Right prescription for Erdt Group
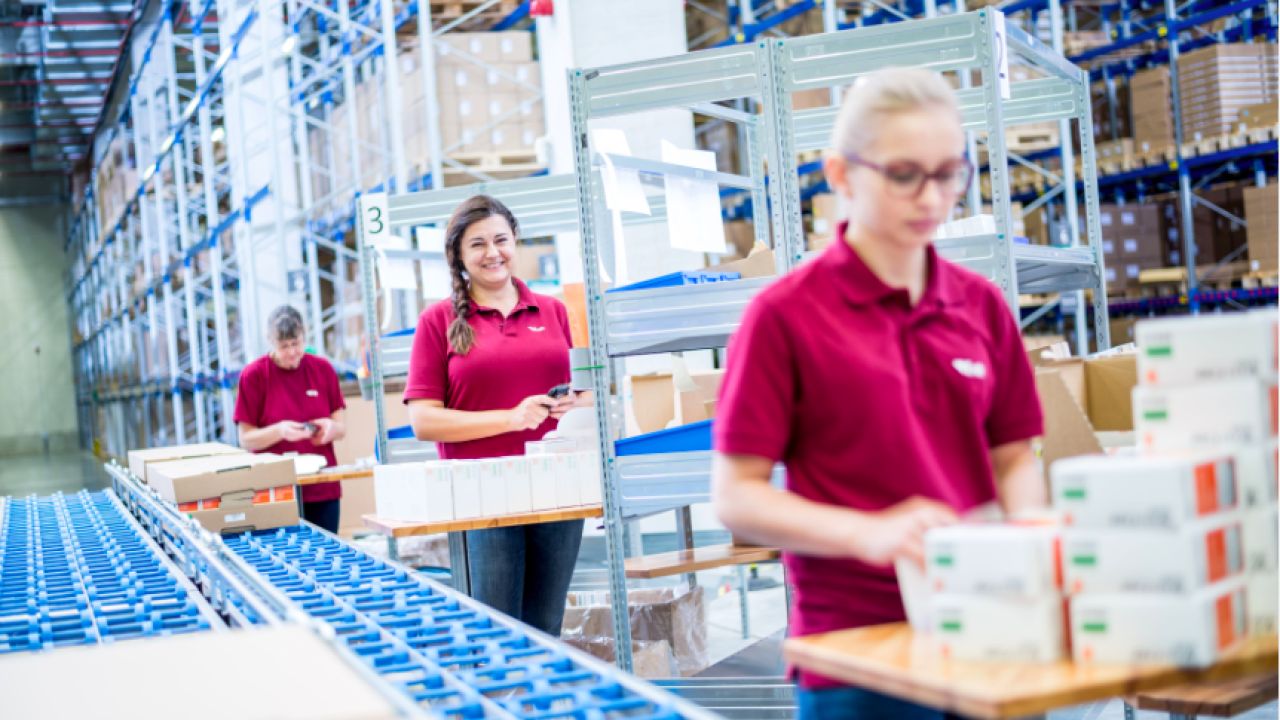
Guaranteeing that labels are legible and compliant can prove labor-intensive, as German logistics and fulfilment specialist Erdt Group found. However, a device from Printronix Auto ID has revamped its validation process and ultimately improved its productivity.
Erdt Group specializes in assembly and contract packaging, particularly of medical devices and pharmaceuticals. It processes more than 60 million items a year from its 14,000sqm logistics space.
Given how highly regulated this industry is, Erdt’s customers expect their logistics and fulfilment partner to be fully compliant. In order to meet directives, statutory requirements, and assembly and packaging stipulations, Erdt uses a combination of semi-automated work processes, state-of- the-art IT systems, and precise manual assembly to achieve compliance.
Robert Beier, director of IT, explains: ‘As service providers we see it as a top priority to fulfil exacting standards, particularly with packaging and labeling of medical products like dressings, syringes, cannulas, infusion equipment or surgical supplies.’
German manufacturers who market their products worldwide need to consider directives not just from the EU but also from securPharm (German initiative to ensure the authenticity of its pharmaceuticals) and the US Food and Drug Administration (FDA). There are also EU regulations for medical devices and in vitro diagnostic, which require products to bear a unique identification number.
The Falsified Medicine Directive EU (FMD), which came into force in February, provides measures to prevent counterfeit medicines entering the supply chain. It requires all packaging to be tamper-proof and to feature a unique identifier in the form of a 2D data matrix barcode.
Legibility, traceability and serialization
Erdt serializes, documents and packages its customers’ medical devices and pharmaceuticals for distribution to pharmacies, clinics and medical practices. During this logistics process, Erdt assemblers and its warehouse and dispatch department print 6-7 million labels a year. ‘We must ensure the printed barcode complies at all times with the requirements and standards,’ says Beier.
Each product label includes a one‑dimensional barcode of the unique Global Trade Item Number (GTIN), and a 2D data matrix code bearing information such as batch number, ingredients and expiry dates. Such detailed labeling ensures each item is traceable and verifiable throughout the entire supply chain. Barcodes must also comply with ISO standards IEC 15415 and IEC 15416 (ISO quality level 1.5) for print quality. Only when labels are 100 percent legible, verifiable and documented do they fulfil statutory requirements.
Analysis by the FDA into the labeling and packaging of medical devices revealed that labeling errors accounted for 15 percent of product recalls. Erdt had found that guaranteeing print quality was a labor intensive verification process that could not be carried out during the print run process itself. Samples had to be taken before, during and after printing to check compliance with ISO standards. The labels had to be physically taken from the production chain, manually measured, checked with an external barcode verifier, and then integrated back into the print job. Separate equipment for printing and verification was necessary to complete the checks, which all required extra manpower and time.
Erdt found that with the online data validation (ODV)-2D thermal printer validator from Printronix Auto ID, it could print and verify labels simultaneously, ensuring that only ISO conforming labels entered the supply chain. Its Viernheim operation switched to twelve Printronix Auto ID T8000 series printers with ODV-2D for its product labeling and packaging area.
Printing is by thermal transfer onto paper labels. Each label is inspected by the ODV function in accordance with the ISO standards IEC 15415 and IEC 15416, and the result of the validation is stored for continuous documentation. If the ODV-2D validation function detects a faulty label, the offending label is drawn back into the printer, overwritten and replaced automatically. This process is documented enabling Erdt to achieve legal security and transparency for its customers, since all relevant information is stored in the database. The ODV Auto ID Data Manager (a module of the PrintNet Enterprise Auto ID software) enables customized, detailed reports to be stored for each print run, right down to the individual label of a batch.
All twelve of the printers were installed and commissioned by AIDC-Box within a short time. As Printronix Auto ID offers all commonly used printer drivers, no changes had to be made to Erdt’s existing IT infrastructure or hardware. The existing Access database controls the printers directly. No additional software is required for the layout and creation of labels.
‘ODV-2D is a unique barcode printer which enables us to not only guarantee a high quality of label printing but also fulfil the strict requirements of our customers,’ explains Beier. ‘By validating and documenting the label printing all at once we have been able to rationalize our processes and increase our productivity.’
Stay up to date
Subscribe to the free Label News newsletter and receive the latest content every week. We'll never share your email address.