Mission Labels improves efficiency with RotoRepel
Sussex, UK-based Mission Labels has switched to using RotoMetrics’ RotoRepel non-stick coated dies.
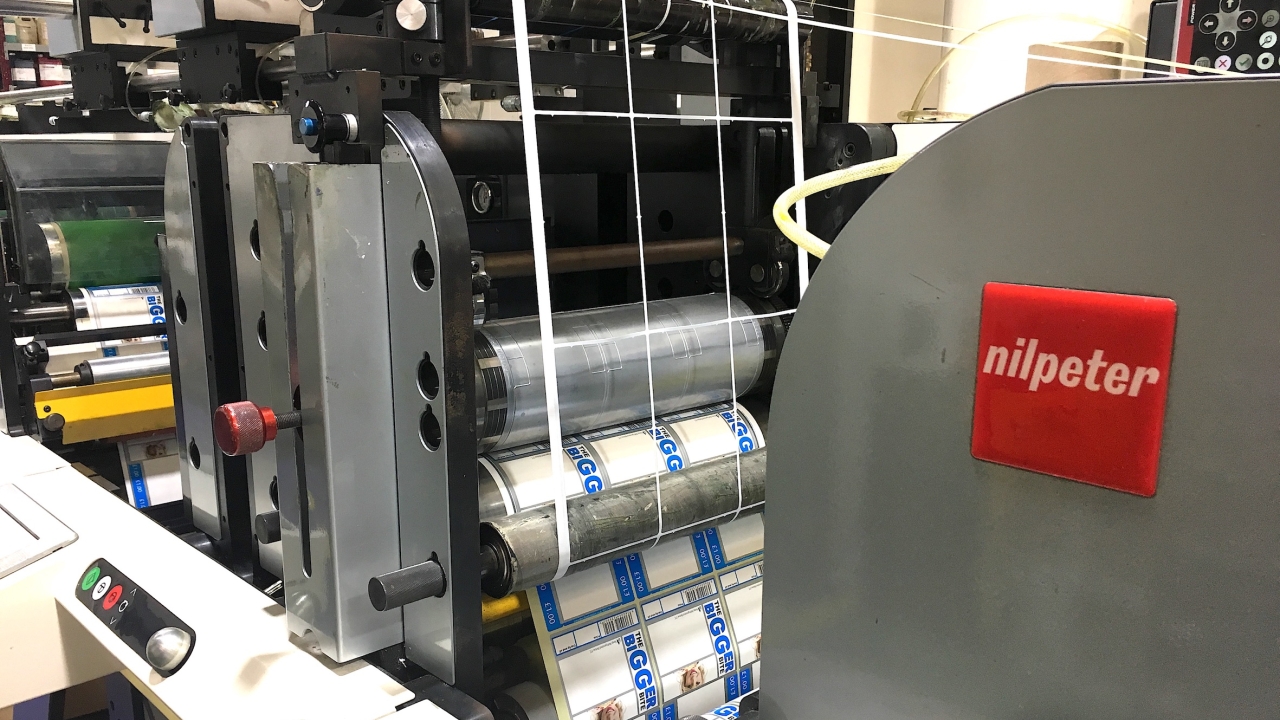
RotoRepel was designed to improve die-cutting efficiency on substrates that use difficult adhesives and hot melt, and, according to RotoMetrics, has none of the chipping or flaking often associated with non-stick coatings, creating an improved workflow with fewer stoppages.
Speaking for Mission Labels, co-founder and technical sales director Dave Humphrey commented: ‘We’re running typically 70,000 to 100,000sqm jobs at around 120m/min, so need reliable and accurate performance from our dies. RotoRepel has made a huge difference to the performance of our two Nilpeter presses, and for us RotoMetrics products are the benchmark for the industry.’
Set up in 2002 by Dave Humphrey and his wife Fiona, and Martin and Sue Gearing, the company has grown to a £2.5m GBP business that employs 18 and produces a variety of labels for the food, hair and beauty, pharmaceutical and industrial markets. Printing is carried out on two 8-color Nilpeter FB flexo lines with reverse printing, over-lamination and back-cutting capability, with the facility to produce peel and reveal labels. Converting is handled by Omega, Rotoflex and Flexor equipment.
The company uses a range of materials from paper-based to synthetics, all adhering to the strict regulations of BRC, from which it holds the top ‘High Hygiene AA’ rating. Mission Labels uses low migration UV and WB inks throughout, with UV varnishing, with the offer of a white back-up on clear film to produce a UV quality label with WB inks. Fully self-sufficient from pre-press to finishing, the company has a policy of ongoing investment, that includes a full suite of Adobe software, CtP processing of HD-flexo plates, and a state-of-the art color matching system.
Dave Humphrey summed up the value of getting the small details right: ‘We are an efficient outfit here and need all of our technology to perform to the best of its ability. The simple and inexpensive switch to RotoRepel has given us improved performance from our presses, simplified life for our operators, and improved our bottom line.’
Stay up to date
Subscribe to the free Label News newsletter and receive the latest content every week. We'll never share your email address.