Will hybrid inspection systems challenge line-scan?
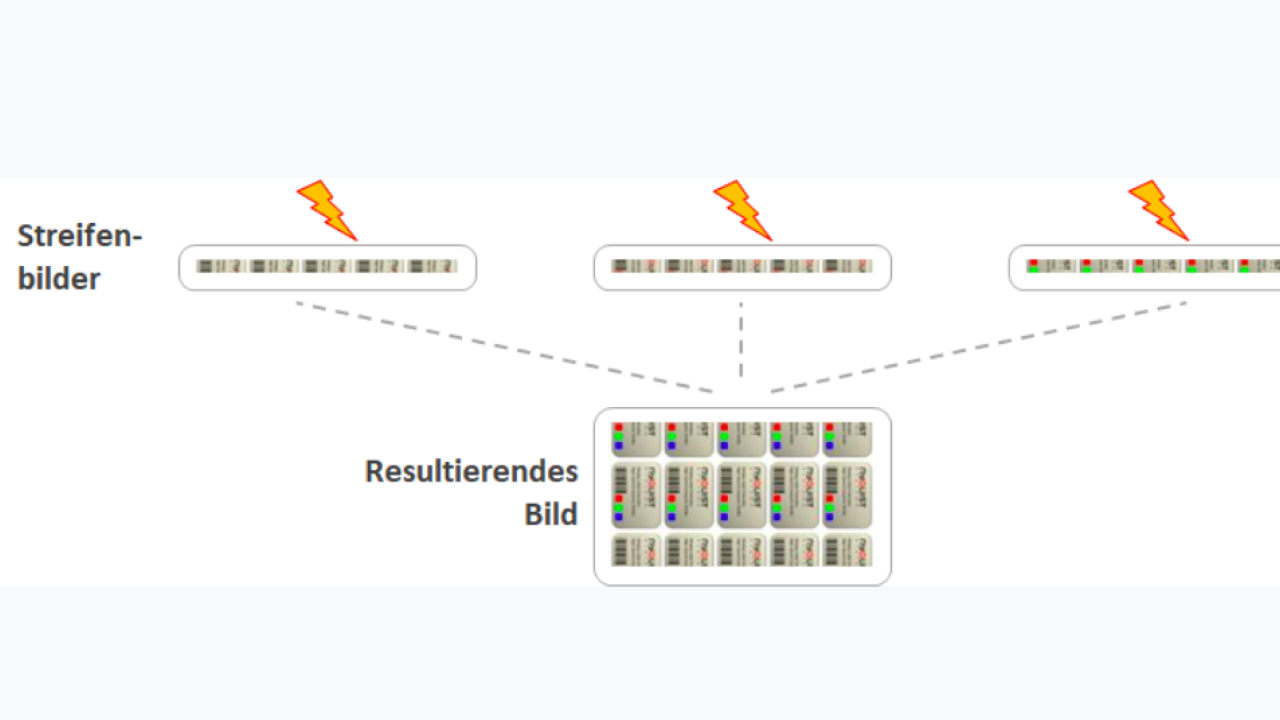
There are currently between 1,800 and 2,000 matrix-type inspection cameras in the field, with users benefiting from their relatively low cost and compact footprint. But does this technology really have the potential to replace premium line scan cameras systems? This question is addressed in the following article.
How the technology works A brief explanation of the underlying technology is necessary. Figure 1 shows the principle. At equidistant intervals, individual stripe images with a height between 3mm and 12mm are acquired and then stitched together in the processing PC to form an overall repeat image. The striped images are recorded using a rotary encoder, which is driven by the running printing web via a friction wheel.
From this representation the similarities to the line scan camera become clear. If a line is interpreted as a stripe image with height ‘one’, both principles merge into each other. For the strip heights mentioned above, one typically obtains images with line heights of 20-100 at optical resolutions of 0.1mm to 0.3mm. Since the recording principle obviously combines the properties of line scan and matrix cameras, it is referred to in the following as hybrid technology. Initially, the image quality achieved by hybrid technology was relatively coarse. Due to the low resolutions and low transfer rates, undesired distortions and shadows occurred at the stripe transitions in particular. However, this effect has been largely eliminated by various development stages to date.
Hybrid technology The main motivation for the use of hybrid technology is the low price of the camera and the associated optics. Compared to line scan cameras, savings of a factor of 2-5 can be achieved. In addition, the size of matrix cameras is significantly smaller than that of line scan cameras, which created opportunities for new, compact housing concepts. Figure 2 shows an approximate size comparison of typical representatives of the two camera technologies, while Figure 3 illustrates the compact integration of a print inspection system into a printing press.
Despite the significantly lower costs, hybrid systems are hardly lagging behind line scan cameras in terms of camera resolution and speed. The camera resolution has increased from 1,200 pixels in the beginning to 4,000 pixels (4k). With a line frequency of 40kHz, the new cameras can meet practically all requirements relevant for narrow web label and packaging printing.
A significant advantage of hybrid technology over line scan cameras is worth mentioning here: since images are always taken in the raster from stripes, the LEDs in the lighting unit do not have to be permanently energized, but can be flashed. This results in a considerably lower current load (reduced by a factor of 20 to 100 at full speed), which has an extremely positive effect on the temperature and the achievable service life of the LEDs.
Visualization function
The operator wants to be as close as possible to the process, both on the press and on the finishing machine. This is why real-time visualization of inspection systems has been improved in recent years. Today it is possible to display the running web as a standing image on large monitors over the entire speed range of the machine, as shown in Figure 4. Repeat frequencies of 20-30 Hz at full HD or even 4k resolution are no problem.
Today, hybrid technology is used on machines where previously only manual inspection was possible due to costs. Once a print shop had decided in favor of one system, the demonstrable cost savings and the benefits for the operator usually led to the successive equipping of further machines. One hundred percent visualization, simple operation and powerful counting functions were the decisive factors here.
Technical advances
With the availability of 4k cameras, hybrid technology has now finally opened up to premium systems based on line scan cameras. Resolutions in the range of 50 micrometers are possible with these cameras and allow applications such as the control of small fonts or QR codes. The main advantages such as investment costs and compactness have been retained. Workflow solutions with inspection on the press and automatic defect placement on the finishing machine are implemented at a reasonable cost using hybrid technology.
A major technical advantage of hybrid technology with matrix cameras lies in the free selection of the image section. For example, a modern 9-megapixel sensor offers a resolution of 4,112 (width) x 2,176 (height). Since only narrow image strips are evaluated, the height is irrelevant at first. However, the cut-out image strips can be placed at any position, which makes it possible to realize different angles to the recorded path via software. This makes it possible, for example, to capture images in both brightfield and darkfield. There are many applications for reflective materials, like Clear-to-Clear and holograms. This can be combined with the independent activation of different illumination sources. Inspection strategies, which previously had to be carried out by independently operating cameras, can now be implemented in a single pass.
LED illumination
LED technology is now used in a range of common illumination strategies. All systems have a diffuse illumination, which is suitable for most applications. If, for example, the outlines of a clear label on paper or plastic substrates are to be made visible, a focused lateral light source, the so-called contour light, is used. Special safety features based on UV-activated pigments can be made visible with a selectable UV LED illumination. The illumination through the web, which for example serves to detect holes in aluminum yoghurt lids, can also be switched on. Figure 5 shows various examples using different illumination strategies.
Validation techniques
Pharmaceutical applications require absolute validation of the inspection process. The quality and consistency of the inspection must be checked at regular intervals, which in practice is often done using pre-printed test rolls with test samples applied in advance.
However, producing such a roll is time-consuming and it has to be replaced quite frequently due to wear or contamination during rewinding.
For inspection systems with line scan cameras, one suggestion was to apply defects in non-image areas of the web and then inspect them using specially defined inspection zones at the start of a print job. This procedure is, of course, quite complex and not always acceptable for the end customer.
Hybrid technology offers a simple and efficient alternative via the matrix camera. Since the matrix camera provides a complete image area in static operation and not just one line, a defect can also be simulated using a template. Figure 6 shows a template consisting of two strips: the upper strip consists of text or graphic elements which correspond to the good state and are taught in as a master. During the inspection, the inspected image area is shifted by the stripe height. As a result, the lower stripe is compared with the upper master stripe. Detected deviations are displayed, whereby the quality of the inspection depends on the set inspection accuracy. Thus different evaluation criteria can also be checked.
Pinhole detection can be achieved even more easily by first learning an opaque master and then comparing it with a template with defined holes.
Stay up to date
Subscribe to the free Label News newsletter and receive the latest content every week. We'll never share your email address.