Variable data verification
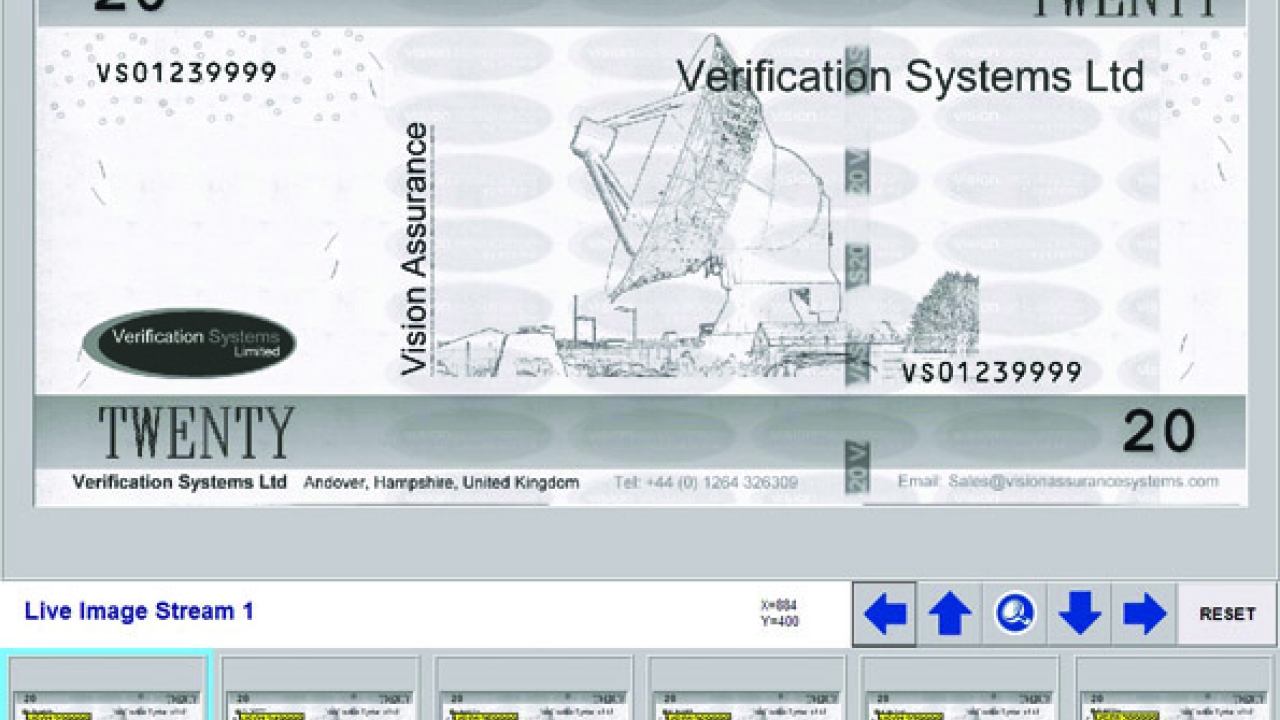
Variable data verification poses critical challenges on high speed labeling lines and can make use of techniques developed for document and banknote inspection. Mark Williamson and Derek Norridge examine the issues
Industrial vision has an important role to play in a host of inspection applications in the paper, printing, label and labeling industries. Applications include continuous verification and/or quality inspection of numbered print and inspection of symbols and labels on web, sheet or single documents, as well as inspection of security features by checking the presence, position and integrity of applied features such as foil and hologram devices and base paper inserts like security threads. One particular application that poses critical technical challenges is that of variable data verification, where data such as serial numbers are different on each item being checked. Variable data verification can provide100 percent checking and verification of sequences and print quality of numbered documents on high speed printing and collating machines.
Variable data verification
High speed image processing techniques and verification are well-established and can be used to check text, 1D barcodes, 2D datamatrix codes individually or in various combinations. In general, the data being checked on any individual batch does not change – each label, or product within the batch contains the same information. However, there are many applications, such as bank notes, cheques, lottery tickets, software security labels, mail out documents and other ‘content critical’ items where the data changes form label to label. Whether this is a sequential or non-sequential change, it represents a significant challenge to the image processing system. As in more traditional applications, variable data verification systems must ensure product integrity and eliminate the production of expensive waste. In order to do that, the system is required to provide 100 percent inspection by reading and verifying label numbering at web speeds in real time and provide a guarantee of print quality by rejecting incorrectly printed characters.
System components
Any industrial vision system consists essentially of the same components: an appropriate light source to illuminate the area of interest, a camera – or cameras – and framegrabber to capture an image, a PC to process data, suitable image processing software and appropriate interfaces into the printing machine for triggering of the imaging system and for a reject mechanism. Capturing images at high speed requires a fast shutter speed to eliminate blurring, this means that there is very little time to sense the light reflected from the document, and ambient light will produce a signal from the camera, which is too small to be of any use. The camera signal can be boosted to a useable level by illuminating the target with a very intense light. To maintain registration and obtain full image access, it is necessary to install the camera and lighting assembly in the delivery section of the press. Ideally the cameras should view the image on a flat surface to minimize distortion. High resolution low distortion lenses are chosen to give the correct working height for the cameras taking into account the area available in the press.
Making measurements
A variety of calculations can be required for variable data verification. These include:
• Serial numbers – non-sequential serial, serial, fixed, blank, denomination or prefix/suffix characters may need to be checked.
• Verification – may be required between serial numbers on the same note, between adjacent notes in each stream and between sequential documents in adjacent streams.
• Sequences – standard increment, decrement, skip etc may be required as well as special sequences
• Layout – checking that the printed characters appear in the correct order and to the predetermined defined layout for each document.
• Sheet Layout – multiple note sheets can be calculated to check for correct rows, columns and special schemes. i.e. split sheets and makeup sequences.
Other requirements may be to check for OCR Quality, OCR / symbol print contrast (for over and under inking trends), alignment and check digit. In practice, the high speed triggered camera(s) capture images and record data from multiple fields for analysis. Ideally, each field can be assigned to search for a different style font, barcode or unique symbol, pattern or logo. Figure 2 shows a screenshot from a system measuring ‘banknotes’ with the live image feed from the cameras. Figure 3 shows a typical report screen for this inspection, in a format representing the layout of the product. The blue text is the calculated number and the green text is the actual number extracted from the images. Figure 4 shows another live feed, but this time, one of the serial numbers is positioned incorrectly, and this is flagged red on the image, even though the number itself is correct. Figure 5 shows a results screen highlighting that the errors have occurred only on Stream 1.
Interfacing and reporting
In order to interface appropriately too many types of presses and transport systems either Web or Sheet fed, provision must be made for all the necessary timing and interface signals between the system and the customer application. Camera trigger signals are normally generated from Document sensors and/or an optical shaft encoder. These signals are used to trigger the camera at the correct place on the web/sheet. The system should also provide output signals for alarms and lamps etc. and interface with customer stop circuits and PLC’s. A signal can be generated for each fault detected which can be used to reject the sheet and mark the defective document. Reports should show the time and date of all sequences inspected and details of all faults detected. By recording the data for each fault, document re-makes can be run at a later time. In the event of a serious printing error, an alarm signal should be generated, typically using an alarm beacon to warn the operator.
About the authors
Mark Williamson works for vertification specialist Stemmer Imaging (m.williamson@stemmer-imaging.co.uk) and Derek Norridge for Vertification Systems Ltd
Pictured: Live feed showing multiple streams – no failures
This article was published in L&L issue 5, 2011
Stay up to date
Subscribe to the free Label News newsletter and receive the latest content every week. We'll never share your email address.