Canadian Lorpon Labels installs HP Indigo 6900
Lorpon Labels of Canada has doubled its digital label production capacity with a new HP Indigo 6900 digital press, improving agility to deliver labels with fast turnaround to support the upswing in demand for food packaging.
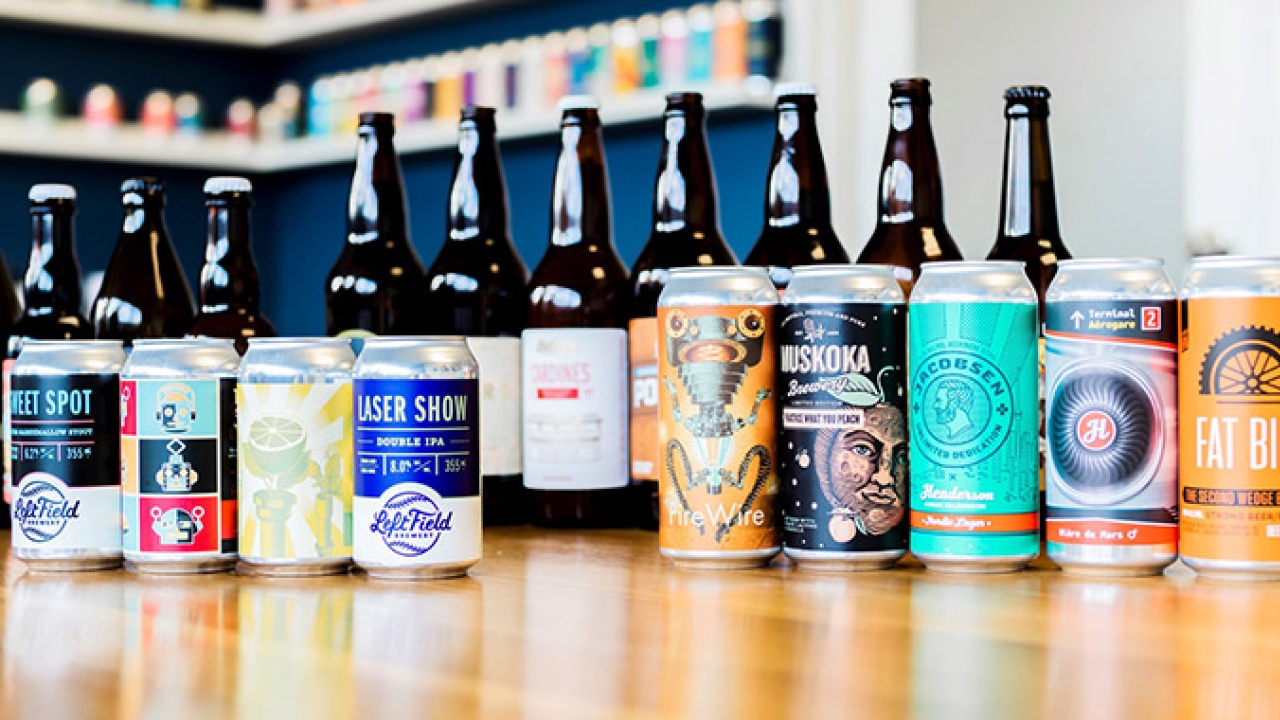
The Toronto-based converter, supplying to the wine and spirits, beverage, beer, food, and cosmetics industry, has experienced nearly a 70 percent increase in orders during the pandemic, as food suppliers scramble to restock stores.
‘Covid-19 brought unexpected demand for labels. The addition of another press gives us flexibility and allows us to continue to deliver fast turnaround times in a period of dynamic supply chains,’ commented Jeff Sommer, VP of business development at Lorpon Labels.
The HP Indigo 6900 installed at Lorpon is a new-generation press supporting the HP Production Pro for labels and packaging print server for high productivity, variable data processing and color matching. According to HP, the digital front end offers up to five times faster RIP power for more jobs per day and faster turnaround.
‘Our partnership with HP offers the ability to serve new and existing customers in a manner we cannot achieve with any other technology, adding to our fleet was the best path to successful growth,’ added Sommer.
With digital printing, Lorpon has shifted its business plan from providing industrial commodity labels to a company that can compete as a provider for global brands.
‘We gave small to medium size businesses the chance to compete with big global brands and over time, these brands grew and brought big brands to us,’ said Sommer.
The media range of the HP Indigo, able to print on textured wine papers and special substrates such as metallic and wood veneer, is especially appealing to the wine and beverage industry.
As Lorpon grows its HP digital business, it is taking advantage of HP PrintOS Print Beat, a cloud-based PSP management, to monitor the productivity of the presses in real-time, identify issues, and keep press uptime to a maximum.
Stay up to date
Subscribe to the free Label News newsletter and receive the latest content every week. We'll never share your email address.