Innovation powers growth
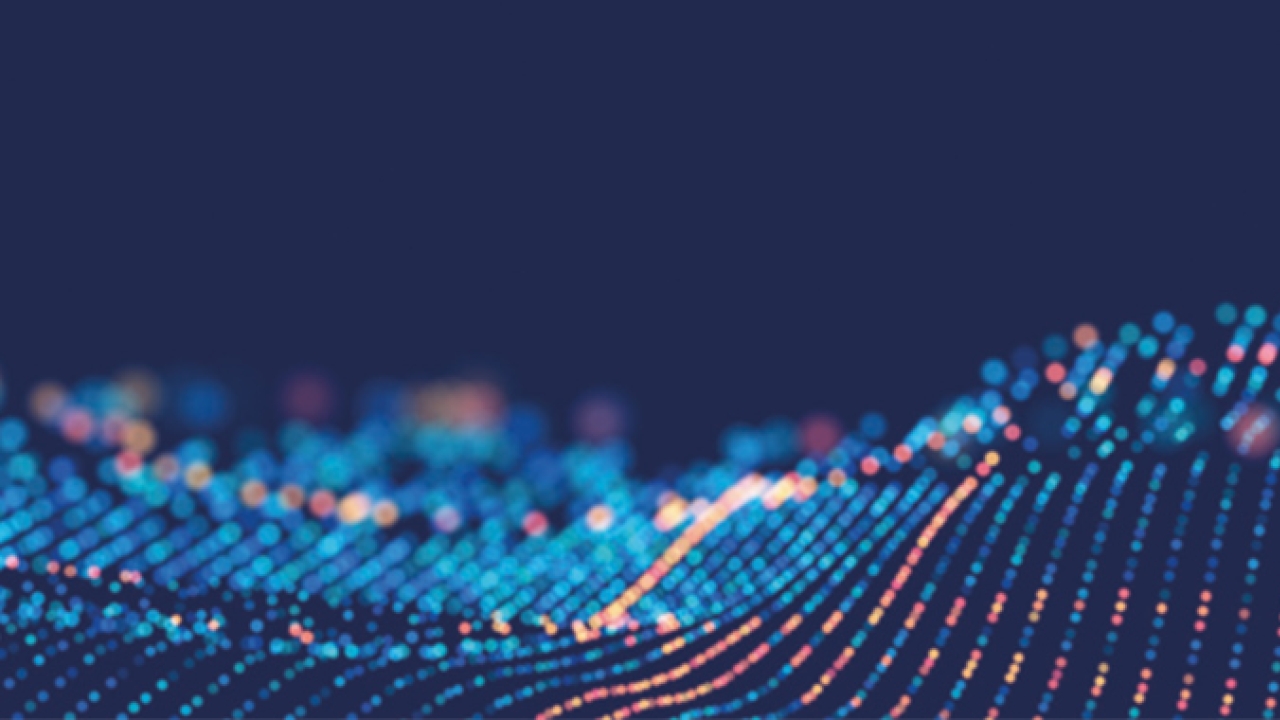
I spoke recently with a major finance group looking to invest in the label industry. One of their main questions was how it was possible for the label industry to have kept growing globally while growth and profitability in the wider commercial print industry faltered.
My answer was two words: innovation and entrepreneurship.
Looking at the fascinating ‘L&L looks back’ column in each edition of this magazine reminds us that innovation goes right back to the start of the narrow web industry, constantly creating new opportunities for label converters to add value and upsell their services.
Innovation has revolved around the modular nature of the narrow web press line, which has also stimulated development of new materials, inks, plates and so on. In the 1970s and 1980s letterpress was the dominant print technology in Europe at a time when it had been overtaken by offset in the commercial print industry (apart from some small niches in book printing). Letterpress cured with UV allowed narrow web converters to offer their brand owner customers extremely high-quality print.
At the same time, narrow web press manufacturers developed modules which allowed further decoration processes to be added in the same press line, including screen printing for heavy laydown opaque whites and 3D effect varnishes, and hot foil/embossing. Flexography was a fast-developing process at this time, and narrow web manufacturers took the opportunity to add flexo coating units for varnishes and coatings.
It was developments in flexography which were to provide European label converters with their next opportunity. While in the US water-based flexography was the dominant technology throughout the 1980s, the early 1990s saw the development of UV-cured flexography. The greater simplicity of the flexographic process soon made UV flexo the upcoming technology of choice for label converters, particularly with the development of digital platemaking. Once again the same level of integration of add-on modules allowed them to offer hot foil/embossing and UV screen in the same press pass.
At the same time cold foil was developed as yet another drop-in modular process unit. Cold foil allowed foiling effects to be added to heat-sensitive materials such as direct thermal labels. Its low origination and operation costs compared to hot foil allowed foiling effects to be added to a huge range of labels for which hot foil was too expensive, particularly in the food and drinks sectors.
Two other key commercial print processes, offset and gravure, were also adapted for narrow web converters, opening up different paths to added value. UV offset formed the basis of narrow web presses targeted at the high-quality toiletries and cosmetics sector – again combined with processes such as screen, flexo coating and hot foil/embossing. Gravure made an appearance as another optional add-on module, specialized in adding first-down white, metallics and cold seal coatings.
Added value
Over the last decade we have seen digital printing opening up a new range of value-added opportunities, not only as a standalone process, but also as another module which can be offered on an in-line narrow web press.
If we look at the different ways digital has been integrated into conventional print platforms, we see the same kinds of innovation taking place. So, for example, we have seen a digital print bar (a mono inkjet unit the width of the press) jetting a first-down white as a replacement for a UV screen or UV flexo unit, which in turn is made possible by the development of more opaque inkjet whites – a real achievement given the viscosity limitations of inkjet. Printbars can also be used to add a variable black (effectively a digital black plate) or a spot color.
We have also seen multi-color digital print units added to flexographic presses. On these hybrid presses, digital has replaced flexography as the main print engine while making use of traditional in-line converting, finishing and coating units.
Today’s big development is digital embellishment, where digital imaging is being applied to spot matte/gloss varnishing, foiling, screen-type 3D and tactile effects and simulated embossing/debossing. These technologies are available in different combinations of off-line and in-line, and once again will open up new opportunities for label converters to add value to the services they offer.
Which brings me back to my conversation with the finance group. As I explained: the label industry has grown consistently – at least two percentage points above GDP everywhere in the world – because technology companies are constantly developing innovations which allow the print industry’s most dynamic and entrepreneurial business owners to offer new and added value services to their customers. It really is as simple as that.
Stay up to date
Subscribe to the free Label News newsletter and receive the latest content every week. We'll never share your email address.