Labelexpo Europe 2011 review: Finishing and converting
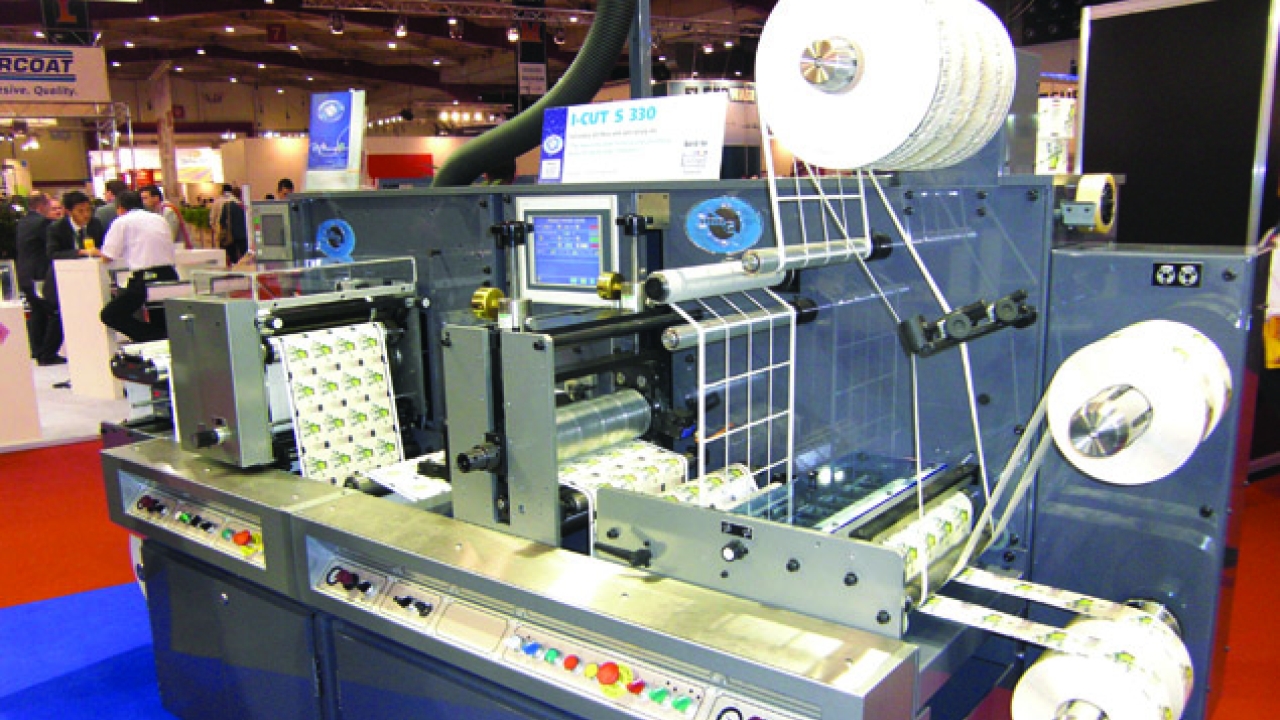
Integration of 100 percent inspection, increased modularity and finishing of digitally printed labels were areas of focus among a raft of developments in finishing and converting equipment at Labelexpo Europe. James Quirk rounds up some of the technology on display
On the AB Graphic International stand two versions of the company’s Omega Digicon 2 label converting lines ran live demonstrations featuring one-stop operation with semi-automatic turret rewinders. One model was demonstrated with off-line turret rewinder to allow machine slow down when the finished roll terminates and the second operated non-stop at full speed and included Nordson automatic gluing.
The new Omega ATR inspection rewinder was also featured. The model is equipped with turret rewinder to allow the operator to inspect the web visually while maintaining non-stop finishing.
Featuring new software upgrades, the Digicon Sabre Xtreme laser cutter was demonstrated running three jobs with non-stop digital die change-over and variable data capability. The system featured digital cold foil application through inkjet technology to apply the adhesive without the use of printing plates and Tidland automatic slit change pattern system for non-stop operation.
Allen Datagraph Systems Inc (ADSI) launched its iTech Centra HS digital finishing system, which is said to be up to four times faster than the original Centra system. The event also marked the European introduction of the iTech Axxis SR digital label system for proofing and prototyping of labels. Allen Datagraph also showcased the iTech Axxis digital label system for printing and finishing short-run labels on a wide variety of substrates.
The iTech Centra HS is a high-speed roll-to-roll digital converting system that allows users to laminate, die-less cut, strip the waste matrix and slit custom labels in one production pass. The iTech Centra HS can convert printed materials from any digital or analog print platform, including inkjet and thermal printers or a conventional flexo press in roll lengths up to 1,250 feet (381m) and up to 14 inches wide (356mm).
Print to cut registration is accomplished via the SmartMark optical registration system. Multiple registration marks can be scanned to automatically adjust the cut file, compensating for any skew or scale issues that may have been caused by the output device or the material. The computer-driven cutting technology is capable of cutting multiple depths within the same cut file allowing for perforations or multi-layer applications. The iTech Centra HS also has a new touch screen interface that makes it easy to set up and operate.
The iTech Axxis SR digital label system allows converters to proof or prototype labels of any shape on-demand, and is also suitable for end users who have short run label requirements.
The system, using an Epson B-500DN inkjet print engine, prints labels at 720 x 720 dpi. With a wide variety of available substrates – paper, polyester and polypropylene – the system can print in widths from four inches (102mm) to eight and a half inches (216mm) in rolls with a maximum outside diameter of 11 inches (280mm).
Ashe Converting Equipment demonstrated an Opal slitter rewinder equipped with a 100 percent inspection system from German company Eye-C, thanks to a new reciprocal partnership between the companies which also saw Eye-C run an Ashe rewinder on its own stand. The machine can process any substrate up to widths of 600mm.
Also on display was a servo-driven Opal 330 with die station for blank and pre-printed labels, as well as a Solitaire filmic slitter which can handle web widths of 400-800mm.
Aztech Converting showed an ISR slitter rewinder with 100 percent inspection from Erhardt + Leimer, and a BSR dual spindle slitter rewinder, which can handle all substrates including unsupported film.
The ISR range has a maximum speed of 243 m/min and the BSR of 228 m/min.
Bar Graphic Machinery showed its latest digital finishing converting line, the BGM Elite FDTR Flexo Die Cut. Standard features are being able to print to re-register, die-cut to print re-register and print to print re-register; the servo-driven print stations are equipped with self-positioning print cylinders enabling automatic print registration set up. The machine is fitted with interchangeable UV and IR curing cassettes, while dual servo-driven die stations with removable anvils enable all converting options to be achieved.
Other models exhibited from the Elite Range were a filmic inspection slitter rewinder, inspection slitter rewinder, rotary die-cutting rewinder and die-cut to register slitter rewinder. By mid-way through day two of the show, the company reported two sales off the booth to L&L.
Cartes launched a new version of its Laser 350 RF laser die-cutting machine. Also on display was Cartes’ HS CombiLaser Series, where laser technology is combined with printing units to create modular machines for label production which can reach speeds of up to 15,000 cycles per hour. The HS CombiLaser Series features different applications such as converting and die-cutting by traditional flat die or laser, UV varnishing, corona and primer pre-treatments, silkscreen printing, hot stamping, embossing, lamination and hologram application.
Cartes reported numerous sales during the show. Belgium-based Femaprint purchased a Laser 350 Dual RF; Lenzlinger of Switzerland bought a Laser 350 Dual; French converter Neo-Color ordered a TFE 350 electronic sheeter; Brazil-based Indústria de Etiquetas Romano opted for a HS203SHH label converting line with hot stamping, embossing and flat-bed die-cutting; and Mexican converter Etiquetas Modernas purchased a HS352SS system which allows fine silkscreen decoration, Braille embossed effects and complete or spot varnishing.
Colordyne demonstrated its new CDT-1600PC (production class) roll-to-roll press dedicated to the prime and secondary pressure sensitive label markets, narrow web packaging and tags.
Show attendees saw for the first time Colordyne’s inkjet system using Memjet color printing technology mounted on a specially engineered web handling system in cooperation with AzTech Converting.
The 1600PC is a 5-color fixed head system equipped with CMYK water-based dye ink, plus a water-based dye pantone spot color capable of running at 32 in/sec, or 160 ft/min on both continuous and pre-die cut materials. Memjet’s printheads utilize nanotechnology that can print at 1600 x 1200 dpi on this system. Memjet-powered printers use Memjet printheads, controller chips and ink. The Memjet printhead is 8.77 inches wide and has 70,400 nozzles that can fire more than 700 million drops of ink per second. With its five printheads, the CDT-1600PC can fire more than three and a half billion drops of ink per second.
This digital inkjet system is poised to tackle two separate pieces of market share. Firstly, the Colordyne system can offer a turnkey solution to brand owners of all sizes that help improve turnover times, reduce inventories and waste and provide a production avenue for more cost-effective full color labels. Since the system is capable of printing pre-die cut materials, the complex conversion step is removed from on-demand label production, thereby streamlining the process.
The Colordyne 1600PC has been designed with flexibility in mind and with the AzTech Converting partnership, label converters too can find the system to be a simplified process, but can additionally customize the converting line by adding stations to the front and back of the digital heads with options to coat, laminate, integrate foiling, stamping and/or die stations to produce more short runs of high-value labels cost effectively.
The way in which the Colordyne system has been designed around low capital, consumable costs and profitability is different from others in the market. Inks, materials and the inkjet head are considered consumables and are factored in as such within the cost model. The Memjet heads in the Colordyne system can be replaced for a minimal cost, which lowers the cost per print.
Convertec unveiled its new modular unit for digital Braille printing for labels. The unit, called DigiBraille, has a modular design that can be retrofitted to any printing press or converting line for either in-line or off-line Braille production. The central impression design allows booklets and labels to be printed with greater accuracy while inspection is also done on the same drum.
The CI unit was possible to make due to an innovative printing head design. The smaller printing head also allows for increased speed and tighter tolerances. The basic software for the new DigiBraille module can handle up to 12 labels across the web, printing up to 24 text lines of Braille simultaneously. The extended software can handle upload of PDF´s and XML data to avoid operator programming errors.
A separate camera inspection system is available that can cross-check the printed Braille text image against a master image. If any errors occur, they can be marked and taken out further down the process.
Daco Solutions launched the Spectrum servo-driven single color flexo press with re-register capabilities. The Spectrum can take digital print from a variety of digital presses, apply a varnish or overlaminate and die-cut to register. It is also capable of producing single color flexo labels and die-cut or using the re-register system add further colors, or just simply die-cut plain labels.
The company’s DTD250 table-top finishing machine has had various upgrades, with an air mandrel for the unwind, a new draw/nip roller configuration, guarding modification enabling RotoMetrics Hydra Jacks to be fitted at a later date by the client and a Daco designed back scoring system. A PLD250 semi-automatic turret rewinder was also on display with upgraded software.
Daco signed an order with Sapir Sprint, Israel, for a Daco DTD250 within 30 minutes of the doors opening at Labelexpo Europe.
Sapir Sprint produces thermal transfer labels for a range of desktop and industrial printers. Sapir Sprint’s Ronen Gidony said: ‘We bought one of the first Daco DTD250 machines back in 2003 when the machine was first introduced to the market. The machine was and still is one of the workhorses of our production facility and we ordered a further DTD250 in the summer of 2011.’
Mark Laurence, sales manager at Daco Solutions, said: ‘Ronen has been a long-standing customer of ours and has grown his business successfully over the last eight years utilizing Daco equipment. I can remember the initial conversation with him where he was worried about technical support with being so far away; it is something we laugh about now: he reminds me that he has never bought one spare part from us or had the need for a service call in eight years.’
DCM Usimeca displayed a non-stop sleeve seaming machine and a quality control machine, alongside a Serval narrow web slitter rewinder and a sleeve perforating and sheeting machine, SleeveCut.
Delta Industrial ran live demonstrations of an integrated web converting and packaging line. The system showed a variety of processes such as island placement, tight tolerance die-cutting, vision inspection and heat seal pouching. The Delta Mod-Tech can incorporate many additional features, allowing the user to create a custom manufacturing and/or packaging system.
Emis showed its Flexor line of inspection slitters, rewinders and die-cutting machines. Flexor STACRW4-12 is a fully servo four spindle turret rewinder with a width of 410mm. Flexor 440IS is a 440mm wide inspection machine equipped with the latest Nikka D1 camera system. Flexor 380 2C+ is a 380mm wide machine equipped with a double die-cutting unit and a re-register module to die cut pre-printed labelstock. Flexor Lexjet 350 is an industrial inkjet machine for printing low volume jobs or variable data, equipped with the latest Konica Minolta KM1024 heads and GEW UV curing.
Emmendinger Maschinenbau (EMB) showed its high speed punching and embossing machine. The company said the machine is being used by customers in the packaging, dairy and beverage industries. It punches small shapes out of unprinted and printed aluminum, paper and plastic foils directly from reels, which may then be used as sealing lids or labels. Applications include sealing lids for yoghurt and pro-biotic drinks and beer bottle neck labels. The machine brings capabilities for embossing, perforating, pin-perforating and doming, and quick changeovers between tools enable easy handling and increased production. The company has developed a shredder, which can be optionally added to the machine, for crushing waste foil into small pieces, allowing for easier suction and collection of the waste.
Errepi demonstrated its automatic cores cutter machine, Vittoria, suitable for plastic or cardboard cores of various diameters and lengths; and its Leonardo 350mm automatic non-stop turret rewinder. The company launched a flexo printing unit, Flexoturbo, which was shown on a 2-color modular machine.
ETI Converting Equipment introduced its emulsion acrylic Cohesio technology, which brings label printers the flexibility of emulsion and solvent acrylic adhesives, as well as hot melt and UV hot melt adhesives, in one Cohesio multifunctional inline coating and printing system. The self-computerized multifunctional printing and coating equipment provides users with the benefits and cost savings of converting pressure sensitive material and/or printing pressure sensitive labels all in one pass.
The company also showed the new Miniliner, an ultra-thin clear PET or BOPP liner of 12 microns which is said to substantially reduce waste and increase productivity. The Miniliner can be die-cut at speeds up to 150 meters a minute and is adaptable to ETI`s Cohesio technologies.
ETI promoted the linerless capabilities of its Cohesio printing and converting equipment that can reach speeds of 150m/min. Linerless technology brings converters direct monetary savings, allows for simple front and back printing, and is a more sustainable option for pressure sensitive label decoration since more labels fit per roll, reducing transportation emissions, and there is no liner waste to be disposed of.
Graficon Maschinenbau showed the new Graficon RPS 220 booklet and processing machine, demonstrating the inline production of booklet labels. A new feature on the machine is the merging of three different pre-printed materials in register. Also on display was the sheeting machine, Graficon BSM 340, for processing from roll to sheet, with new options and extension possibilities such as intermediate cut, waste shift and stacking options.
Grafisk Maskinfabrik showed its new Digital Converting Line 500 (DC500), which can handle web widths from 100mm up to 515mm. The die-cut station is fitted with optional GapMaster by Kocher+Beck. The DC500 comes with UV flexo-varnish station with registration and super-gloss varnish capabilities. It is also fitted with the optional semi-rotary hot foil station with GapMaster that will be demonstrating high quality gold- and silver-printing during the show. GM will also be running various jobs on its smaller digital converters, the DC330, fitted with Zenna laser die-cutter, and the DC330-mini. The entire range of GM digital converters as well as other finishing machinery – re-/unwinders, core cutters, roll lifters/turners, sheeters and waste management machines – were available for testing at the show.
Grafotronic launched its 440HI slitting machine with a 100 percent inspection system from Nikka. The 440HI is a high-speed fully servo-driven machine with new features such as an integrated roll lift, slide control panel and a quick-change knife package.
The company also showed its new Converting Line 380 CL in a modular design that included two flexo units, die-cutting and a new automatic turret rewinder. Each module is servo driven and works independently. Extra units, such as lamination, inkjet, labeling, 100 percent inspection, hotfoil and varnishing, can be added.
HKM showed its 380 and 280 ranges of rewinders. An additional rotary die-cutting station on the HKM 380 inspection rewinder enables production of clean and printed labels, while modular construction offers a wide range of options. The HKM 280 rewinder can automatically stop after counting down a defined number of labels regardless of the machine’s speed, a function which increases speed and productivity.
Impression Technology Europe showed the Rapid Label Printing Systems, as well as launching a new Rapid finishing line. Built around the Memjet printhead, the table-top X1 and the floor-standing X2 printers both produce full color labels at a rate of 18m/min. As the machines run from a standard PC, each label can be unique, making them suitable for applications such as tracking or stock control. With virtually no set-up cost, the unit production cost per label remains the same whether printing one or 1,000 labels. The new Rapid finishing line is expected to include a varnishing and semi rotary re-registering system.
Karlville Development demonstrated its SteamBox portable steam tunnel for shrink sleeve prototyping. The SteamBox simulates the shrink tunnel process by using a progressive steam pulverization system along the container in a transversal movement. The portable unit works for full body applications, half body applications, tamper-evident applications and multipacks, and can be adapted to different sizes of containers. Also on display was the company’s K3-Seaming Machine.
Kongskilde showed its pneumatic trim and waste removal systems for the labeling industry. The company, whose background is in the paper and plastic industries, has developed a system with non-stick components and simple design which is targeted specifically at the label sector.
Kugler-Womako presented new developments for the cutting of plastic labels as well as a concept for efficient label matrix removal for pressure sensitive labels. The company’s existing LabelCut 102, launched 10 years ago, enables customers to professionally convert wet glue labels from reels into strip piles. Its new development, a cutting capability for plastic labels, is targeted to the stringent requirements of this demanding niche market.
The LabelCut cuts plastic labels with a thickness of 50 µm to 105 µm at a speed of 2,000 cuts/min or 200 m/min. Even at the highest speed, the cutting accuracy is +/- 0.1 mm, both longitudinally as well as transversely. The company developed a collating area that makes it possible to collect sensitive plastic labels in strips smoothly and precisely. Even during operation, the collating area can be adjusted from outside to millimeter accuracy.
Another innovation focuses on efficient label matrix removal for pressure sensitive labels. Kugler-Womako’s system for the converting of thinner label webs reaches a speed of 200 m/min and a width of 650 mm, without damaging the substrate.
LeoMat showed the latest model of its digital finishing machine, Digitakt 330 SFR. The Digitakt 330 SFR has a matrix rewind, printing unit, semi-rotary die-cutting unit, an AVT camera inspection system, cutting unit and rewinding unit. The machine is assembled modularly and allows the simple subsequent integration of additional modules like hot and cold stamping, screen printing, additional die-cutting, in-mold delivery system, label dispensing systems etc.
LeoMat also demonstrated its Practice 430 I inspection machine with a new concept on the AVT booth. The Practice 430 I has a matrix rewind, AVT camera inspection, inspection table, cutting unit, two rewind stations and two web advance devices (also suitable for thin and sensitive materials).
Lombardi unveiled two new machines: the modular Screenline finishing machine with silkscreen, hot foil and die-cutting capabilities, and the Synchroline flexo press. Both units featured Lombardi’s new patented doctor blade, the Air Blade System (ABS).
The quick change ABS incorporates what Lombardi calls Hi-DynamiX , a pneumatics-based locking mechanism which automatically and dynamically adjusts pressure against the anilox. The benefits include better ink distribution and more even setting of the blade across the anilox, helping prolong anilox life.
The Synchroline press has a servo driven tension control system which can handle a wide range of substrates, from 12 micron film up to 400 gram board. New features include a pre-registration system for both printing and die cutting units and an innovative register control with an automated ‘gain’ setting which sets the percentage by which registration errors are corrected (how ‘aggressive’ the correction is) depending on the substrate characteristics. The system reads and analyzes error statistics in real-time and automatically finds the ‘best fit’ system parameters. Different settings may be required, for example, at the start and end of the reel.
Martin Automatic showed an MBSC butt splicer for the first time at Labelexpo Europe, on the Labelmen stand.
Gavin Rittmeyer, vice president of sales and marketing, said: ‘The MBSC is the most economical narrow web, short- and long-run splicer on the market, combining an affordable price with high performance and offering great value to converters. We are demonstrating the MBSC working with our STR turret rewinder. Together, they deliver extraordinary waste savings, productivity increases and print quality improvements through non-stop press operation. Significantly, the MBSC splicer and STR turret rewinder at the Brussels show reflect our international presence and global commitment – under a licensing agreement, Labelmen Machinery Company, based in Taiwan, builds Martin splicers and rewinders to sell with their Labelmen presses worldwide.’
Martin Automatic also showed a STS automatic unwind/splicer, complemented by an STR turret rewinder at the delivery end of the press. Both of these units were built by Labelmen, under license.
Visitors to the company's stand saw demonstrations of an MBS butt splicer and LRD rewinder. The MBS provides non-stop splicing in narrow and mid-web processes of a variety of substrates from labels to flexible packaging and carton board. Fitted with a built-in roll loading device – no carts or hoists required – the MBS at the show was equipped with Martin's Waste Reduction System (WRS) to enable converters to run the maximum amount of material from a roll of stock.
The LRD rewinder features a moving cantilevered spindle arrangement for rewinding and automatic unloading of finished rolls. The AC vector drive package, with dancer tension control, adds accuracy and flexibility. The LRD at the show was equipped with a web guide, integrated shear-cut slitting and ribbon separation for winding multiple streams of printed product.
Following the show, the MBS splicer and LRD rewinder will be installed at Albea – formerly Betts UK – in Colchester, England, for the production of laminated tubes.
Newfoil showed the latest addition to its range of label converting and finishing machines: the Newfoil SF330 servo-driven flexographic varnishing unit. Designed for varnishing digitally printed webs, the machine will spot varnish in register or flood coat webs up to 350mm wide. It has optional unwind and rewind units for stand-alone operation or can be interfaced with Newfoil hot foil, embossing and die-cutting machines for inline use. Dual UV and IR drying units are incorporated as a standard feature of the machine, thereby increasing the potential use of the system.
Pantec GS Systems reported increased interest from visitors in its inline hotfoiling technology, which the company says results in lower cost per label and shorter lead times. The company showed its Rhino inline flatbed hotfoil embossing system.
Peter Frei, CEO of Pantec GS Systems, said: ‘We had well-known, experienced printers on our booth who could not believe that our stamping process can really achieve outstanding results on open, structured paper at 120 m/min with perfect register and microembossing structures.
‘High speed with foil saving for large volumes not only allows higher press usage, but economizes foil massively. It is also the basis to go in-line to printing presses for premium wine labels, as Rhino’s revolvable head allows multistroke for single pass manufacturing of ambitious designs, with combinations of foil and blind embossing, still running at a speed of 40-60 m/min. Flatbed hotfoiling allows use of cheaper foils and tool costs are a fraction compared to rotary.’
Perfecto showed its G3 and G4 series of label inspection slitter rewinder machines using brushless servo-driven technology. G4, the newest series, offers maximum slitting speeds of 300m/min and 100 percent inspection at 150m/min. Perfecto LabelSpect (G3 and G4) label inspection slitter rewinder machines complement the 100 percent defect detection system from BST International. Integration of both systems, says the company, results in precise and synchronized stopping of labels on the splicing table and provides ease of operation for the user.
Labelexpo Europe proved to be a successful show for Prati with 21 sales agreed and a raft of new leads generated. The sales went to Italy, Austria, Germany, France, Tunisia, Middle East, India, South Africa and the US.
The main attraction was the servo slitter inspection rewinder Saturn, also in the Booklet version, capable of finishing booklet labels, and the modular Vegaplus converting line, available in 330, 450 and 530 web widths, that provides a platform for rewinding, slitting, die-cutting, overprinting/coating, inspecting operations.
‘If Saturn and Vegaplus were the sales queen, from leads and negotiations we can say that PharmaCheck consolidated its position of unique 100 percent label inspection system that meets the strict requests of the pharma industry, while the new Digitplus proved to be a reliable solution for finishing and laser die-cutting of digitally printed labels,’ said Chiara Prati, sales director at the family-run company.
Labelexpo provided Prati with the opportunity to introduce the new Saturn Linerless. The sustainable version of the slitter inspection rewinder features two interchangeable rewinder shafts to rewind the lanes in an alternate mode, to avoid rolls sticking. This enables it to manage the production of linerless label webs.
Label converters specializing in the beverage market were interested in the demonstration at Labelexpo of the Jupiter equipped with Proxima, the advanced detecting system. It delivers improved operator usability with clear labels, even at the maximum machine speed.
Roland DG presented a range of combined printers/cutters. All these machines allow proofing, prototype printing and printing of small label runs.
Roland DG showed its UV machines that, thanks to LED-UV technology, print on all standard label materials. The lamps don’t produce heat so printing on heat-sensitive materials is possible. The UV printers are available in widths from 76 up to 163cm and feature up to six colors: CMYK, white and transparent. This transparent ink creates matte, glossy and relief effects such as Braille and structures.
The company also demonstrated its printers/cutters with metallic silver ink. The VersaCamm VS series is available in widths from 76 to 163cm and the new VersaStudio BN-20 is 52cm wide. All these machines are able to print hundreds of metallic colors. The VS machines use CMYK, metallic and white ink, while the BN-20 only uses CMYK and metallic ink.
Rotocontrol received 18 orders for its slitter rewinders during Labelexpo Europe. The company says the orders were a mixture of repeat and new business from converters in countries including the UK, Germany, Turkey, South Africa and Jordan.
Rotocontrol launched the EPOS option (electronic knife positioning system) at the show, which fully automates the slitting set-up reducing job change time to less than a minute, even with shear systems using upper and lower blades.
The company also showed its RSC vertical inspection slitter rewinder, RSD die-cutting, RSP single pass 100 percent security inspection and the EDM200 over-printing press. Servo drives from Bosch Rexroth assure precise, automatic tension control and high speed.
The company launched its SVS (Sensing and Verification System) option, which features powerful algorithms to detect repeated printed images on most material types including clear on clear, IML and butt-cut labels to provide missing label and matrix detection feedback to the machine.
Also featured was the Vacuum Splice Table option enhancing operator efficiency by automatically placing mill-splice/flags, matrix/missing labels and vision detected defects right on the vertical inspection plate for reworking.
Rotoflex displayed its most popular finishing models at Labelexpo Europe. The stand featured a VLI 440, two VSI 330s and a DSI 330, allowing attendees to see a wide variety of inspection, slitting, rewinding and die-cutting capabilities.
For the first time in Europe, each of the machines had an operator-friendly Genesis advanced control system. Created and developed exclusively by Rotoflex, Genesis is available on all Rotoflex inspection rewind machines. With a simple HMI, operators can monitor all functions and clearly identify faults and issues from a single screen. Integration of the system into multiple machines on the production floor allows operators to easily transfer from one machine to another without relearning the complexity of a new control system.
The advanced system can detect missing labels in multiple lanes as well as detect the presence of a matrix. With multi-lane counting, the converter gets accurate label counts for each roll. The capability to count and inspect a variety of label shapes – not just squares or rectangles – results in an accurate count of labels per lane, regardless of varying label shapes or lengths.
Live machine demos were held daily with rewinding experts demonstrating how converters can take control of their workflow by incorporating Rotoflex technology.
Schober unveiled an addition to its RSM line of rotary die-cutting machines, the Spider, a high-speed automated stacking and counting system for stacking large IML products at a web speed of up to 50m/min. The equipment can handle different types of products with exchangeable, product-specific pick-up plates, taking up products with synchronized speed and stacking them non-stop into a dual piling cassette system. A 100 percent product inspection system with discharge facility of bad products is also available.
Serlem demonstrated the CFB 550, an offline machine designed for the production of labels from reel to stack of various shapes and thickness. From the printed reel, it can cut materials such as OPP, PVC or paper. The machine is particularly suitable for IML production.
Smag reports that it received five orders for its I-Cut 330 digital converting machine during Labelexpo Europe. The machine was launched at the show.
The I-Cut 330 is designed to be used offline and offers high speed varnishing and die-cutting. The company says that the machine is attracting interest from digital label converters because of its accessibility and high speed changeovers – claimed to be just three minutes and thus making the system a viable option for printers who have many short run jobs. One new customer will be Lenzlinger Etiquettes, based in Neuchâtel, Switzerland, which claims to make 30-50 job changes a day. The company will be using the I-Cut 330 to support its four HP and Xeikon presses.
Soma Engineering featured demonstrations of its Pluto II slitter rewinder and Bulldog offline die-cutter. The new 1350mm wide Pluto ll slitter rewinder is designed to reduce waste and down times. With its larger unwind and rewind diameters and simplified job changeovers, Pluto ll is a high performance machine for long runs with in-built features for operator comfort. These include automated slit edge removal, ‘knife positioning assistant’, shaft-less unwind system with integrated loading and programmable rewind core positioning.
The Bulldog die-cutter is a roll to stack, off-line machine optimized for producing aluminum and plastic foils and laminate lids for in-mold labels, beverage labels, yoghurt cartons and similar applications. Print to die registration ensures high precision cuts with optimum edge quality. The flatbed die-cutting system consists of multiple long-life dies that also permit punching of different configurations at the same time. Depending on the shape of the lid and the number of die tools in use, typically up to 75,000 lids per hour can be produced and delivered to the stacker.
Spilker showed high-precision cutting and stamping tools as well as special purpose machinery for rotary cutting and converting. The company unveiled its newly developed converting machine series S-Con Vert, which offers digital adjustment of the longitudinal cutter for a comfortable adjusting of the machine and a significant reduction of material waste.
An integrated new roll-handling-system enables it to perform the role change without lifting the material. The S-Con Vert 550 has a simple manual inspection and optional 100 percent inspection system. Spilker also showed its modular S-Con Starline 550, which allows various cutting, embossing and laminating processes to be combined.
Starfoil, a Netherlands-based manufacturer of finishing equipment, demonstrated the ValueLine 1300 spooling-slitting machine and an efficient foil cutting machine, as well as a new cantilevered CLC-400 machine, designed to spool or slit three inch hot-stamping rolls to one inch or three inch rolls by means of shear slitting.
Systec Converting showed its complete range of plate mounting machines, including a plate mounting machine for printing cylinder technology equipped with auto-focus color cameras and a zoom factor up to 270 times, and a plate mounting machine for sleeves equipped with high definition cameras.
The company introduced a new machine with four cameras, tape dispenser and nip roll – which avoids air bubbles between tape and support – equipped with Systec’s REP suite software. It allows the importing of the repro file for mounting and for virtual proofing with no inks.
Pictured: Smag took five I-Cut orders during Labelexpo
This article was published in L&L issue 6, 2011
Stay up to date
Subscribe to the free Label News newsletter and receive the latest content every week. We'll never share your email address.