The Mike Fairley column
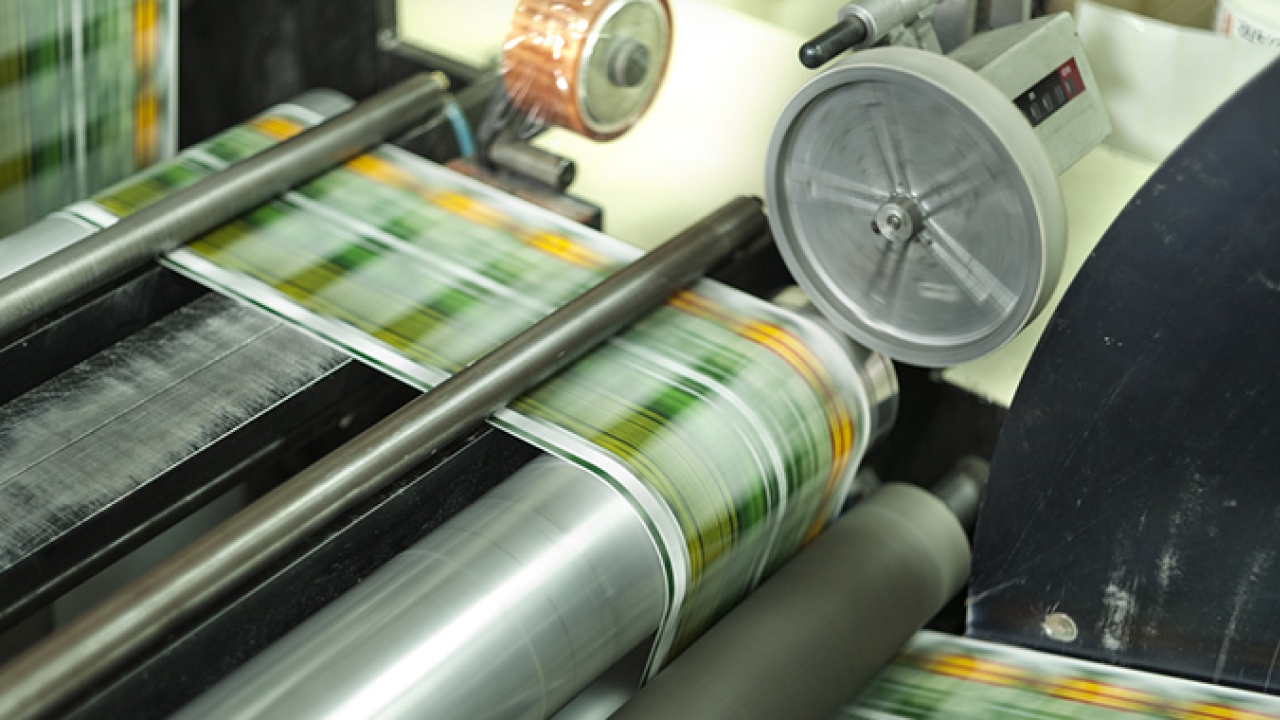
With in excess of 20,000 self-adhesive label presses in use worldwide, together with increasing numbers of flexible packaging and shrink sleeve printing presses, that printing and converting machinery related accidents might be somewhere near the top of the list of reported industrial accidents each year ̶ across all industries and sectors.
Just think of how many printing cylinder nips, unwind and rewind rolls, die-cutting units, specialized finishing systems, tension control systems, turret rewinders, UV-curing units, waste removal and web handling rollers are in operation in the label industry almost every day, and the possibilities there are for accidents to occur during make-ready, attending web breaks, freeing blockages, during machine setting, cleaning or maintenance. And that's just on all those printing presses operating with anything from four to nine print units.
Add in all the related inspection rewind machines, slitters, embossing and punching machinery, foiling machines, coaters, splicers, core cutters, inspection systems, air trim removal, web cleaning and corona treating equipment, and it all adds to the potential for a high number of machinery-related accidents, some possibly quite serious, each year.
Yet this is not the case. Print related industry accidents, including label production (both printing and converting), are far from the top of the total of all global industrial and workplace accidents which, according to the International Labour Office, currently add-up to in excess of 337 million occupational accidents and 160 million victims of work-related illnesses worldwide each year.
Globally, the print-related industries have tended to be statistically grouped under the ‘Other manufacturing’ category of accidents, coming-in behind food and drink manufacturing, chemical and pharmaceutical products, metal fabrication and manufacture of transport products in the number of accidents each year. Outside of manufacturing, the construction industry is one of the leading sectors of workplace accidents.
Even within the print and paper converting sectors globally, machinery accidents are usually only around the third cause of all the accidents and injuries, coming in behind manual handling (around 26 to 27 percent of the industry's accidents), slips, trip and falls at between 19 and 22 percent, while contact with machinery is down at anywhere between 12 percent and 22 percent (depending on country and how statistics are compiled). Most of the printing machinery accidents that do occur could often have been easily prevented through the proper usage and maintenance of guarding, combined with enhanced instruction and training, and eliminating or minimizing potential accident hot-spots in and around the press.
The label industry’s leading manufacturers have done much in recent years to make press operation as safe as possible, automating servo controls, print units and die change, introducing electronic setting of anilox rollers and print pressure, together with the automated loading of previous print settings to minimize press set-up handling.
As a consequence of improved training, advances in press controls and automation, as well as more sophisticated machine guarding, the printing industry's incidence of machinery accidents has tended to experience a decline in most years since the millennium. Indeed, the data that is available indicates that while it’s still quite possible to get hurt (or very occasionally even killed) in a printing plant, print firms offer their workers a safer environment than private-sector industry as a whole.
Entangled
Where label machinery accidents do still occur, it has most commonly been due to contact or getting entangled with dangerous moving parts, including in-running rotating nips, such as between printing cylinders, rollers, gears and transmission machinery. Many of these could possibly be put down to older machinery where levels of automation and guarding are less sophisticated. Long, untied hair, loose work clothing and jewelry all pose obvious entanglement hazards and should always be avoided.
Around three-fifths of the industry's reported machinery accidents have historically occurred during cleaning, making-ready, webbing up or attending to web breaks. A further one in five of the accidents occur while the operator is freeing jams or blockages, and while machine setting. Between them, machinery accidents are most likely to lead to a variety of cuts and bruises, lacerations, fractures, dislocations and crush injuries to fingers or hands.
However, as already mentioned, it is manual handling involving lifting, lowering, carrying, pushing and pulling that comes out as the main cause of accidents in printing and paper converting, not uncommonly occurring in areas such as warehousing, storage, reel handling, moving pallets or ink containers, and where picking and packing are taking place.
Another key area of manual handling accidents in the label world is those that involve the handling, setting-up, cleaning, inspection or storage of cutting, embossing, foiling, sheeting or perforating cylinders, anvils and support rollers. Certainly, solid rotary cutting, embossing or foiling tools can be quite heavy and a challenge to lift in and move in or out of the converting line and handle safely without risk to the operator (or the tool).
Such tooling can be heavier, harder to handle, bulkier and potentially more likely to cause damage than in many other label production applications. Whether flatbed, rotary or flexible cutting dies, they all have sharp edges and can lead to cuts being sustained during handling, set-up and adjustment. Yet the basics of lifting and moving heavy or awkward shapes are not always well explained. A good guide to handling, storage and safety consideration in the handling of tooling can be found in the Label Academy book ‘Die-cutting and Tooling’.
In addition, it should noted that operators may need to adopt somewhat awkward postures when inserting or removing tooling or making on-machine adjustments. If these tasks are not carried out appropriately and safely there is obviously a risk of injury. Such injuries include work-related musculoskeletal disorders creating pain and injuries to arms, legs and joints, as well as causing repetitive strain injuries.
Manual handling injuries can have serious implications for the employer and the person who has been injured. Apart from the more specific areas of warehousing, storage, packing, and the handling of all kinds of tooling, they can occur almost anywhere in the workplace and heavy manual labor, awkward postures, repetitive movements of arms, legs and back or previous/existing injury can increase the risk.
Safety measures
To help prevent manual handling injuries in the label printing workplace, any potentially dangerous tasks should be avoided as far as possible. However, where it is not possible to avoid handling reels, tooling, boxes, pallets and the like, then employers must look at the risks of the specific tasks and put sensible health and safety measures in place to prevent and avoid injury.
Fundamental points to remember in the manual handling and lifting of heavy dies, reels, boxes, or awkward or difficult shapes are as follows:
- Get a good grip with the palm of the hands when lifting and handling, not just fingers only. Use protective gloves where necessary.
- Avoid standing and holding heavy tools or loads. Rest on a bench or platform of a suitable height if any delay is unavoidable.
- Never change the grip while carrying.
- Never persist in attempting to lift loads, reels, boxes, or heavy tools if there is a feeling of strain.
- Train workers to keep lifts below shoulders and above knee height.
- Educate workers about risks to the lower back related to handling and twisting.
- Use handling aids or hoists wherever possible.
After manual handling accidents, the second most common cause of accidents in the world of printing and label converting ̶ and the cause of some 40 percent of all major accidents ̶ is for those that involve slips, trips and falls. Most commonly, these types of accidents are likely to occur in production areas or washrooms, and are followed by accidents outdoors, in stairways or car parks.
In label production areas slips, trips and falls are often related to spillages ̶ of oil, ink, water or other fluids (which should be cleaned-up immediately, dried and signposted) ̶ by pallets or other items extending into walkways, from label substrate and other production waste on the floor and not placed in suitable bins, from trailing cables (provide cable covers for temporary arrangements during maintenance or repairs), or from reel or pallet trolleys or trucks not placed in their designated storage areas. Outdoors, accidents may be due to rain and wet surfaces, ice or snow on the ground, untreated potholes and uneven ground.
Many of these types of these slip, trip and fall accidents in and around the factory can often be put down to poor housekeeping or poor maintenance. Monitoring and routine checks by managers, supervisors and maintenance staff, the investigation of incidents and the monitoring of reports to identify any reasons for failures, can be important in the minimizing of such accidents.
It might be useful to finish this accident review with some general principles for the avoidance of accidents in and around label and converting units and presses, and in the overall production and non-printing working areas. These can be summarized as follows:
- The provision of adequate information, instruction, training and supervision on all health and safety matters.
- The wearing of appropriate and suitable clothing. No loose clothing which may get caught. Wear good boots or shoes.
- Watching for oil, grease, ink or varnish around the machine and clean it up
- Keeping workbenches and floor areas tidy and free from waste.
- Checking that tools and equipment are not lying on the machine when starting up.
- Knowing all the control points around the machine and how to stop in an emergency.
- Checking all guards are in position and working properly before starting the machine.
- Stopping the machine before making adjustments and always use the correct tools for the job.
- Never trying to move obstructions or blockages while the machine is still in motion.
- When working on a machine making sure that the power is shut off in a way that it cannot be started accidently.
- Keeping all gangways and passages around machines clear of obstruction.
- Ensuring all waste substrate is placed in the proper containers.
It is worth reiterating that all employers in the global label industry will usually be required by legislation to have plans in place to manage health and safety in the workplace. Where five or more people are employed those plans should be put down in writing in the form of a health and safety policy statement.
There is also a legal requirement to assess potential risks to the employees' working environment before their employment begins (and to review this annually), and to record any significant findings.
Accidents in the printing and label industry have been seeing a steady decline for a good many years. Let's keep it that way. And if possible, reduce the number of accidents even further.
For more Mike Fairley columns, go to www.labelsandlabeling.com/contributors/michael-fairley
Stay up to date
Subscribe to the free Label News newsletter and receive the latest content every week. We'll never share your email address.