RFID tags aid Reynolds
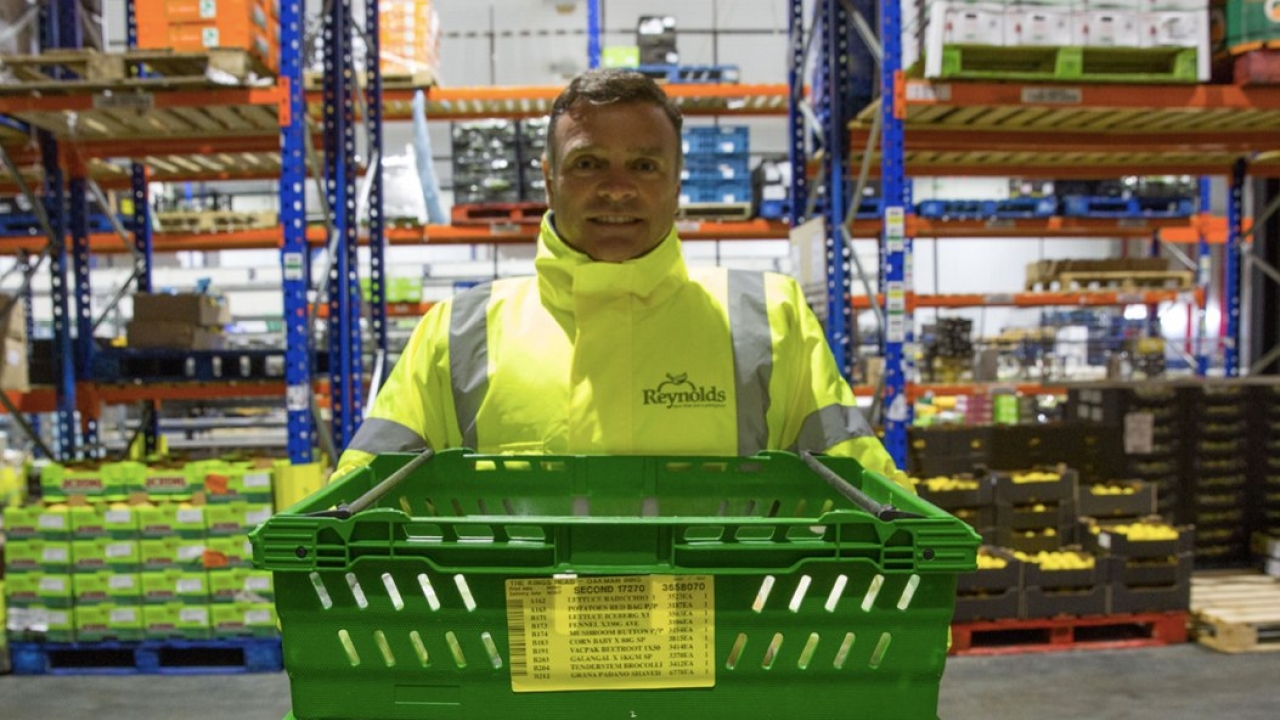
As well as Reynolds itself, many of its customers were also facing increased waste disposal costs and were looking for a more sustainable approach, suggesting a change from cardboard to so-called totes: returnable and reusable plastic crates. Although more sustainable, they cost around ten times more than the paper version. The challenge for Reynolds therefore was to find an efficient way of tracking and proving ownership of the trays, which were often diverted into other organizations or simply not returned.
‘We were packing the goods into sturdy plastic totes because that’s what our customers wanted,’ says Reynolds IT director Richard Calder. ‘Our customers were finding them useful, but they weren’t returning them. It wasn’t just a small number. We were losing a significant sum of money each year, having to replenish crates that just seemed to disappear out of the system.’
Reynolds turned to Avery Dennison to find the best option. It needed a product that would be sufficiently weatherproof to withstand the tray wash process and durable enough to withstand the physical handling involved in customer operations. The company decided to evaluate how UHF RFID could solve the issues.
‘The performance of the AD237 RFID technology was very good and it met Reynolds’ criteria,’ says Peter Jackson, market development manager, food intelligent labels at Avery Dennison. ‘The size was a great fit for the plastic totes with plenty of space for data info. Reynolds uses two identical duplicate tags on each tote to enhance reading performance, minimize potential damage and maximize the lifespan of the tote usage. Each tag can operate independently or as a pair, so it’s a very robust technology. The RFID label does not need to be encased in a protective shield, so operational costs are dramatically reduced.’
In order to increase inventory accuracy, each tray is labeled with an UHF RFID tag as an identifier, which is then read by Reynolds when it leaves for a delivery and is read again when it is returned empty.
‘Impinj RFID readers are built onto the conveyor belts in the distribution center and fixed readers are placed above each dock door to read outgoing and incoming totes. Reynolds uses its own in-house software to manage the entire inventory,’ adds Peter Jackson.
As the crate travels through various stages in the distribution center, it passes several RFID readers before it is loaded onto the delivery van. This helps ensure the crate is correctly loaded with the food items ordered by the customer. Multiple crates are then put together and loaded onto the lorry for delivery.
“Thanks to multi- directional connectivity, we can arrange and control the entire production process ourselves. It saves us a significant amount of time.”
‘Once you have a unique RFID label on each tray, it opens up a world of future opportunities to improve the service we give to our customers,’ comments Calder. ‘The RFID option came at the right time, just as the tags were dropping in price and had become more reliable.’
Integrated system
The system put together by Calder’s team is integrated with the company’s ERP system. This enables tracking the goods inside the crates and the deliveries, ensuring the right crates went into the right lorries for delivery. If the trays are not returned within the agreed time period, follow up action is taken to ensure the customer is billed for the cost of a new tray. Currently, the return rate is close to 98 percent – a dramatic cut in overall tray losses.
‘We are talking of savings of between £100,000 and £150,000 GBP a year on the crates that were being lost,’ adds Calder.
All crates are tracked through the whole process: checked out of the factory and checked back in again when they are returned from customer premises. The tags embedded in the crates are then wiped, checked off in the ERP system, washed and re-used.
Combining tags and readers, RFID provided Reynolds with exceptional benefits across its supply chain by offering a new opportunity to leverage a sustainable technology, reduce waste and enhance its capability to deliver quality food efficiently. ‘The use of plastic returnable crates is fully aligned with our sustainability goals. The UHF RFID tracking system that Reynolds has deployed allows us to ensure the crates are being correctly used in as many restaurants as possible,’ states Guy Croot, head of distribution at Pizza Express, one of Reynolds’ customers.
‘By adding a unique identifier and online connectivity to every item in any inventory, RFID-enabled intelligent labels let grocers, restaurants and convenience stores, dramatically improve inventory management, efficiency, traceability, sustainability and customer satisfaction and have an improved omnichannel infrastructure,’ concludes Peter Jackson.
Stay up to date
Subscribe to the free Label News newsletter and receive the latest content every week. We'll never share your email address.