UPM Raflatac launches recycled content PP label material
UPM Raflatac has launched the first polypropylene (PP) label film manufactured from post-consumer recycled (PCR) plastic using Sabic’s TruCircle technology for certified circular PP products.
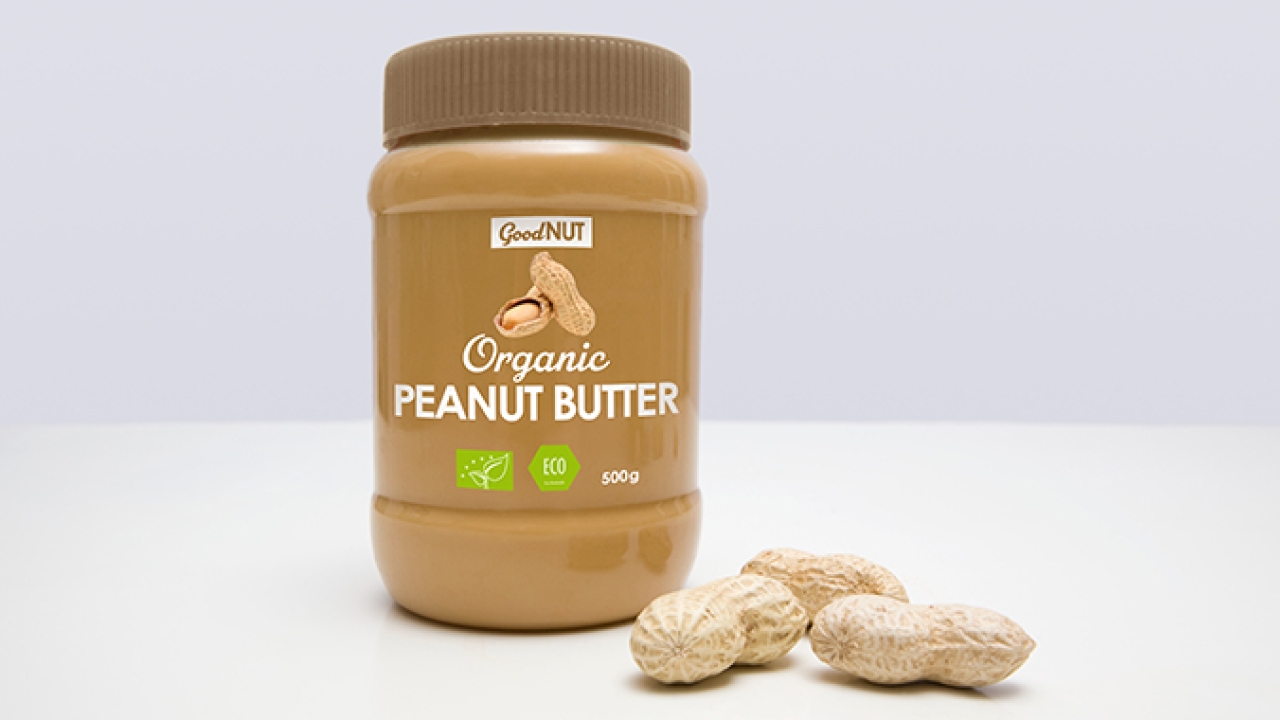
UPM Raflatac’s PP PCR Clear and White products are made with a chemical recycling technology that uses mass-balance approach to deliver virgin-like resin feedstock. With the same properties as standard PP films, these PP PCR films can be used in different label applications, including rigid food packaging. Customers and brand owners can achieve the same product performance and cut their footprint by decreasing the amount of virgin materials used at the same time.
‘We are happy to be involved in our industry’s shift toward more circular solutions and this innovative product is the first of its kind available on the market. It is a concrete outcome of our efforts to label a smarter future beyond fossils by developing products that reduce the use of nonrenewable materials and treat waste as a valuable resource,’ said Antti Jääskeläinen, executive vice president of UPM Raflatac.
New products are a continuation of the company’s mission to use recycled or renewable raw materials initiated with the Forest Film where fossil raw materials are replaced by renewable wood-based ones.
The whole value chain of PP PCR films has ISCC PLUS certification, widely recognized sustainability certification scheme that verifies the mass balance predefined and transparent rules. In addition, it provides traceability along the supply chain, from the feedstock to the final product.
The PP PCR films have been developed leveraging TruCircle, Sabic’s complete portfolio of technologies that span design for recyclability - mechanically recycled products, certified circular products from feedstock recycling of plastic waste streams and certified renewable products from bio-based feedstock.
The high quality of the post-consumer recycled plastic is secured through chemical recycling, turning plastic polymers back into their original molecules. These can be reformed into polypropylene which is equal to one made from virgin raw materials and fulfills strict food safety regulations. The chemical recycling process enables the use of recycled plastics in applications that could not utilize recycled materials before, such as food applications.
‘Sabic is continuing to reinvent and lead in sustainability, and we are truly pioneering the way toward a circular economy for plastics. TruCircle is a significant milestone in our journey and with it, we’re more committed than ever to collaborating to close the loop on used plastics for the good of our planet,’ said Mark Vester, circular economy leader at Sabic.
Stay up to date
Subscribe to the free Label News newsletter and receive the latest content every week. We'll never share your email address.