Digital flexpack makes waves
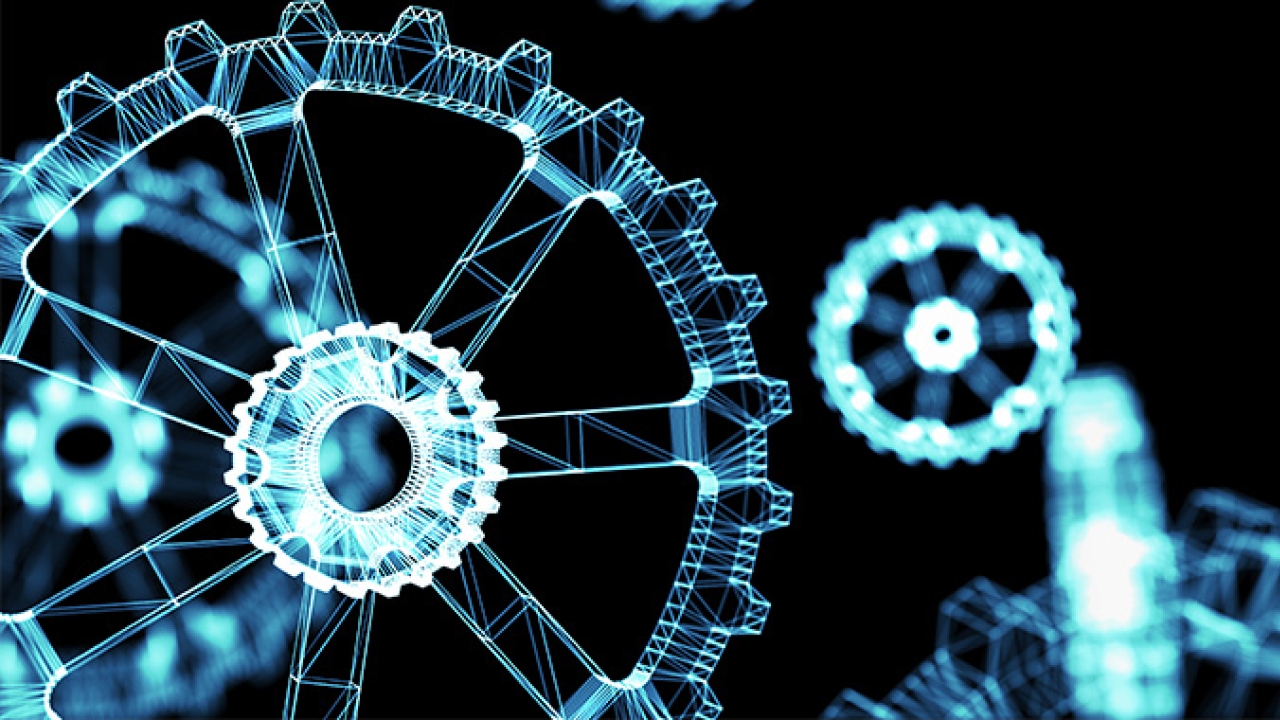
Less than a decade ago flexible packaging was all about wide web, long run, cost-efficient commodity production. Presses were highly specialized monsters, based either around Central Impression drum (CI) flexo, or unit-type gravure presses. Use of water-based and solvent inks for flexo and solvent inks for gravure required powerful drying tunnels to dry the inks at high speeds, giving the presses a distinctively large footprint.
Although increasingly designed with robotic changeover for fast change between jobs, these presses were not designed for short run work. The cost of CI flexo plates and gravure cylinder engraving alone, let alone the makeready waste at these widths and press speeds, made short runs impractical.
But at the same time, marketeers were learning the power of short run labels produced both on digital presses and on highly automated, fast change narrow web UV flexo presses. Clearly there was potential for the same kinds of agile marketing for flexible packaging.
Then came a new generation of digital and UV flexo presses with wider web widths in the 26-32in (670-830mm) range, built to handle thinner, unsupported, heat-sensitive webs. UV flexo press manufacturers such as Bobst and Omet produced in-line presses in these mid-web widths, followed by MPS and Nilpeter, while Mark Andy rediscovered its Comco heritage in developing the P9E platform and demonstrating a 26in module at Labelexpo.
Benefits
There are many benefits of mid-web UV flexo compared to both CI flexo and gravure platforms for short run flexible packaging. Elimination of solvents is a key one, while UV (and UV LED) curing eliminates the need for energy-intensive drying tunnels. Plate costs are reduced and the presses highly automated to reduce changeover times and makeready waste.
These presses allowed narrow web converters to diversify from PS labels into a whole new realm of value-added flexible packaging opportunities.
On the digital front, HP led the way, back in 2014, with its ground-breaking 30in HP Indigo 20000 press. For many years, as the industry waited for the commercial availability of Landa Nanographic press technology, HP Indigo had the digital flexible packaging field pretty much to itself, racking up over 200 installations globally and sparking a new, disruptive model of digital-only flexible packaging converters like ePac, which now has now purchased more than 50 HP 20000 presses across 20 locations.
Now we see a new generation of aqueous (water-based) inkjet presses being brought to market specifically tailored for flexible packaging production. Water-based inks are considered safe for food packaging – though the finished packs still need to be migration tested – but do require a pre-coating for use on films.
At the last Labelexpo Europe, Memjet made clear its ambition to become a major player in the digital flexible packaging market after launching its Duralink pigment-based inkjet head technology. At the show, longstanding Memjet integration partner Colordyne announced a strategic alliance with MPS to bring the technology to the mid-web market, integrating the Colordyne Duralink printhead technology into its EXL-Packaging press.
And in June this year, Miyakoshi launched its MJP30AXF water-based inkjet press targeted directly at the flexible packaging market. The press is 30in (750mm) wide and runs at 50m/min with a print resolution of 1,200 x 1,200 DPI (in four colors plus white), handling materials down to 12 micron.
Screen meanwhile announced a commercial release date of March 2021 for its new PacJet FL830 water-based inkjet system specifically designed for the flexible packaging market. The press will be able to handle films up to 830mm (32in) wide at speeds of up to 75m/min (246ft/min) at a resolution of 1,200 DPI. At present, the press handles both PET and OPP and Screen is working to further expand substrate compatibility.
Outside the mid-web category, but certainly worth mentioning, is the Sapphire EVO W water-based flexible packaging press developed in a partnership between Kodak and Uteco. It uses Kodak’s 600 x 600 DPI Ultrastream inkjet heads and QD Packaging Inks, which are certified for indirect food contact. The Sapphire EVO prints on a 49.2in (124cm) web at speeds of up to 500ft/min and is available with in-line priming, flexo white and post-coating and a hot air/IR drying system.
Although not digital, a novel approach comes from Comexi, which has developed an offset Central Impression press, which matches relatively cheap plates, offset quality and standardization with the ability to gang then slit multiple jobs across the web.
Stay up to date
Subscribe to the free Label News newsletter and receive the latest content every week. We'll never share your email address.