Q&A: Shi Jianping, PTAC
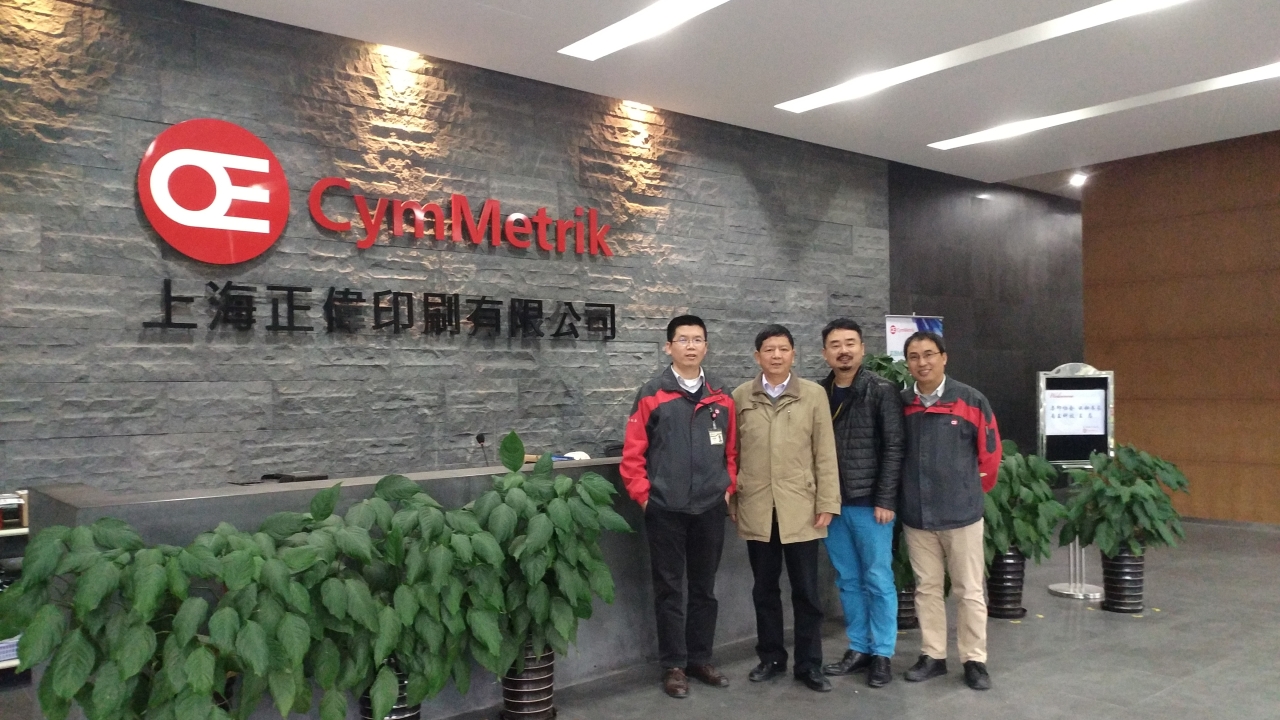
L&L: What are the major responsibilities of the Flexo Printing Branch of the Printing Technology Association of China? And what is its role in China’s industrial development?
Shi Jianping: The Flexo Printing Branch of the Printing Technology Association of China has been a champion of the flexo printing industry’s growth in the past 25 years. There are two main functions. Firstly, to build bridges between print enterprises and government authorities, forwarding their demands and requirements to government in a timely manner and providing in return the government’s policies and regulations to the industry. We make full use of the association’s resources to build a platform of expertise and share these resources with our members. As a representative of the package print community we provide technical support and assistance as well as participating in the drafting of new laws and regulations relating to the print sector. This allows industrial standards to be developed with the requirements of the flexo industry in mind, which maintains a sound basis for development.
L&L: What has the Flexo Printing Branch done to push the growth and development of the industry?
SJ: At the end of September we had almost 270 members, with 25 new members joining this year – an increase of 10.2 percent. We have built a database of 50 experts with detailed technical knowledge of the industry and in the past year we hosted visits from more than 20 giants in our sector, including Avery Dennison, Kodak and Weifang Donghang. In addition, we interviewed more than 30 companies including DIC Graphic, Hangzhou Cron and Shanghai CymMetrik.
A major part of our work was to participate in the establishment of a series of flexo printing industry standards. These included national standards for ‘Color and transparency of printing ink sets for 4-color flexo printing’; ‘Green’ printing standards; process control requirements and test methods for flexo printing of books and periodicals; and standards for Digital Flexo CTP platemaking and flexographic platemaking. We not only contributed to the standards regulating the sector’s industrial development, but we also provided an important data resource and organized skills training for the whole industry.
In addition, after a resolution at our annual meeting last year, we represented our members in an exchange of views and opinions with the leaders of the Environment Development Center about a reduction in the atmospheric pollution tax for water-based flexo inks with VOC emissions of under 5 percent. At the beginning of October, this appeal was converted into a new standard announced on the official website of the Ministry of Environmental Protection. The relative cost reduction of flexo water-based ink in terms of environment protection will raise its market competitiveness to a significant extent.
L&L: What is the current status of the Chinese flexo printing industry?
SJ: According to the latest statistics from PEIAC (Printing and Printing Equipment Industries Association of China), flexo presses were the only type of equipment to show growth of both imports and exports, with growth rates in both cases above 30 percent. At the same time, figures from a national index of leading ink suppliers show that flexo printing accounts for 15-18 percent of overall printing market share – a 10.9 percent increase on the previous year.
Besides the continuous efforts of flexo printing enterprises, the industry has, as we have seen, benefited from the opportunities brought by national environment protection policies. Compared with ‘traditional’ printing methods (gravure, offset and screen printing), the waste gas and liquids discharged by the ink and production process during flexo printing are much less and are more easily controlled at source.
Mr Cai Chengji, a consultant at the Flexo Printing Branch, made a calculation of the density and rate of exhaust emission when printing with water-based ink. As a result of this work, the emission limits for water-based inks to comply with the requirements of eco-label products issued by Ministry of Environmental Protection, is lower than Beijing Municipality’s specified limit of 30mg/m3, and the maximum emission rate is lower than Shanghai and Tianjin’s specified limit of 1.5kg/h.
Therefore, environmental policies are actually a big help for the growth of flexo printing.
L&L: How would you compare the development of flexo printing in China with western countries?
SJ: Industry insiders usually describe flexo in China as ‘late start, poor base, weak foundation, slow growth’. Indeed, flexo printing technology was not imported into China until the 1990s, and it grew slowly due to the limits of the technology and lack of skills.
However, we have seen some real breakthroughs in recent years. The Chinese flexo press industry has moved from nothing, through imports, digesting of knowledge, then innovation and development to achieve its present-day status. The latest statistics indicate that the total installed base of flexo presses in China is currently up to 2,197 pieces – 76 percent of which are made in China.
Letterpress and offset printing were in the past the main production methods used in label printing. But at Labelexpo Asia 2017, exhibitors such as Weigang, Dowell, Bengraphic, Jingda, Hexiang, Olger and Shanghai Xinhu will all showcase new flexo label equipment.
In the fields of flexible packaging and film label printing, the rapid increase in print quality of satellite flexo presses can now compare with gravure presses in terms of production efficiency and precision. However, compared with western countries, Chinese flexo printing is still not mature. At present, flexo printing in western countries accounts for around 32 percent of print production, while in Asia Pacific as a whole, it is only 15-20 percent. The proportion in South America is higher than Asia-Pacific and Africa is the lowest. But the trend is clear: the market share of flexo printing in China five years ago was only 8 percent, and it is up to approximately 15 percent today.
L&L: What are the current challenges faced by China’s flexo industry? And how do we respond?
SJ: In my opinion, the challenges are mainly from two aspects, one for hardware and another for software.
‘Hardware’ mainly refers to the flexo printing plate. In China, the biggest restriction on the rapid development of flexo printing is the high cost of flexo printing plates. Flexo plate material requires complicated production procedures and high precision, and the overall market consumption is not large. This means flexo plates are not as popular as offset plates. For quite a long period in the past, converters had to rely on imported flexo printing plates from companies such as DuPont, Flint, MacDermid, Toyobo, Asahi Kasei and Kodak. Nowadays, Chinese enterprises such as Lucky Huaguang Graphic have started batch production of flexo printing plates, and the output of Chinese-manufactured flexo printing plates is gradually rising.
From beginning of this century, western countries had already entered into the digital platemaking stage, while we are still in the process of converting from conventional to digital plates.
Currently the integration level of digital plate technology in Chinese platemaking companies is not high. So Chinese flexo printing enterprises need to strengthen communications with advanced international enterprises – ‘go outside and invite in’ – in order to diminish the gap while achieving the breakthrough and upgrading of our own platemaking technology.
The ‘Software’ mainly refers to the establishment of industrial standards and cultivation of professional talent.
Industrial norms and standards are required to regulate the processes adopted of Chinese flexo printing enterprises. Next year, we will continue to establish these industrial standards in the form of several new regulations. These will include process control and test methods for UV-cured flexo printing, and a draft of new technical requirements and assessment methods for ‘Green’ flexographic printing. And besides organizing technical exchanges, summits and forum activities, the Branch will also encourage flexo enterprises to cultivate training of their own workers through daily production and training classes, and to innovate continuously in order to improve the flexo products’ quality to match the level of offset and gravure printing. As the saying goes: ‘More preparation quickens the speed in doing work’. Raising the technical level of personnel and their ability to innovate will allow enterprises to cope with any kind of challenge and realize more rapid development.
L&L: What are the most important measures the Flexo Printing Branch will take in the future?
SJ: In 2018, we will emphasize the following, as well as keeping up our other established work. Firstly, implement environment protection policies. At present, 21 municipalities and provinces have published (different) regulations relating to emission standards of air pollutants for the printing industry. In 2018, China will start levying its environment protection tax. The Flexo Branch will forward in a timely manner the latest environment protection policies from the government and feed back the status of enterprises to the relevant governmental department.
Perhaps the most important national environment protection standard will be ‘Technical requirements for environmental labeling of products – gravure and flexo printing ink’, and the Branch will cooperate closely with the Authentication center of the Ministry of Environmental Protection and will carry out the work of interpretation, propagation and implementation.
The second key strategy is around the application of new media. The development of the internet era and the joining of a younger generation of flexo talents makes communicating by WeChat more and more popular. We are operating three WeChat groups – ‘Flexo printing Vision’, ‘Big Flexo Branch family’ and ‘Vice president of Flexo Branch’. Using these faster and simpler new media communication platforms, we hope to promote an effective and direct communication and learning between the Branch and enterprises as well as among enterprises.
What’s more, in order to promote the quality improvement of flexo products, the Flexo Branch will go on to hold the biennial Hua Guang Cup, rewarding product quality assessment in the flexo printing industry.
L&L: What do you think about the development of digital printing in China? Is there any conflict with flexo printing?
SJ: I think digital printing must be a mainstream printing method in the future. It meets the demands of the market for fast turnaround and personalized packaging. Now, digital printing in China is still at an early stage of exploration, but there is already a small group of enterprises which have obtained good results from digital printing, converters such as Taiwan Fengpeng and Shandong Lv’Ai.
Both digital and flexo printing are environment-friendly methods, which will develop mutually for quite a long time. Following the development of automation and greater efficiency of flexo press technology, the two processes will be combined for use in various ways.
The Opinion was first published in Labels & Labeling, issue 6, 2017
Stay up to date
Subscribe to the free Label News newsletter and receive the latest content every week. We'll never share your email address.