Signite sparks PS technology revolution
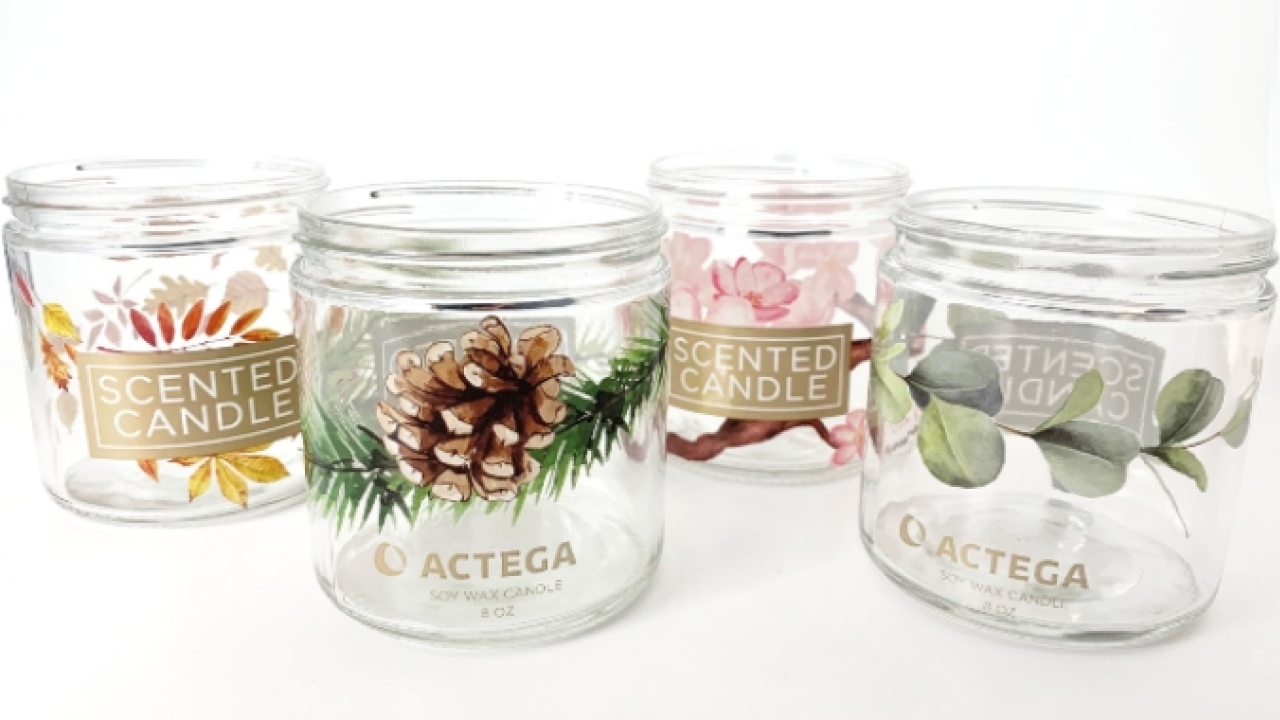
Actega’s patented Signite technology involves printing, in reverse order, a ‘face’ coating, process colors and adhesive onto a double-side coated PP silicone release liner. The first-down coating layer, printed in the exact shape of the label graphic, acts as the ‘face’ of the label and at the same time a protective coating for the print. Next, the process colors are layered down, again in reverse order, and only on the graphics area, followed by a high opacity white and then a pressure sensitive adhesive coating.
When the web is wound up, the top adhesive layer is in contact with the siliconized reverse side of the release liner.
A modified in-line hardware applicator is then required to transfer apply the Signite label decorations to containers. The Signite decorating process is currently commercial for cylindrical, flat walled container shapes such as 750ml Bordeaux wine bottles. Equipment is currently being developed to handle non-cylindrical, asymmetric and tapered glass containers which are more commonly used in distilled spirit glass packaging.
The principle is quite simple: the revolving container surface is brought into contact with the adhesive side and provides sufficient shear force to release the ultra-thin film Signite label construction from its carrier film. Because there has been no die-cutting – the entire label is simply printed to shape – there is no matrix waste.
According to Anthony Carignano, technical director, marketing for Actega North America Technologies, most of the technical development work relating to Signite originates with Actega’s Rhode Island, US-based multidisciplinary applications team, which includes formulating chemists and printing application specialists working hand in hand with inhouse mechanical and electrical engineering specialists.
“We have all this expertise in-house from robotics experts and programmers to electrical and mechanical engineers and chemists and business development technologists. It’s a true multi-disciplinary approach”
Carignano describes the L3 liquid ‘face’ coating layer: ‘It is like an overprinting varnish, but beefier, with more scratch, impact and solvent resistance. A varnish coating would usually be one to two micron in total thickness. However, depending on the application performance requirements, our L3 layer can exceed ten micron total thickness. This is because the L3 is the print receptive backbone of the printed image, which as well allows the image to consistently release from the carrier film.’
The L3 layer is printed as a spot coating for clear-on-clear label applications. It can equally be printed as a flood coating for a full body wrap.
As well as scratch and rub resistance, the L3 coating has been designed with ice water resistance so the labels will not delaminate from glass in an ice bucket.
Signite constructions also exhibit a high degree of heat resistance. Signite label decorations for candle glass applications have been successfully oven tested to withstand two hours at a 230 deg F/100 deg C ambient, with no yellowing, delamination or picking.
Mark Andy hybrid
Actega has historically worked very closely with Mark Andy on new product development projects. Developing the printing side of the Signite process, testing was carried out on Mark Andy’s Digital Series HD hybrid flexo-inkjet press.
‘We use a flexo station at the front end of the press to print the L3 coating then piezo digitally apply pico-liter droplets of full process color and spot Pantone ink onto that “island” to create extremely high resolution images,’ explains Carignano. ‘We then use other flexo stations where needed to add either new performance characteristics, metallic inks or White before the application of a flexo-applied pressure-sensitive adhesive. Think of it as a reverse pyramid-shaped sandwich of films – we’re using a PS adhesive on one side and a standard UV cured coating on the other side.’
Actega’s Signite product development team has been experimenting with different effects by varying the carrier film construction. Carignano says: ‘We have evaluated several transfer film constructions including ablated films which allow for L3 haptic, micro-holographic effects and security features which would be impossible to replicate using other direct or indirect printing technologies.’
Applicator development
Uniquely, Actega also controls the development of its hardware applicator which is key to the commercial success of the Signite label decorating process.
“It is like an overprinting varnish, but beefier, with more scratch, impact and solvent resistance. A varnish coating would usually be one to two micron in total thickness. Our L3 layer can exceed ten”
As we have seen, the Signite process requires that a rotating container contacts the adhesive side of the printed image construction with enough force to shear the L3 layer away from the release liner.
‘The shear forces during transfer to container are quite substantial,’ says Carignano. ‘Registration is the key. To ensure that both on press and on the applicator the tension is just right. It’s like the label decoration waits for its in-motion container transfer bus ride. The printed Signite images are pulled off and away from their bus stop and on to container as containers rotate past.’
The challenge for Actega is that every container surface, whether glass, plastics or metallic, has different surface and contact properties.
During glass container manufacture, for example, a cold end coating is spray-applied or sputtered on to the surface of the glass, creating a network of non-continuous dots. ‘The chemistry of the cold end varies based on supplier and sometimes even country of origin,’ explains Carignano. ‘We have had to become knowledgeable about cold end coating chemistries to make sure we have good Signite transfer and adhesion. Before any given glass container is label decorated we pass it by a two-station flame treater. The flame treatment surface heats the cold end coating to 140-160 deg F. For most polyethylene based cold-end coatings, this is the perfect temperature to give good transfer adhesion of the thin adhesive layer and image onto the glass.’
Actega is achieving application speeds from 35-40 containers a minute on typical 750ml Bordeaux wine bottles. ‘It really depends on the container and the decoration,’ states Carignano. ‘If it’s a full wrap design it runs slower than a spot applied “starburst” design. The size of the glass container also matters. Small micro-glass container vials such as for packaging essential oils can be transfer-decorated much more quickly than 750 ml glass wine bottles 6in (15cm) diameter growlers. The star wheel input area on our hardware applicator is modified to cope with all these different glass container sizes.’
Carignano states that on high aspect ratio glass containers such as religious candle glass, Actega can do a full wrap almost down to the foot of the glass so long as there are no contours or shouldered areas.
‘Many brands ask how we address the rounded areas of glass such as shoulders, and we are working this out,’ says Carignano. ‘A further challenge we have on high aspect ratio glass containers is that they can wobble, so this is something we have had to learn how to control.’
Carignano sees Signite decoration technology as contributing to the overall sustainability profile of glass containers. Signite’s pressure-sensitive adhesive is formulated to meet Thermoform Label Test PET-S-04, the recycling protocol adopted by the Association of Post-Consumer Plastic Recyclers for PET plastic recycling in the United States. Under specific pH and recycling bath water temperature conditions, Signite’s adhesive layer is designed to dissolve and allow Signite decorations to exfoliate away from glass containers.
What’s next?
Actega’s Signite product development team has a huge advantage in being able to call on the resources of the entire Altana group of companies. ‘We are driven by big data, for example in analyzing how a bottle wobbles on the applicator,’ explains Carignano. ‘And we have all this expertise in house from robotics experts and programmers to electrical and mechanical engineers and chemists and business development technologists. It’s a true multi-disciplinary approach.’
This approach means the applicator itself will be a smart, Industry 4.0 orientated system. ‘We dial in the diameter and type of container along with a lot of information about what we are about to decorate, and the system “understands” what’s coming through.’
Actega’s new technology incubator in New England is now deploying Signite directly with small brands looking to get new products off the ground. Applicators are being set up at many points around North America to help prove the Signite process in commercial production environments.
To date, Actega’s analysis suggest that Signite is broadly cost neutral when compared with thin film plastic prime label technologies.
‘Certain areas of the market are ripe for disruption,’ concludes Carignano. ‘This is certainly a more elegant way to decorate than direct-to-object printing. Next, we will be gathering data to develop a lifecycle analysis. It will be critical for Actega to have hard comparative data to share with relevant brands and co-supplier partners for feedback.’
We at L&L will be closely following the development of this exciting technology.
Stay up to date
Subscribe to the free Label News newsletter and receive the latest content every week. We'll never share your email address.