Automating flexo pre-press processes
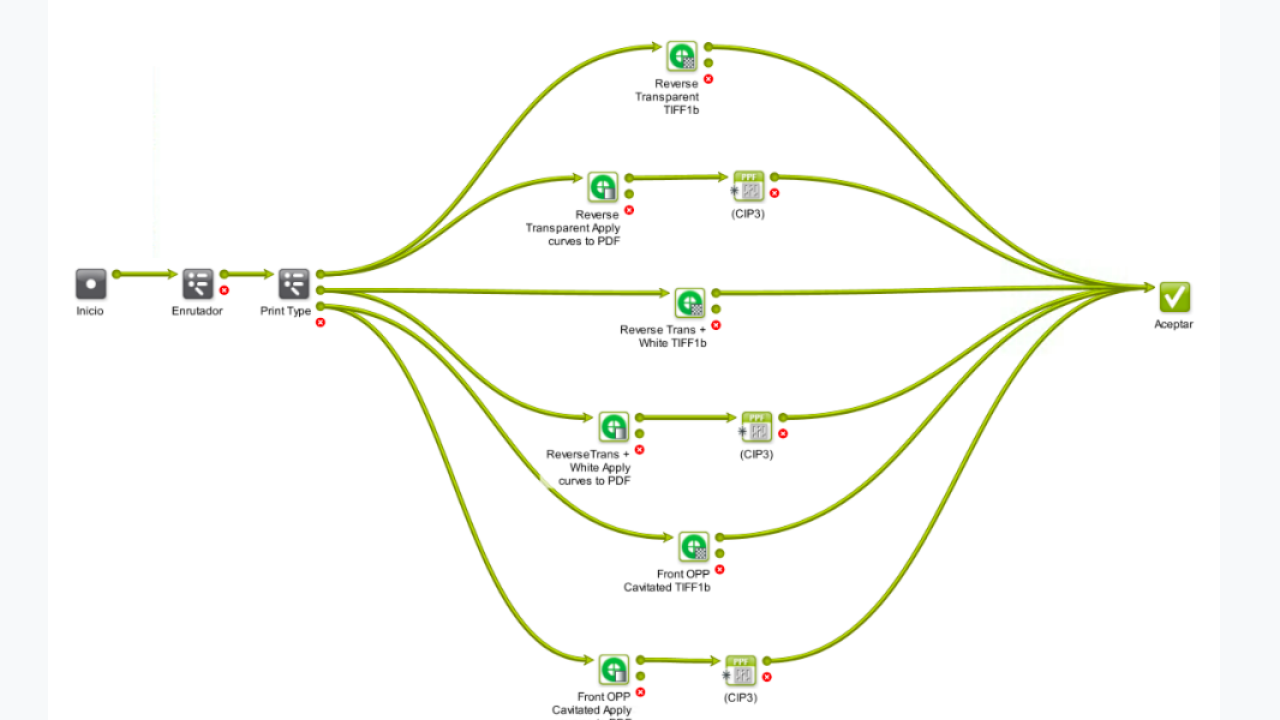
In the last ten years great advances have been made in the quality of flexographic printing of flexible packaging and labels more due to pre-press developments than the design of better flexo presses.
Specifically, variations of the ‘flat dot’ have revolutionized flexo printing and allowed flexo to challenge competitive printing systems in sectors where it previously struggled.
Flat dots have allowed a high level of standardization in the flexo printing process. Standardization is the key tool for limiting process variables and extends all the way back to pre-press – although each job still requires its own unique analysis and feedback from print back to pre-press.
The final goal of standardization of press variables is automation. Automated systems eliminate errors and allow time to be better spent on other tasks. A successful automated workflow will include the following elements:
1. Pre-press tasks performed in accordance with the job design or final product
2. Standardization of the internal review system for individual tasks and workflows
3. Definition of workflow systems to be used as standards
4. Programming of the selected workflows
Pre-press tasks
The principal task of pre-press operators is to carry out actions on the original artwork until it is considered ready to be printed. These operational tasks are defined by the requirements of each piece of artwork: the end use of the final product; and the characteristics of the press on which it will be printed. Pre-press operators can optimize these common tasks by using workflow systems.
The range of pre-press operations is varied, but it is important to highlight those which are most common:
• Trapping
• Distortion
• Application of curves and predefined layouts
• Modification of screening angles
• Regulation of printable minimum dots
The list could be wider and more varied, but the goal is to define which tasks and operational actions we frequently perform in the treatment of the designs and the routine steps we follow.
Standardization
To ask which workflow system we should implement, we need to summarize and put each workflow step in order: in other words, we need to standardize them. The standardization exercise requires us to check and review the processes and performance of the pre-press team and analyze repetitive work actions.
In operations with more than one pre-press technician, the kind of information which supports standardization will make the team more cohesive and less dependent on individual abilities. Collecting and listing all actions that are individually or collectively performed on an artwork – as well as coordinating part of those actions with the printing team – will help in establishing working methods that minimize errors and optimize the printing process.
Definition of workflow systems Primary workflow systems should be simple steps and easy to follow. It may be necessary to divide certain complex workflows into simpler steps.
To program a workflow requires a certain level of skill in software programming. Regardless of the software acquired for workflow creation, it is very important to carry out thorough training for the programmer, which ultimately will save time and cost. If these programming skills are difficult to achieve internally, we suggest contracting an external company to execute workflow creation and training of staff in their functional use.
To summarize, we strongly recommend taking advantage of the current range of digital pre-press tools that help us optimize resources in our pre-press department, ultimately avoiding mistakes during printing.
Stay up to date
Subscribe to the free Label News newsletter and receive the latest content every week. We'll never share your email address.