Laser powers investment
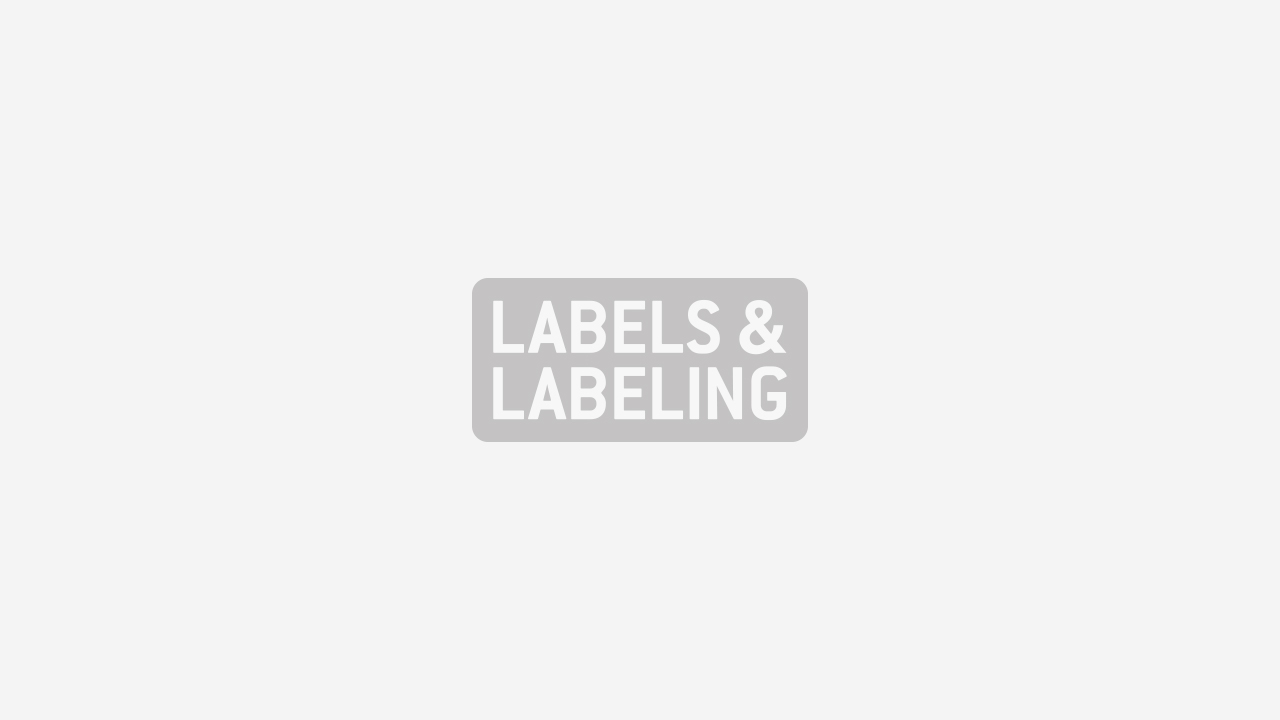
A major investment in laser technology is set to propel Cheshire Anilox into the premier league. Carol Houghton reports
In the last 18 months Cheshire Anilox Technology has undertaken a major investment in new coating, finishing and laser equipment. Managing director Paul Smith says the one and half million GBP project will ‘ensure sustainability and improve quality and deliveries’. He continues: ‘It also offers Cheshire access to the latest coating and engraving technology to ensure we can stay at the forefront of anilox innovation for many years to come’.
The most recent installation is an Applied Laser Engineering (ALE) Fibre laser. The 500W laser will allow Cheshire to produce high quality bespoke engravings to suit challenging flexo and coating applications.
The four and a half meter Fibre laser system is equipped with multi-beam technology for high precision and high quality engraving with fully programmable cell geometries. It can produce engravings from 25LPI-2000LPI and features a custom pulse mode which enables graphical control over the creation of bespoke cell shapes.
In addition, the latest MAD engraving mode enables more types of engraving and improved precision. Paul Smith says this results in optimum cell release characteristics and ‘absolute engraving consistency’ with less than one percent cell volume variation across the roll surface. Sonia Arcos, sales director at Cheshire Anilox Technology, says ‘The new Fibre laser is finely tuned and can engrave down to a micron. We have noticed the bottom of the cell is smoother, making it more efficient at releasing ink at a high line count and still achieving the desired density and vibrancy’.
Arcos expects the new laser will cut production time by up to one third and increase current capacity by 30 percent to 800 rolls a month (depending on size). ‘With the old Fibre laser the parameters need to be set by the operator while in the new laser all that is done automatically. The operator just programs in the design and the laser follows it, ensuring the highest possible consistency.’
Having used ALE laser technology for more than 15 years, training for this latest installation was minimal. ‘The operators needed to learn how to program the software, but this was easy enough,’ says Arcos. The machine was put straight into production with the appropriate quality controls.
The purchase is described as a ‘historic moment’ for the company. Arcos adds: ‘It is the evidence of Cheshire’s long term commitment towards continuous improvements in quality and service as it continues its expansion in the global flexo and offset markets.’ The new equipment will help converters looking to move into high definition flexo work, as Arcos notes: ‘Many flexo applications struggle to compete with rotogravure and offset but with this new technology, it is possible to produce up to 2000 lines per inch, which is ideal for HD flexo.’
Chain reaction
The purchase of a new and more efficient Sulzer Triplex Pro 200 coating machine last July highlighted the need to increase engraving capacity. ‘Increasing efficiency in one area pushes investment in the next,’ says Arcos. Following the Fibre laser, the next investment will be a new grinding machine, expected within the next few months.
With its improved efficiency, the company hopes to tackle new markets, particularly the ‘extremely competitive’ flexible packaging arena. Arcos notes that all new machines for flexible packaging now come with a sleeving unit. She predicts this is also the future for narrow web, dictated by the press manufacturers.
With the recent surge in demand for high release engravings and a consistent growth in sales, Cheshire is beginning to run out of space in its current premises. With great foresight the company laid foundations for an extension before it even moved into its current premises in 2000. This means full production can continue undisrupted when the time comes to develop the 60,000 sq feet site.
Company profile
Cheshire Anilox Technology was established in 1992. The company’s main market is label converters (30 percent), followed by flexible packaging and corrugated board (both 25 percent). The remaining 20 percent of business supplies coating rollers for offset presses.
Exports account for half Cheshire’s business, mainly to Europe and Asia. Sonia Arcos adds, ‘India is a huge potential market but we need to overcome cultural differences to succeed there. Distance also presents a challenge and we are working to develop more partners in the region. We are just scratching the surface at the moment.’ The US is already well supplied for locally, so is a much tougher market to enter.
Pictured: Installation of the new Fibre laser at Cheshire Anilox Technology
This article was published in Labels & Labeling issue 1, 2013
Stay up to date
Subscribe to the free Label News newsletter and receive the latest content every week. We'll never share your email address.