Breaking new ground in package printing
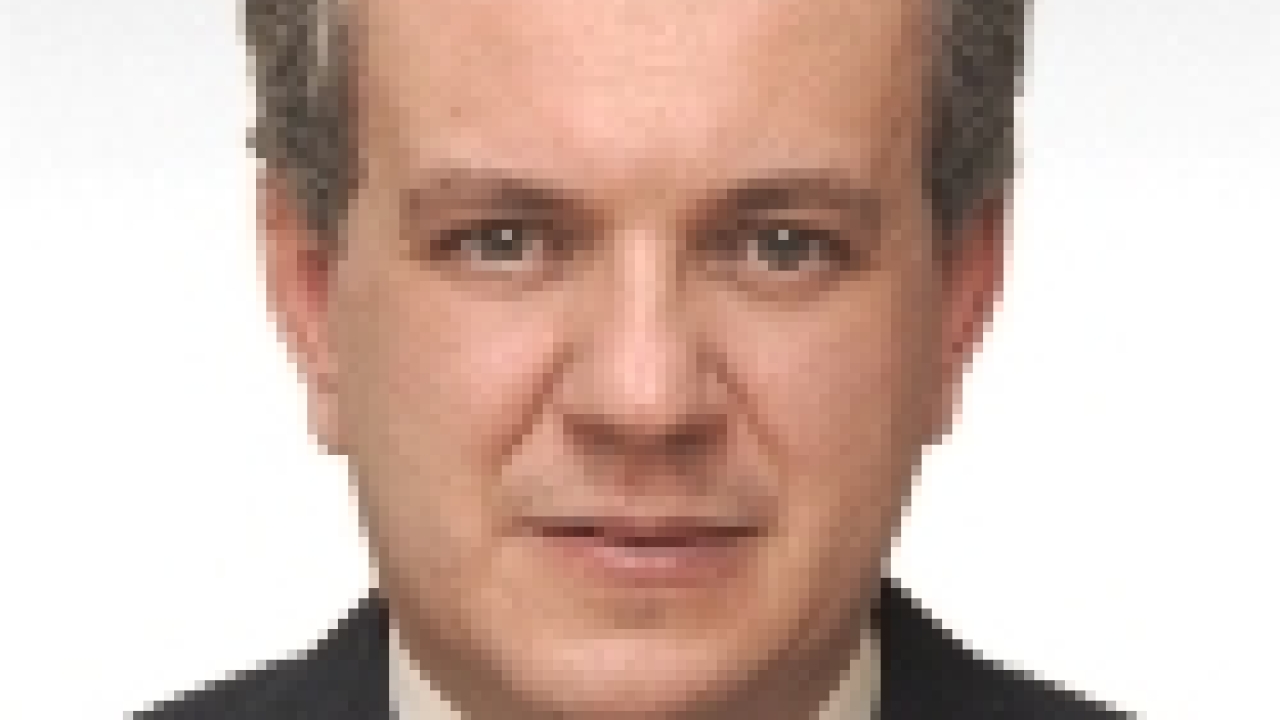
Marco Calcagni, director at Omet, discusses how one press manufacturer has responded to changing market demands using in-line flexo and hybrid machines originally developed for label printing
The idea of using in-line flexo and hybrid machines, developed for label printing, to produce flexible packaging and light carton cases of small and medium formats is not new, but it is very much part of today's news. Some converters were using this technology back in the 1990s, particularly in the USA, where in-line flexo was well established. But, it was not until Labelexpo in 2001, where Omet launched its VaryFlex line, specially configured to print and convert packaging for various sectors from foodstuff to non-food, that the European market started to take notice.
Using consolidated experience of processing extensible films, and in particular shrink and stretch labels, as well as thick cellulose substrates, it was possible to develop the optimum technology for quality printing on different flexible materials, and special units to process and convert carton board into die-cut boxes and cases, in a single step.
Throughout the decade since that launch, the VaryFlex concept has continued to evolve, with the development of new application technologies. These have made it a viable alternative to the large gravure and CI flexo presses, as well as sheet fed offset equipment. All these technologies are chasing the same market; one of superior quality packaging, characterized by reduced run lengths and shorter make ready times. Not forgetting lower costs too.
To cater for this varied market, it was elected to make the press available in a variety of web widths, from 430 mm to 850 mm (17 inch to 33 inch). By doing so, it fulfils the needs of a broad consumer market that demands printed packaging should combine information and a promotional function.
Flexibility and quality
We believe that we are probably unique in the variety of technologies on offer. This begins with a fully modular platform that can be configured as a hybrid, with flexo, gravure, offset, screen, and digital printing, as well as in-line converting units for die-cutting, hot/cold-foiling, and hologram transfer. Of the current crop of multi function machines, the VaryFlex is seen to be the only mid-web in-line press that allows the interchange and variable positioning of the gravure unit, and incorporates in-line lamination and cold-seal devices as options, which are useful for producing ice cream and frozen food packaging.
The machine can be equipped with different drying systems for solvent or UV inks and is provided with the new automatic register control system, known as ‘Vision 2’. This has a video camera mounted on each printing unit to bring the line into register within just a few seconds, and so dramatically reduces start-up times and substrate waste.
For carton box converters, the in-line converting possibilities, with interchangeable die-cutting units and two unique units, called Fly Cut and Twin Cut, enhance the flexibility of the line and increase its productivity. The Fly Cut unit allows the press to cut different sizes from six inches to 33 inches without having to make machine adjustments. Driven by an independent motor, it uses a synchronized shear action for a clean and accurate cut. The Twin Cut system produces a die-cut format range that avoids having to replace heavy and expensive die-cut cylinders.
To enhance appearance and also offer a degree of brand security, one of the key finishing techniques now available is hologram application. It is used with paper and light carton metalization using water-based resins and embossing. An overhead path can be assembled to insert the application in any required position. The flexibility of the in-line multi-technology system is enhanced by stability of gearless drive train, with its associated lack of vibration. It is this that makes the press line so suitable for producing packaging with very high quality graphics in fields that compete directly with CI flexo, sheet fed offset and gravure presses, not only on a quality level, but above all, on an economic one.
Consolidation in strategic markets
Acquiring experience in the packaging market, with more than 10 years active involvement, has brought worldwide success to machines in the VaryFlex series – with different web widths and configurations – working at leading plastic and carton packaging houses across five continents. In our home market for example, we have Cartotecnica Palladio, a major sheet fed offset converter, which specializes in pharmaceutical packaging, while elsewhere Multicolor, Smyth, Identigraphic, and Supremex, figure strongly, and LabelMaker is currently printing flexible packaging on a brand new VaryFlex 850 in Ireland.
Among our most significant reference customers is Hubei (China), where on a multiple configuration line, cigarette cartons with a smart holographic finish are produced on a special unit in one pass. The Chinese market continues to be one of huge potential for our diffuse range of package printing lines, and for that reason we have increased the size of our factory in Shanghai, which contributes to the assembly work, installation and service of the latest generation of machines.
Stay up to date
Subscribe to the free Label News newsletter and receive the latest content every week. We'll never share your email address.