Applicator bottlenecks
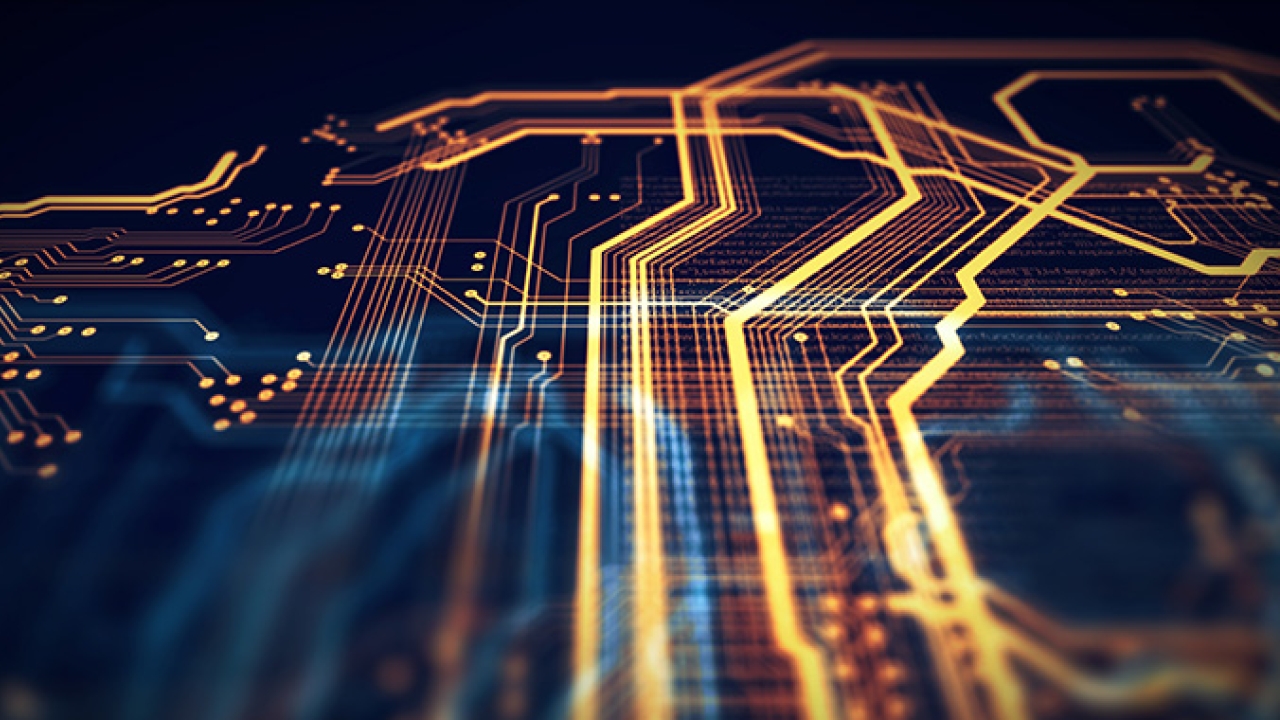
The news in this issue of L&L of a potential breakthrough in clear-on-clear self-adhesive label technology is an exciting one. Signite is a technology developed by Actega which allows the converter to literally print the label substrate as a coating, followed by reverse application of colors and an adhesive layer. These layers are all deposited on a reusable carrier with a release coating on the back to stop the adhesive sticking when the roll is wound up.
Actega points out that Signite eliminates siliconized release liner and filmic face material, with no wastage from die-cutting and matrix removal, since all coating and print layers are deposited only on the image area.
It will be fascinating to see how the beta trials of the new technology roll out. But what is also clear is that Signite will require dedicated application equipment to transfer the adhesive side to the container when the carrier roll is unwound.
And it is the machinery side which has so often held back the deployment of new self-adhesive labeling technologies. The simple fact is that no matter how efficient, or sustainable a new label technology may be, there is an enormous amount of ‘investment inertia’ in the installed label applicator base. This means that the big brands have invested enormous sums of money in installing super-efficient high-speed self-adhesive label application equipment. Krones’ latest modular automatic self-adhesive label applicators, for example, run at up to 72,000 containers an hour.
Label converters have invested proportionately large sums in inspection and inspection-rewind technologies which ensure that every label delivered to the end user is quality checked, sometimes multiple times.
Behind this sit multiple layers of sophisticated technologies such as silicone release coatings which ensure that labels can be released consistently at these sorts of speeds.
The result is a robust decoration system which allows production lines to run at high speeds with practically zero downtime from label failures, with the labeling system usually running in line with further production processes such as filling, capping, sealing and palletization.
So this is the environment into which new PS label technologies are launched. Brands often recognize the advantages of new label technologies, but find it simply too disruptive to change over production line technology.
This largely explains why linerless label technology has failed to establish a really significant foothold in the prime label market.
Imperative
Linerless has a clear market imperative at a time when sustainability has never been so high on brands’ agendas. But linerless labels require a dedicated applicator. Not only does this run up against brands’ reluctance to invest in different applicator technology, but it can also limit brands’ ability to choose between competitive suppliers, since linerless usually forms a ‘closed loop’ system requiring a particular brand of applicator machine.
As an example, Ritrama, now part of the Fedrigoni group, developed the innovative Core linerless system some years ago, which allowed any label converter to print on rolls that were converted to linerless in-house. But it still required brands to invest in a dedicated applicator machine manufactured by Ilti, and this has limited the technology’s market penetration.
Avery Dennison is an example of a company which recognized the key importance of applicator technology when trying to push the boundaries of self-adhesive label technology. L&L readers might remember the Curve Appeal system which allowed the application of large format self-adhesive labels onto curved container surfaces, offering up to 30 percent more billboard space than standard PS body and neck labels. This required not just new materials development, but also a specialist applicator, which was manufactured under license from Harland Machine Systems based on the company’s Titan applicator. A line was installed at Silgan Plastics in Indiana, USA, but once again the entire system – capable of challenging shrink sleeves in terms of front of container branding space – did not achieve its full market potential.
What this brief review makes clear is that for new self-adhesive label technologies to succeed, end users must also be prepared to invest in the relevant applicator technology – which is generally considered disruptive to their existing automatic self-adhesive labeling workflow.
Maybe the missing link here is the contract packer. In the same way Avery Dennison was proactive in setting up a whole Curve Appeal decoration line at Silgan Plastics, would a certain size of contract packer be interested in forming a partnership to install an innovative self-adhesive applicator/material system which would offer key benefits to their target end user base?
Perhaps inviting the contract packer industry to the next Labelexpo might be a way to find out?
Stay up to date
Subscribe to the free Label News newsletter and receive the latest content every week. We'll never share your email address.