HP Indigo moves to enhance printer’s capabilities with new press and ILP unit
HP Indigo has developed 6900, a new digital press which provides enhanced capabilities to label and package printers by extending the application range of pressure-sensitive labels produced using its technology.
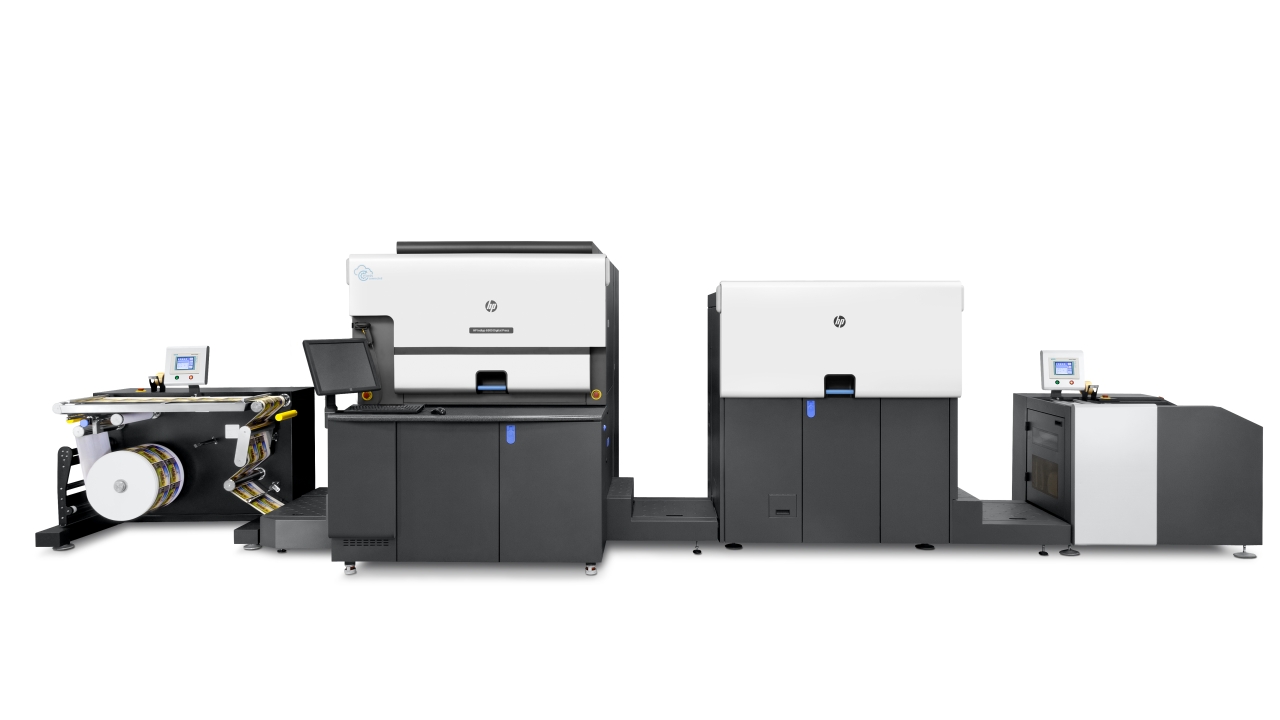
A key element of the new HP Indigo 6900 is integration of Pack Ready for Labels, offering enhanced chemical, mechanical, thermal and water resistance to pressure-sensitive labels. This opens them up to use in applications where high resistance is required, such as specific food, beverage, personal care, household chemical and pharmaceutical environments. Edible and automotive oils, refrigerated and sterilized goods, cleaners and bathroom products are identified by HP Indigo as such applications that are more easily addressed by printers deploying Pack Ready for Labels.
Ami Berger, product marketing manager for the HP Indigo 6x00 series, explained that such applications represent a third of the total pressure-sensitive label market. Two-thirds of the market, where high resistance is not a requirement, can already be readily addressed using HP Indigo digital printing technology.
To achieve such resistance characteristics, HP Indigo has developed a suite of pre- and post-press technologies, starting with an upgraded in-line priming (ILP) unit. The enhanced ILP features a gravure-style, anilox-based coating mechanism that supports the use of a new primer, developed in collaboration with Michelman. This primer, DigiPrime 022, provides enhanced adhesion between the substrate and ink. On top of the new Pack Ready primer, the DigiGuard 222 Pack Ready varnish is applied. Alternatively, HP-approved off-the-shelf varnishes can be augmented with the DigiGuard 901 varnish strengthener additive to provide chemical crosslinking with HP Indigo’s ElectroInk, so delivering the requisite resistance.
Berger noted: ‘While it has been possible to address this market previously, either using additional post-print processes or other printing technologies, Pack Ready for Labels means there’s no need for lamination or to use high-end UV varnishes to achieve high resistance when using the HP Indigo digital printing process.’
The HP Indigo 6900 features the upgraded ILP as an option and it also available as an upgrade option for HP Indigo WS6800 owners. The new ILP supports existing primers used by HP Indigo customers, with the added benefit that switching primers is simplified by the new coating mechanism.
‘Previously, the use of rubber rollers in the coating mechanism required extensive washing if looking to switch between primers, which could cause a headache and long periods of press downtime,’ explained Berger. ‘With the new coating system, it is a chamber doctor blade system that is essentially plug and play, making it much quicker and reasonable to change the primer.’
HP Indigo 6900 also integrates easily with HP Indigo GEM technology. GEM is a UV inkjet-based unit which enables the application of fully digital graphic embellishments in one pass. The technology is capable of a number of embellishments including digital, variable spot and tactile varnishes, foils, cast & cure and a range of other creative effects. It has so far only been shown publicly working in-line with an HP Indigo WS6800 press, but the HP Indigo 6900 will be ready to be integrated with GEM out of the box.
As well as future-proofing due to compatibility with Pack Ready for Labels and GEM, the HP Indigo 6900 features a number of ‘behind the hood’ productivity enhancements that have addressed pain points identified by existing HP Indigo 6x00 series press users. In total, HP Indigo has changed or improved more than 100 parts in the 6900 from previous 6x00 series models. New pumps and a new pipe system offer improved reliability, color calibration has been halved, a 7mm CCC provides better frame utilization, and an enhanced AAA print quality inspection system offers a better detection rate, less false alarms and can be used for a wider range of substrates, according to Berger.
Further developments include a splice detector that will detect splices, disengage the print engine and continue printing after the splice, meaning printers can achieve a higher utilization rate when using lower cost rolls that have splices. This also improves the life of consumables and eliminates the need to manually monitor splices, noted Berger.
A new DFE, HP Production Pro for Indigo Labels & Packaging, offers a faster RIP, allows enhanced fleet optimization and delivers greater site connectivity to respond to the pace of growth HP Indigo said its customers are experiencing. It is intended to cater to the increasingly complex environments printers operate in, where they are running multiple presses across multiple sites, producing an increasing number of complicated jobs, and with a need for more automation and streamlined management tools.
All of the above lead Berger to describe the HP Indigo 6900 as, ‘the most significant labels and packaging new product innovation this year.
‘The HP Indigo 6900 gives you enhanced capability mostly on versatility and productivity, since the print quality is inherent through the print technology. You can address more applications and be more productive, and not just on the press but through the entire ecosystem.’
HP Indigo 6900 is commercially available from this week, when HP is hosting its latest global VIP event. Around 700 attendees are expected in Israel on February 20-21.
Also commercially available from this week is ElectroInk Silver. This new ink is said to open up a range of metallic colors by using it as a base layer, as well as other potential uses, such as replicating foils. To support ElectroInk Silver, HP has developed a special binary ink developer (BID) with a customized design and special materials to cope with issues arising when running the conductive elements found in ElectroInk Silver inside the electric field present in the print engine.
GEM is to be made commercially available later this year. Read more about this technology in L&L issue 6, 2017, and here.
Stay up to date
Subscribe to the free Label News newsletter and receive the latest content every week. We'll never share your email address.