Workforce woes
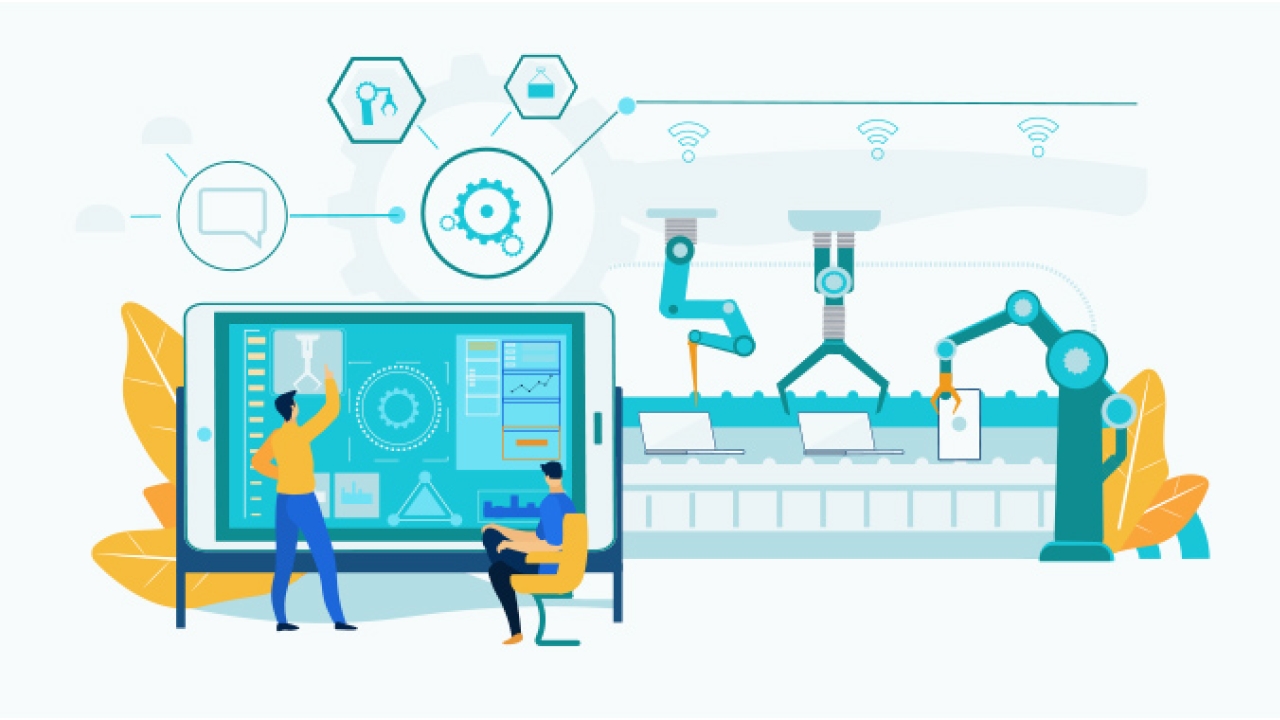
Near-historic low rates of unemployment in the US have created what some experts are calling ‘the tightest labor market in recent history’. It’s not only making hiring incredibly difficult, it’s holding back the industry. All of manufacturing seems to be struggling under the weight of more open jobs than number of people looking for work.
The National Association of Manufacturers says that 522,000 US manufacturing jobs remain open, and a Deloitte survey estimates a potential shortage of 2.4 million workers in the next decade. This hiring squeeze is putting pressure on label converters trying to meeting production demands. In a survey of its converter members, TLMI found that a lack of workers is leading to a production backlog and a reluctance to add capacity. ‘A number of medium-sized converters report that their backlogs are rising due to an increase in sales coupled with the challenge of finding qualified labor that would enable them to increase capacity in order to bring down label delivery times,’ the TLMI report found. In other words, converters are saying they would add capacity – either by adding another shift or adding new machinery – but they simply don’t have anyone to run pressroom equipment.
Can automation save the day?
When it comes to automation, the conversation in the label industry has largely centered around making workers more efficient, but not replacing them entirely. However, as the widespread talent shortage permeates the printing industry, and the skills gaps continues to threaten growth, the conversation appears to be shifting. Equipment manufacturers are responding to label converters looking to find efficiencies wherever possible and to automate repetitive tasks.
‘Finding skilled labor is a challenge for us because it’s our company policy not to poach people from competition,’ said Jai Chandra, managing director at Veepee Graphics Solutions, based in India and Sri Lanka. ‘Therefore, it’s always a struggle to maintain quality and service without skilled workforce, the only other way out is automating processes wherever possible.’
Veepee Graphics employs 100 people in three locations and has always believed in having employees work across departments. Chandra himself works in marketing, business development and finance. He admits it’s getting harder to operate business that way.
‘Customers are getting more demanding and the turnaround times are reducing drastically. The only solution was finding ways to increase the productivity or bloat the team. Improving the work efficiency of the team is an ongoing process in our company, which in turn puts a lot a pressure on the them to come out of their comfort zone and improve their output. We found that this was not well accepted by the older team members who were already used to a certain way of working.’
The National Assosiation of Manufacturers says that 522,000 US manufacturing jobs rmain open
Older workers struggling to adapt isn’t the only issue. Many businesses find it challenging to hire younger workers as an increasing number of press operators approach retirement age. Some companies use digital printing to attract a younger, video game and computer-oriented generation.‘We communicate the digital element of printing and from our experience, our younger operators prefer the cleaner, computer-driven equipment,’ said Adrian Brown, managing director at UK-based Olympus Print Group.
Meanwhile, flexo press manufacturers are making their presses more efficient. Mark Andy has invested in pressroom efficiencies with its automated print head redundancy. Nilpeter is marketing its ‘clean hand technology’ with its machinery. Bobst offers fully automated change overs with no operator intervention. MPS is exploring automated intelligence in its press with its ‘Talk To Me’ connectivity technology. Omet’s automation features include plate pre-registration, multiple-camera registration adjustment and automatic adjustment of print pressure.
Many converters are realizing automation gains on press with inspection equipment, and with front-of-the-house software and workflow systems. L&L’s James Quirk wrote in a review of workflow software shown at Labelexpo Europe 2019: ‘Artificial Intelligence-driven factory automation is key trend, using intelligent systems to help run a plant. The fully automated factory is where we are headed. Not working autonomously but working as a cyber assistant to human skills and judgment.’
Global response
Workforce woes are not a problem unique to one region. Rather, label converters across the globe are lamenting more open positions than people interested in filling them.
In Europe, the shortage has caused hourly wages to substantially increase in recent years, where rates have almost doubled in the last 10 years. According to the European Chambers of Commerce and Industry, there are increasing signals that Europe is headed toward a skills shortage that ‘may impact its competitiveness and create a bottle neck for further growth.'‘Labor costs and lack of skilled workers are the main concerns of European business,’ the chamber said in a report. ‘Europe’s competitiveness is largely built on human capital. This model is not viable if businesses cannot find staff who match their needs.’
In the US, where student loan debt is estimated at 1.5 trillion USD, a career in the skilled trades is offered as a path to avoid that crushing burden. TLMI and its members are reaching out to young people in high school and college to get them interested in print. They have even begun reaching out to primary schools.
Heidi Bollin, co-chair of TLMI’s Workforce Development Committee, says: ‘In the United States that we have a whole generation that went to college whether they wanted to or not, student debt and all. When we talk to high schools and technical colleges, we try to express that we can give you a great career that’s fulfilling with little to no student debt. We want to make sure they know about Bollin Label Systems.’
Finding good, enthusiastic young people who want a career in print is difficult and getting older staff to adapt to digital technology can be frustrating
Many European companies employ apprenticeship programs to find and train workers, like Adrian Brown and Olympus Print Group. The British Printing Federation send assessors to Olympus’ site to ensure that the apprentices achieve the modules required to build their portfolio and that they reach the required level to pass their apprenticeship. ‘Finding good, enthusiastic young people who want a career in print is very difficult and getting older staff to adapt to digital technology can be frustrating,’ says Brown. ‘The days of lifelong careers in an industry are rarer than they were a generation ago. ‘At our company, the number of years employed is not a guarantee of pay levels – ability is. We also suggest a two-week “look at us while we will look at you” work induction which does what it says and enables honesty and sharpens perception both in the office and shop floor.’
Hiring is the one of the biggest threats facing label manufacturing, and one that calls for a comprehensive, thoughtful and measured response. And in the label and packaging printing industries, no worker is more sought after than a skilled press operator. Rob Daniels, president of Georgia, US-based Quality Tape & Label, says: ‘You have to treat your employees like your customers. Because if you don’t have employees, it doesn’t matter how many customers you have, if you can’t produce the product, you’re nowhere. Your employees are as crucial as your customers are.’
Heidi Bollin is president of Bollin Label System in Toledo, Ohio. She has advanced degrees in human resources, which is a big boon in an industry where human capital is so key. She advises being intentional when it comes to hiring. ‘Company culture isn’t built by bean bag chairs and potlucks,’ she says. ‘It’s the daily little things that companies do to build culture. Having an intentional company culture is important. Whether you want to admit it or not, you have a culture – whether it’s good or bad. Once you acknowledge that, then you can start making decisions with company culture in mind and making it work for you.’
TLMI has made workforce development a key pillar in its strategic plan. The North American label association has partnered with Affinity HR as its official workforce partner. The committee also created DIY hiring toolkits to help member with their hiring needs.
European label trade association Finat has developed a Young Professionals Network, designed for members under 40 years old, to have lasting careers in the label industry. Mikaela Harding, president of YPN, and technical sales support representative at Avery Dennison, told Labels & Labeling in a recent interview: ‘Retention of young people in the industry is a massive issue and everyone is talking about it. For our generation, it’s not necessarily about the job, and it is not necessarily about the money. For most of us it is the support we receive from our companies, and the work-life balance.’
Stay up to date
Subscribe to the free Label News newsletter and receive the latest content every week. We'll never share your email address.