Label Industry 4.0 – myth or reality?
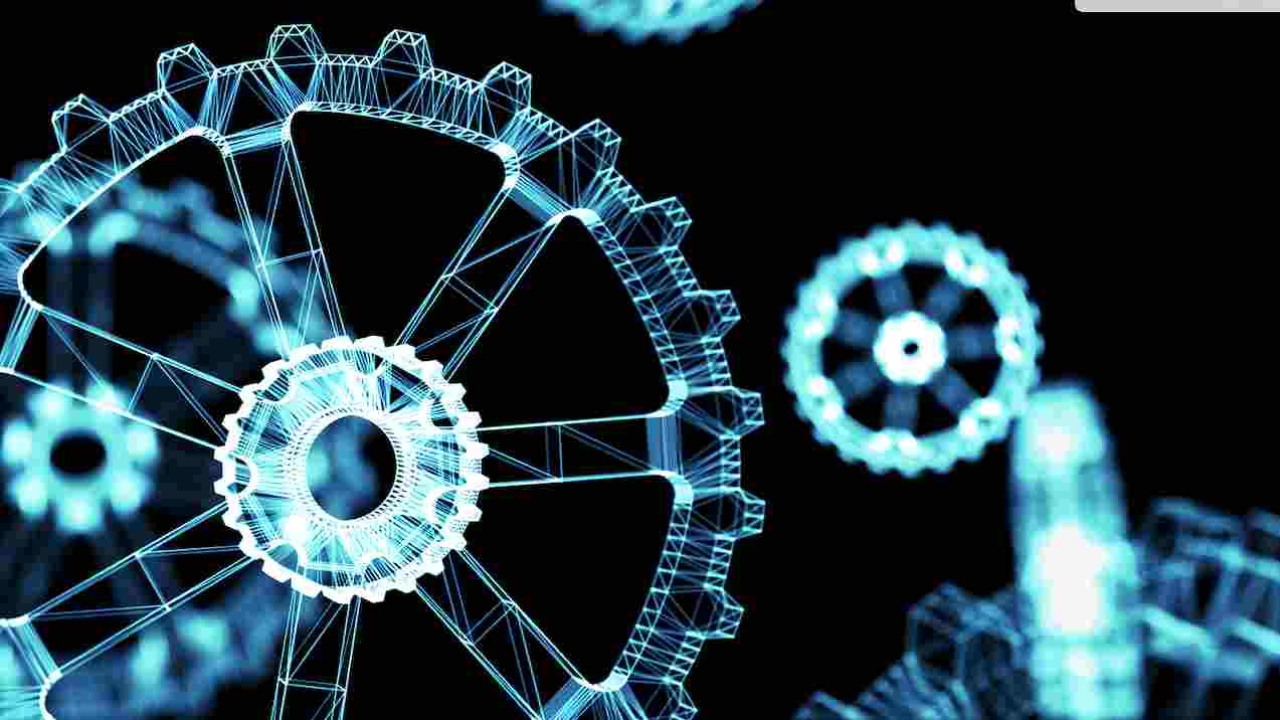
I was recently asked to develop feature ideas for the Gulf Print & Pack show focusing on ‘Industry 4.0’ automation. It soon became clear that this much-discussed term provokes a wide range of interpretations. So what should we understand by ‘Industry 4.0’, and what are the implications for the label printing industry?
A good place to start is Wikepedia’s definition: ‘Industry 4.0 factories have machines which are augmented with wireless connectivity and sensors, connected to a system that can visualize the entire production line and make decisions on its own.’ The ultimate expression of an Industry 4.0 manufacturing operation is the unmanned ‘lights out’ or ‘dark factory’.
We already see Artificial Intelligence (AI) systems – more properly called machine learning – mimicking human decision making across a range of white-collar occupations from insurance underwriting to online customer service and interpreting medical x-rays.
Given access to a defined data set (available resources in a label plant), clearly stated goals (the most profitable manufacturing route) and a set of logical rules, a machine system can, in principle, learn how to make highly complex decisions – and learn from its mistakes.
The victory of Google’s AlphaGo computer program over the world’s best Go player demonstrated this ‘feedback learning loop’ in action. AlphaGo did not win by sheer computing power, as unlike in chess, it is impossible to compute every possible Go variation. Rather AlphaGo learned to play starting from first principles, constantly playing itself to learn what strategies worked and which did not, then applying that learning system to a game with a human opponent – literally out-thinking him in real time.
An Industry 4.0 system is built around intelligent nodes on a network, be that a pre-press workstation, a flexo press or warehouse storage location. Self-monitoring sensors on each node feed status information back to a central processing hub and the node can also receive information which triggers some action (for example setting up a press camera, or making a plate).
The central processing hub runs a constantly updated virtual model of the system as a whole – ‘cyber-physical systems monitoring physical processes, creating a virtual copy of the physical world and making decentralized decisions.’
Automation has been a key industry theme over the last five years, but automation systems tend to exist in their own ‘islands’. Industry 4.0 puts these islands together on the same intelligent network and then starts making decisions according to the goals it has been set.
A goal might include ‘only allow jobs to start which meet a certain level of profitability.’ The system, through its sensor network, is already monitoring costs, drilling down far deeper than a human has time for. It is monitoring press energy costs and per hour rates; assessing makeready costs depending on colors and additional processing; querying warehouse nodes for information on stock availability; monitoring platemaking costs and lead-times and die availability; deciding what inks will need to be mixed, or are already available pre-mixed looking at availability of print, finishing and shipping resources.
AI turns to job scheduling. Can this job be run in slots where similar materials or press configurations are already planned? Does this affect the costing and therefore overall profitability? Finally it defines the machine resources and starts to upload all necessary processing information to each piece of production equipment.
Ground-breaking
As remarked above, much of this individual functionality is already available. One major stumbling block has been that narrow web press manufacturers have ‘closed’, or proprietary, press control systems which require data to be entered by the operator rather than uploaded from a central hub. Performance data such as press downtime is generally entered by scanning barcodes on a standalone console rather than by direct machine integration.
This looks set to change, however. In this edition of L&L my colleague Piotr Wnuk reports on a ground-breaking demonstration of integration between MPS’ Talk to Me open press interface with a Cerm MIS.
Finishing machine manufacturers are already making their control systems open to MIS – for example automated setting of slitting knives from pre-press metadata. Flexo presses are incorporating more self-monitoring sensors, and press cameras are being linked across cyberspace to learn via Big Data analysis about print defects and what causes them.
Back in 1993 when I was editing British Printer magazine, I heard a joke at a Heidelberg CIP3 demo, one of the earliest and most successful attempts at automation. ‘The print factory of the future will be manned by an operator and a dog. The operator is there to feed the dog, and the dog is there to make sure the operator doesn’t touch anything.’ With Industry 4.0, that idea no longer seems so fanciful.
Stay up to date
Subscribe to the free Label News newsletter and receive the latest content every week. We'll never share your email address.