such as in e-commerce. Flexible packaging, which constitutes of packs and pouches used to protect and promote products, is currently growing at 5-7 percent in the country in volume. I don't see it shooting up in the short term. The current size of the Indian flexible packaging industry is estimated at almost 40,000 crore INR (approximately 57 billion USD) in terms of value and over 2 billion kilos (2.2 million tonnes) in volume.
L&L: With flexible packaging runs becoming shorter, do you see technologies such as CI flexo and digital gaining popularity in the Indian market?
SG: Technologies to efficiently produce short runs are becoming more popular. Digital, in many ways, is suitable for short runs provided presses get faster and materials become more suitable for flexible packaging in terms of adherence properties, scuff resistance, among other things. Changes are also occurring in CI flexo as well as gravure to make them more efficient for short runs. All technologies including web offset, CI offset and others are being modified to enable short runs efficiently. Downstream processes of lamination, slitting and so on are similarly being modified for short runs. Having said that, a manufacturer can always choose to specialize only in long runs and offer commoditized laminates to customers at the best or the lowest price. So, one has to decide one’s business model. Packaging material manufacturers have to define their own strategy and choose to focus either on short runs, long runs or both in separate factories. Make sure you have the knowledge and expertise to manufacture efficiently if you want to stay competitive.
L&L: Gravure printers trying to print on flexo presses say that gravure samples are tough to match on flexo. And when they do, brands want their other converter suppliers to deliver the same quality using flexo, which is not always possible. In this scenario, how do printers grow with flexo and other new technologies?
SG: I think it's really more related to competence. In 1994, I brought a specific flexo technology to India for printing high quality labels. To start it off, I went all around the world looking at the best quality label printers, plate makers and ink manufacturers. I decided to import plates and inks of a quality which was not available in India. Then we printed on flexo presses and matched the quality of the best gravure printing. A lot of people don't realize that it's little to do with the technology type and more to do with the quality and application of the technology used. Since India has been more of a gravure-based printing industry, the result is a lack of knowledge in the fundamentals of flexo versus gravure. However, this is gradually changing. Some companies are doing some very good work now.
Having said that, printing a label using any technology – gravure, flexo, letterpress, or any other – will result in a slightly different output. Printing is an art and each artist draws the same portrait with a bit of distinction because each hand has a unique motion. If I print on a press that has a certain tension capability, then it is very difficult for another machine with different tension capabilities to get the same registration quality. But the print matching can be very close and to an acceptable level.
L&L: What will be the impact on the Indian packaging industry of the expected multilayer packaging laws and the ban on single-use plastic by 2022?
SG: Multilayer packaging can be recycled. We can segregate materials through chemical processes and divide them into their components. Or companies can use special extruders to convert these multilayer laminates into homogenous pellets, or another intermediate form which can then further be converted into bricks for construction, or other geometrical forms for conversion into pallets, furniture products and suchlike. This business can be commercially viable. Similarly, there are other attractive uses of multilayer waste such as an additive to coal for producing energy, or in enabling stronger road construction, and so on.
More systematic, well-thought-out efforts must be made by Indian society as a whole including, most importantly, the government. But efforts and actions have been a bit haphazard. Instead of jumping into disconnected solutions we need to look at the subject of waste management in terms of simple, real-life actions. To start, are we collecting, segregating and carrying the waste efficiently to centers for further processing by the right methods relevant to the end-use?
We need to make infrastructure process changes which other countries have successfully implemented. For instance, some Scandinavian countries have stopped using coal because they convert all their waste into energy. They have an energy surplus, so they export it. They have run out of domestic waste and are now importing waste from other countries to feed their power plants.
Homo sapiens will cease to exist without good packaging. It is here to stay. It's not so difficult to organize collection, reuse, recycle and disposal as may be needed. Sustainability has become more of a fashion statement among the public. People think they understand the gravity of the situation but they don’t really understand it. It requires huge commitment and resources of the right technology and logistics, applied with common sense and commitment. If the commitment is there, waste management can be a huge opportunity. We need to create the same kind of excitement and enthusiasm as created by the smartphone. This trillion dollar industry around the smartphone is hardly 15 years old but what a revolution it has created in our lives. If only half the effort and resources put into the smartphone ecosystem are applied to an effective waste management ecosystem, we can create a revolution – imagine a planet without waste, the oceans without waste, all materials continuously reused, recycled. When the profitability is seen by everyone, it will happen – the consumer will make it happen. We need education, political will and the combined effort of the people. If smartphones can be a trillion-dollar industry so can waste management.
L&L: Paper versus plastic is a constant point of debate. What’s your view?
SG: People don't realize that paper packaging waste is very dangerous if not 100 percent collected and recycled. For example in India paper is mostly not made to the best global standards. Waste paper lying in the ground has dangerous chemicals, inks and coatings which leach into ground water and poison it. So, there is no 100 percent correct solution to any form of packaging. You have to work on solutions. Once waste is properly collected and segregated, the reuse, recycle or safe disposal process must go into effect in a highly planned and efficient way.
Incidentally, in the late 1980s I was accused of damaging the forests by increasing the demand for paper made from trees. And then, because I worked on plastics in packaging as a better material, I was praised as a savior, but here we are.
L&L: How important is it for the industry to develop and use more eco-friendly materials?
SG: It's very important not only for our industry but for all industries. Consider the amount of plastic used in ballpoint pens, produced in mass quantities, used and disposed without much thought. Take for instance 3D printing – who's asking the manufacturers of powders used in 3D printers if the powders are truly eco-friendly?
In the packaging industry, eco-friendly material is often not used properly. Some companies use 20 percent biodegradable components in a film and companies call it good for the environment. What difference will the 20 percent make?
Biodegradable materials are either too expensive, or they are still lacking the necessary properties for package integrity. Of course, these problems are being worked upon in the larger industry. The point is the amount of resources and effort to find practical solutions. And how much genuine demand is in the market? Demand comes when people want to pay for it. In that context, smartphone companies have done a great job by ensuring that everyone is willing to pay for a smartphone.
Having said that, genuine recycling is going on, but these are small steps that do not make enough of a difference to the big picture. Everyone needs to come together to really be able to make a change. You need the same madness as the demand for a smartphone to really make a difference. But I look forward with hope that things will change and efforts being made will become more practical, logical and produce real results.
L&L: What are your hobbies outside of work?
SG: I am an angel investor and mentor of start-ups, primarily in the social impact space.
I am also a patron and collector of art and support interesting initiatives in this area.
And, of course, I am actively involved with the Indian Flexible Packaging and Folding Carton Manufacturers’ Association (IFCA).
Stay up to date
Subscribe to the free Label News newsletter and receive the latest content every week. We'll never share your email address.