Zero-defect production
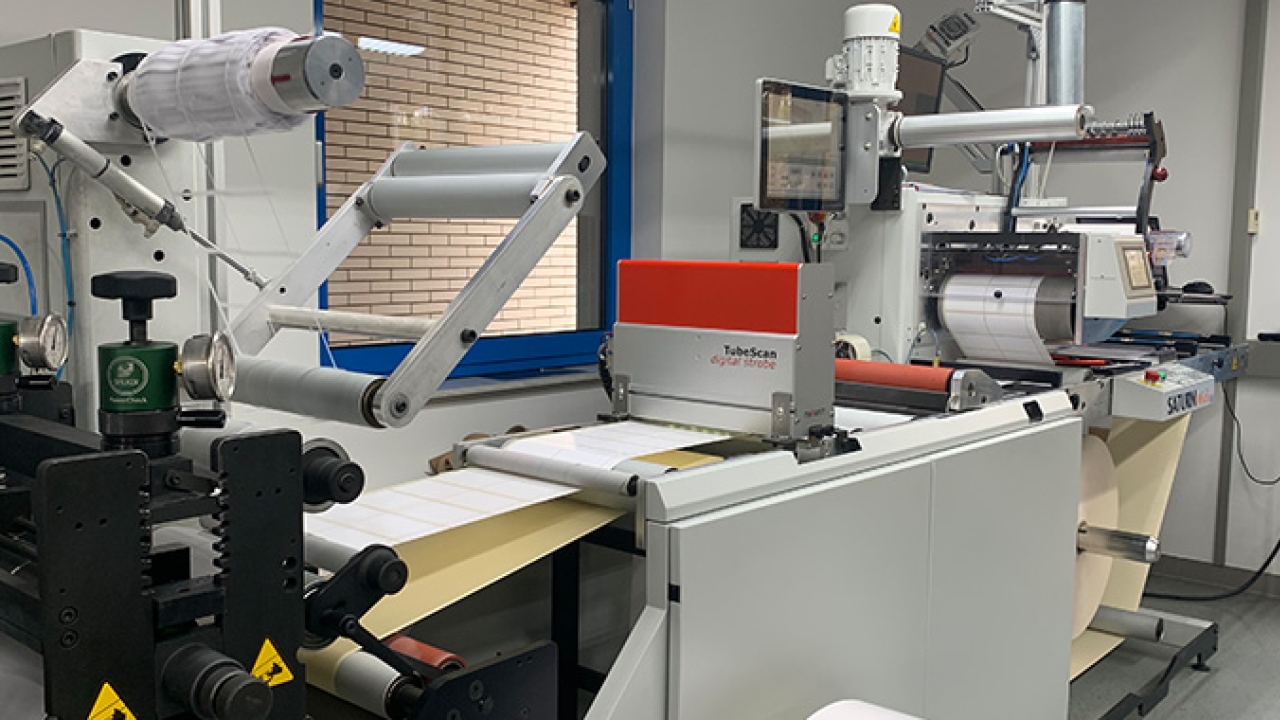
The business has developed significantly over the years and in 1981 the company started producing its own labels. Currently Marschall employs around 25 people and operates five production lines using Mark Andy and Nilpeter presses as well as a wide range finishing equipment including machines from Prati.
‘We provide our services for a wide spectrum of clients, from automotive suppliers, construction and chemical companies, through electrical and electronics, food and beverage and IT, to cosmetics and logistics,’ says Friedel Sellmann.
Many label products leaving Marschall’s production lines are complex and prone to irregularities. Their intricacy often includes detailed graphics and logos, consecutive numbering and barcodes, but also challenging blank labels where error detection is difficult to achieve manually. ‘The requirements and customers’ expectations are growing constantly, therefore we felt there was a need to introduce a system which would add yet another layer of reassurance to our clients about the quality of our products,’ confirms Sellmann. ‘Manual comparison of the printed labels with the PDF files from the pre-press stage sometimes creates bottlenecks in the production process, one that could be eliminated with the PDF comparison directly in the printing machines.’
Quality assurance
The company turned to BST eltromat, based just a few miles away from Marschall’s headquarters and known for its 100 percent inspection systems. ‘Customers come to us with all sorts of issues,’ says Eckart Schmieding, area sales manager at BST eltromat who is directly involved with Marschall. ‘Their production sometimes suffers from irregularities, unnecessary waste, but most of all they want to reassure their clients and themselves that the product which leaves their factory is as perfect as possible. We are not just an equipment supplier, we deliver solutions and always form relationships with our customers.’
BST eltromat analyzed the company’s equipment and came up with a retrofit system which would not only introduce 100 percent inspection to the production line, but concurrently contribute to a significant increase in productivity and reduction of waste.
‘When changing systems in quality assurance, it’s important to keep the machine operators on board and show them the benefits of this innovative technology. Now they no longer need to scan proofs and then compare them with the specifications from the pre-press stage. That saves them a trip to the scanner and the time that this step of the process takes. This way the production process is much faster,’ says the deputy production manager about the new option.
The analysis by BST eltromat showed that TubeScan technology from Nyquist Systems, a member of the BST Group since 2019, were the best option for Marschall. These systems for 100 percent inspection and web monitoring can be used on printing machines or on rewinders. They immediately sound the alarm in the event of deviations from pre-defined target printing values and transfer the data on defects to the rewinders. This enables machine operators to remove the defective labels from the process quickly and in a targeted manner during assembly and packaging. This ensures that only perfect labels are delivered to customers. Costly complaints and refunds can then be all but ruled out.
‘When printing, the TubeScan systems allow us to produce the required quality in a more relaxed manner and let our machines run without worries as long as the TubeScan lights are green. There are still occasional surprises when our machine operators find defects using the TubeScan systems that they wouldn’t otherwise have found,’ comments the deputy production manager.
‘With 100 percent inspection in printing, we’re also minimizing our waste. Our operators can see immediately if defects are emerging and take action to remedy them. We produce the desired quality in a more deliberate manner and, thanks to the counters integrated into the TubeScan systems, we make precisely the needed quantities of labels,’ concludes Friedel Sellmann.
Since the equipment installation the company has been able to avoid reputational damage that would have inevitably resulted from deliveries of imperfect labels to its customers. Minimizing waste, producing desired quality in precise quantities have been also two important factors that have increased the productivity and profitability of label manufacturing at Marschall Etiketten.
Stay up to date
Subscribe to the free Label News newsletter and receive the latest content every week. We'll never share your email address.