Q&A: Jonathan Sexton
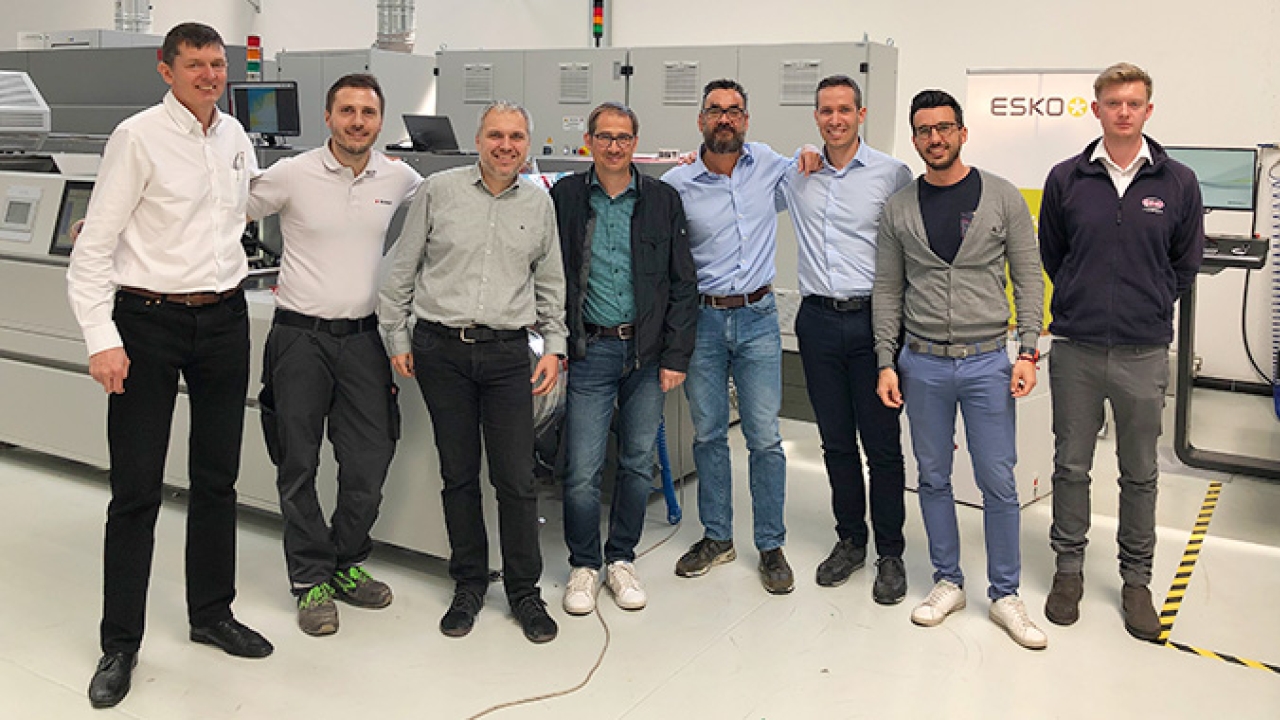
L&L: Can you give us some background about the UVFoodSafe project? Why is such a project necessary?
JS: Historically some industry stakeholders, particularly food industry brand owners, have been fearful of UV technology and even excluded UV inks from use on their packaging and labels. This was born out of occasional high-profile cases in the past where UV inks and coatings were implicated in migration issues. These issues were due to inappropriate product selection and poor practice at the time, but ink technology and printing processes have moved on a long way since then. Thus the industry believed it was the right time to demonstrate that by using correctly specified materials and processes, food compliant packaging and labels can be printed with full confidence.
L&L: What has been the involvement of the wider industry and industry associations in the project?
JS: The project was originally motivated by a small number of individual companies, but it soon became clear that there was broad support for the initiative and the activity group grew quickly. In order to manage this and the practical activities being discussed, it was agreed to bring the group under the umbrella of Finat, the European label association. Other industry associations such as Radtech and TLMI are also represented on the group and today the group has members covering the all the main disciplines in the label industry.
L&L: What were the challenges you faced in setting the testing criteria? Were these challenges different for digital and conventional presses?
JS: The basic criteria is straightforward in Europe, where the Food Packaging regulatory framework and in particular the EC 1935/2004 Regulation states in simple terms that the packaging (printed or not) should not have any adverse effect on the food and consumer.
Of course, further to this there are complex definitions of how to achieve this, and at the heart of it is the requirement to conduct migration testing and meet specific levels for individual ink and packaging materials.
The challenge is that this type of testing is time-consuming and expensive and cannot normally be done by the label converter. The group activities were designed to demonstrate how in practice these requirements can be met on a daily basis in a production workflow through materials selection, process control and measurement, with only periodic migration testing, and to define a best practice protocol.
Since we are working to the same end target, the challenges are basically the same in digital and conventional UV printing and equally true for UV LED. Nevertheless, we need to be conscious that in digital inkjet we work with higher film weights and lower viscosities than in UV flexo and offset, which can impact the way the ink cures, and in LED we work with a very narrow UV spectrum and specific ink products. The digital and LED communities are represented in the UVFoodSafe group, and based on the results for the UV flexo workflow we will decide if specific activities are needed.
L&L: What do the tests involve in terms of technology and workflow?
JS: The activities of the group were split early on into those focused around the ‘Print’ – the actual label or packaging item produced, and the ‘Process’ – the production methods and controls. The Print activity group has focused on subjects such as packaging design risk assessment, materials selection and print quality testing, including migration testing. The Process group has conducted a series of printing tests to determine the relevant process parameters and how they can be controlled.
L&L: How are the printed packs migration tested? What use do you make of these testing results?
JS: The printed materials are carefully selected to ensure they are representative and subjected to testing whereby a food simulant is put in contact with the printed material – normally the side which is contact with the food – for a period of time, normally 10 days, and at controlled temperature such as 40 deg C to simulate extended exposure at room temperature. The exposed simulant has then to be analyzed in a sophisticated laboratory. This is a complex and demanding process as we are trying to detect material down to levels of ‘parts per billion’. The results for individual chemicals when compared to the levels specified in the regulations will show if the print is compliant and thus safe to put into the market.
L&L: What do you hope to achieve when the testing is complete? Do you aim to provide certificates of compliance, or will the results be presented more in terms of guidelines?
JS: The intention is to provide a series of best practice guidelines that if followed will allow converters to produce, within a clear set of parameters, compliant print on a daily basis. Today the only failsafe way to determine if a printed material is compliant – and thus can be the basis for a compliance certificate – is a migration test. What we are trying to achieve is that the converter and their customer can be confident that the print shipped to the market is compliant even though in practice migration tests may only be periodic.
L&L: What are the main lessons you have learned so far?
JS: The main lesson we have learned is that print process parameters are key in ensuring compliant print production and that there are clear areas where lack of controls could cause non-compliant print to be produced. This is particularly true for the UV dose received by the print, which is determined by the number and power of UV lamps the print is exposed to, the condition of the UV system and the printing speed. Ink color and film weight (or density) are also strongly influencing the final result. These and other parameters need to be understood and controlled to ensure production of compliant print.
L&L: When do you think the testing period will be completed – or will it be ongoing?
JS: The practical and theoretical parts of the project are mostly complete for the UV flexo workflow but are awaiting further migration test results from the final set of print tests – which were performed on real-world print designs – before drafting final conclusions. This work should be complete by the end of the third quarter this year and we should be producing the output reports and guidance documents by year end. We will decide at that time which further activities may be beneficial, which could include specific activities in digital and LED and similar activities in other regions.
L&L: What do you think will be the main benefit to printers and to brand owners?
JS: The main benefit for printers will be a set of guidelines and a framework that can be used to set up a controlled workflow for producing food packaging and labels. This will enable existing producers to optimize their processes, while new entrants – such as label converters – moving into food packaging applications can establish robust controls from the start. For brand owners the information will provide a benchmark for their converter suppliers, demonstrating that they are using the best industry practices and controls to produce printed materials for them. This will build the necessary confidence in print purchasers that UV is a viable process for food packaging and labels.
L&L: Do you think the group’s research will open up new development routes for suppliers of presses, inks, coating systems, curing or measurement/ monitoring systems?
JS: Yes, there are key learnings that will drive innovation in this area. While the work completed will move us forward in understanding and controlling UV printing, it has demonstrated that there are still areas for further improvement, such as end-of-press print testing to predict more accurately the final result of a migration test. Equally there are possibilities for further controls in UV dose measurement and applied ink and coating film weight. Ink development is also a key area where developments could provide products with a wider operating window to achieve the necessary migration levels. The industry will certainly be taking up these challenges.
Stay up to date
Subscribe to the free Label News newsletter and receive the latest content every week. We'll never share your email address.