India: growth in a challenging climate
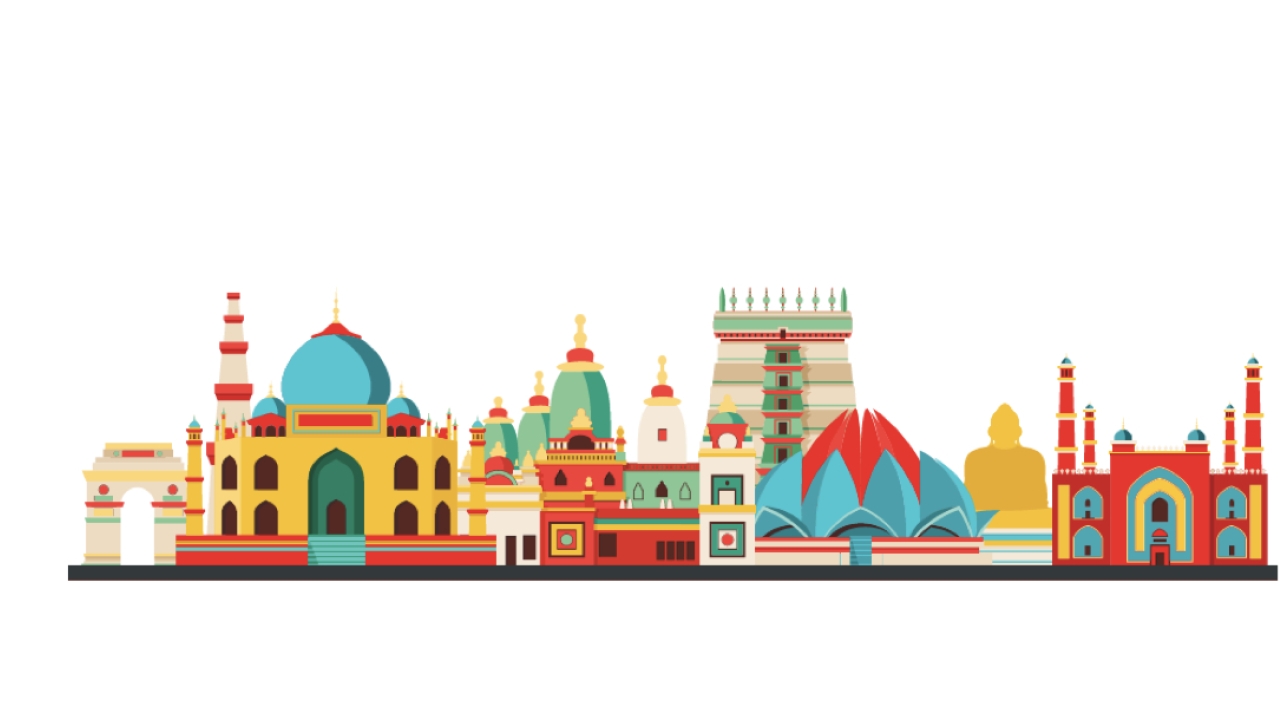
Sharing his insights on industry’s performance in 2019, Harveer Sahni, chairman of Weldon Celloplast, says: ‘The first three quarters saw an increased number of reports on installations because of healthier toplines of smaller businesses that made them opt for high-end label presses. By September there were reports of a slowdown that was more pronounced in the automotive sector and gradually spreading to other sectors. However, given the size of India’s population and increase in demand, the growth of labels is steady and will continue being so.’
Ajay Mehta, managing director of SMI Coated Products, says: ‘Overall, there is a dampening spirit in the worldwide economy but it has not deterred the growth outlook of the industry. However, as the industry matures in India, economies of scale will bolster more efficiency into the system. Newer innovative label solutions will boost the industry.’
While flexo largely remains the technology of preference, an increasing number of converters are also investing in digital technology. ‘This is a welcome sight,’ comments Mehta. ‘It reflects the willingness of printers to come up with innovative products to cater to the needs of their clients. Digital presses should be acquired to create new applications and not just to use it for short runs. This will create new opportunities and wealth.’
Indian companies have been discussing ways to improve efficiency with current infrastructure while also investing in latest equipment. Mehta continues: ‘Indian printers are now consuming an average of 125,000sqm of labelstock per machine per month compared to 100,000sqm about two to three years ago. An increasing number of automated inspection systems being installed in India reflects the keenness towards automation. The majority of printers today have started a quality control department and ERP implementation is happening across the country.’
Improving efficiency in production has been discussed at various forums. The LMAI conference in 2019 saw several speakers including Carl Brock, global application specialist for Bellisima discussing digitally modulated screens (DMS) that offers stable flexo dots while delivering ink saving, consistent print quality and reduced waste. Hannes Rogler and Martin Hoppel of Rogler International discussed optimization tools and software that can handle up to 15,000 different jobs a day, thereby streamlining the flow of information through different processes.
‘Most leading printers across the country are implementing better production techniques to achieve efficiency and MIS systems to enhance their savings from reduced down times and wastages,’ agrees Sahni.
Sustainability
Sustainability and waste management is fast becoming an imperative, with the country facing a serious pollution problem. Citing an example, Sahni says: ‘One printer was regularly burning label waste in a vacant plot next door. The pollution control department took pictures and sent the company a notice with penalties. Gone are the times when investment in waste management equipment was not even considered. Many companies have started to implement green factory initiatives and it is good to see the responsible trends in the industry.
‘When the Prime Minister starts talking regularly about recyclable, biodegradable solutions, and banning single use plastics, sustainability becomes a major buzz word,’ says Ajay Mehta. ‘The government has brought about a lot of awareness. Brand owners, printers and consumers are equally interested in sustainable packaged goods.’ SMI Coated Products has been switching its clients from 85 micron PE to 50 micron PP. ‘We studied this application on shampoo bottles and brand owners conducted trials successfully,’ says Mehta. ‘As a result, around one million sqm of PP labelstock will now be consumed by this brand instead of PE, thus saving 42 tons of plastic annually. Similar applications have been developed using lower gsm chromo papers. Printers are also successfully using 65gsm thermal paper instead of 74gsm.
‘However, to bring about this change in our industry at a large level, everyone has to join hands across the spectrum. We must leave our competition and provide sustainable solutions for the well-being of our future generations.’
Stay up to date
Subscribe to the free Label News newsletter and receive the latest content every week. We'll never share your email address.