Shenzhen Kunbei walks path to digital transformation
Through investments in digital printing equipment and an ERP system, Shenzhen Kunbei is walking a steady path toward digitization and improved production efficiency.
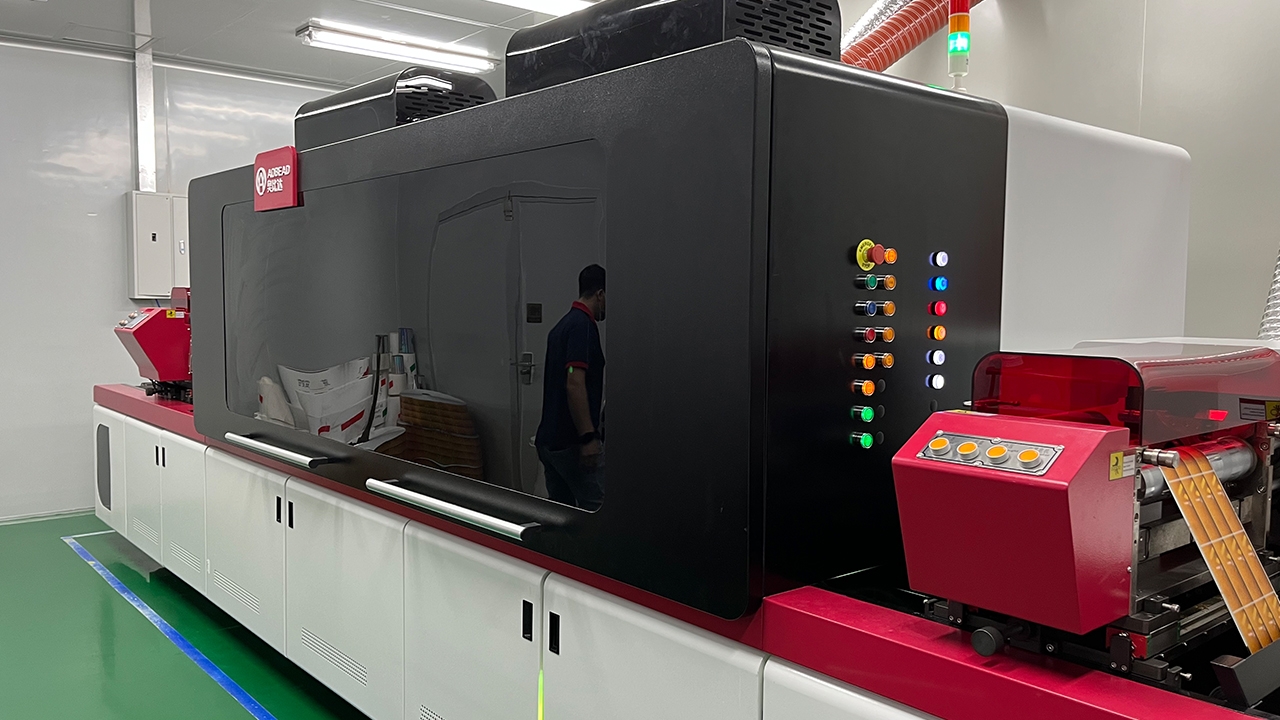
Pulisi DPIM-330F digital-flexo hybrid press in Kunbei
A division of Hong Kong‐based United Label‐Trade, Shenzhen Kunbei first marched into the label industry in 1979, mainly as a producer of price labels and tags for supermarket goods. At the same time, it also acted as an agent for the accompanying hand‐held printers.
With the rapid development of the company, the Hong Kong workshops soon ran out of capacity to meet the growing demand for labels. The company turned its attention to the Chinese mainland when selecting a new production location.
The large population base in mainland China implies a huge demand for labels, and at this time the label printing industry was still in its infancy, with only a small number of label converters. This led United Label‐Trade to register and establish a wholly‐owned subsidiary in Guangdong Province, to be called Shenzhen Kunbei. All its production equipment was moved to Shenzhen, leaving only the sales teams and warehousing services for finished products in Hong Kong.
‘Before barcode technology arrived, all products on supermarket shelves were labeled with price tags,’ says Chen Dongji, vice‐general manager of Shenzhen Kunbei. ‘There was a tremendous demand for price labels and our company grew very fast at that time.’
Chen Dongji joined the company in 1999, originally as a workshop apprentice, and was promoted step by step to his current position. At the peak, there were eight units of Ko‐Pack and Taiyo full rotary letterpress machines in the factory, all running at full capacity.
Following the introduction and rapid adoption of bar code technology, the price label market rapidly shrank. Although Kunbei shifted to the production of barcode labels, its profit margins were squeezed due to the emergence of many low‐cost competitors. ‘Fortunately, we were aware of these seismic market shifts at an early stage, and we started to research a move away from supermarket labels ‐ to in‐mold labels,’ recalls Chen Dongji.
In‐mold labels have totally different technical requirements to self‐adhesive labels since they need to take into account how labels are handled throughout the application process. ‘No blistering or shrinkage or any abnormal phenomena are allowed during the later blow mold or injection process,’ says Chen Dongji. ‘We collaborated with Yupo on research and development at that time and experienced together a constant series of tests, failures, improvements and then re‐tests before the in‐mold labels were finally approved and accepted by cus tomers.’
Thanks to this timely transformation, Kunbei withstood the impact of the introduction of barcode technology. After a short and difficult transition period, in‐mold labels became the major source of business growth at Kunbei, and the company became the largest in‐mold label converter in South China.
Shenzhen Kunbei learned from this experience that a diversified business model was most likely to succeed. Today, the company produces self‐adhesive labels, in‐mold labels and shrink‐sleeve labels, which are widely used in fields such as edible oils, food and beverages, household chemicals, mineral water, electronic products and lubricants.
Automation upgrade
As the label industry enters the ‘new normal’ of post‐pandemic development, a variety of difficulties such as slower growth, cost increases and profit reduction have emerged. Kunbei has been forced to innovate to stand out in a fiercely competitive field.
Jimmy Kwong, the founder of both United Label‐Trade and Shenzhen Kunbei, delegated this arduous and important task to his son, Raymond Kuang, who had worked in banks and then packaging and printing companies after graduating in Canada.
‘I had no experience in the label printing industry before joining Kunbei, and my only knowledge about the printing industry was obtained at a previous sales role in a packaging and printing company,’ Raymond Kwong tells L&L. It took him nearly two years to finally take over the company, starting from his familiar sales role and gradually entering the management team.
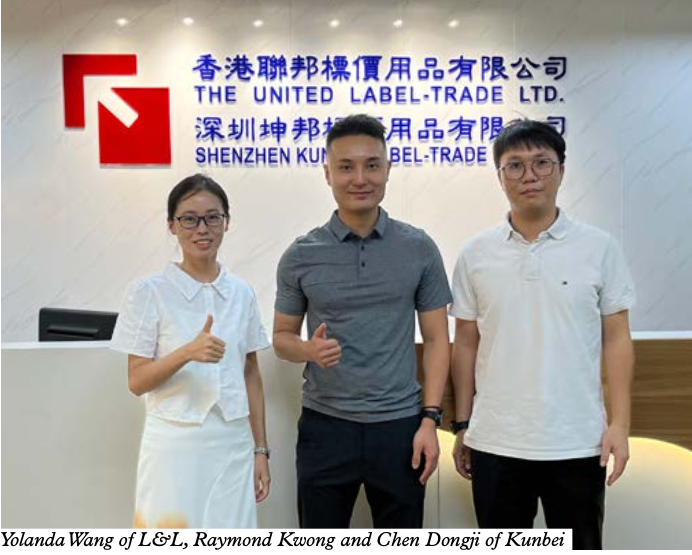
He learned a lot during that period. ‘At first, I thought label products were very simple. However, after gradually understanding and learning, I realized that there were a wide variety of complicated processes and technologies involved in such a small label product, either in raw materials, printing technologies or finishing processes. It was the first time that I had direct experience of the hard road taken by my father and his company.’
Then how to make the change? There is an old saying, ‘A workman must sharpen his tools if he is to do his work well.’ Raymond Kwong resolved to start by upgrading and retrofitting the company’s equipment.
Starting in 2018, Kunbei gradually retired its old Omet inline flexo press and full rotary letterpresses, then successively purchased a Weigang intermittent offset press and inline flexo press, as well as multi‐functional finishing equipment from Rhyguan and Hontec.
Kunbei also retrofitted its presses to connect inline with the finishing units, so orders could be finished in one pass. This significantly helped save time, labor and plant costs.
In May 2023, Kunbei invested in its first digital press, a Pulisi DPIM‐330F digital‐flexo hybrid printing machine. The press is used mainly for small and medium‐sized orders and proofing of new products, freeing production capacity from the company’s conventional printing machines.
‘It’s relatively late for Kunbei to enter the digital printing industry compared with our peers,’ concedes Chen Dongji. ‘However, we had actually looked at digital printing technology some years ago. We are very optimistic about UV inkjet printing with its print quality and speed, which is now very suitable for our current stage of development.
‘Besides this, we attach great importance to the after‐sales service provided by the digital press supplier. One of the major advantages of digital printing is just‐in‐time production, so we require the press supplier to troubleshoot problems that occur during the production process in a timely and effective manner. Pulisi has satisfactorily met our expectations from the performance of the equipment to after‐sales service.’
In addition to hardware upgrades on its equipment, Kunbei has also innovated and optimized its software. Based on years of production experience, Kunbei applied for a series of software patents, including a high‐precision plate‐making system, high‐fidelity image processing, text layout software, a color matching system for digital inks and fully automatic control system for in‐mold label production. This allowed the company to systematically integrate all its in‐house software systems.
At the same time, it has introduced the Xunyue ERP system to monitor in real‐time the operation of all equipment, allowing management to identify and address any problems at the earliest possible opportunity to reduce waste and equipment downtime.
At the time of L&L’s interview with Raymond Kwong, the recently purchased inline flexo and intermittent offset presses were due to arrive. Kwong estimates they will increase the company’s productivity by 20 to 30 percent.
Optimized management
Representing the new generation of managers, Raymond Kwong tells L&L: ‘I am very grateful to my father and the company’s veterans, who have brought together an excellent group of teams in technical, production and customer service. Their professional knowledge, rich technical experience, teamwork awareness and loyalty to the company have not only facilitated my successful takeover but also laid a solid foundation for reforming the company.
‘But I’ve also found some drawbacks left by my predecessors running the company, such as management’s severe dependence on personal experience and poor implementation of some internal rules and regulations, which have significantly affected the potential development of both equipment and the talents of our employees.’
Raymond Kwong has been able to fully leverage his business background in understanding the concept of Big Data to optimize internal management processes.
According to his plans, modern management software will be used to summarize and analyze the data from each process and workstation, identify weak points in production and provide practical and effective solutions when combined with the professional knowledge of the company’s technical team. This process will gradually optimize workflows and achieve the final goal of quality and efficiency improvement as well as reduction of cost and waste.
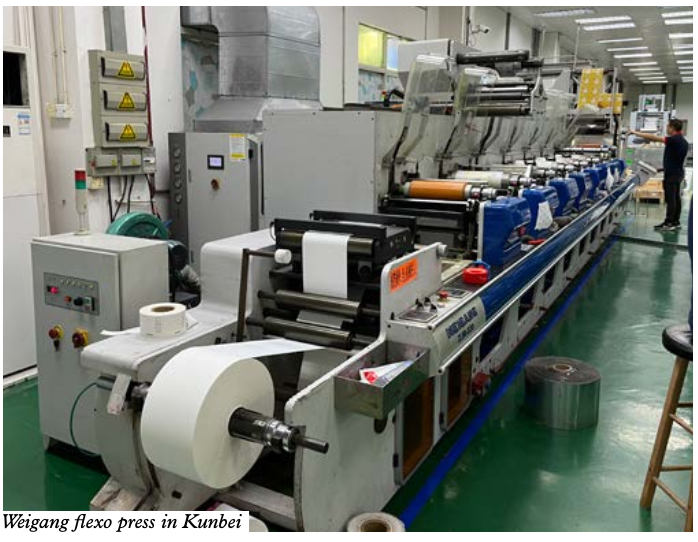
Inevitably some obstacles emerged during this process of management optimization, especially from what Kwong describes as the ‘stubborn habits’ of some older company employees. With a manager’s strategic patience, Kwong patiently promoted his plan, allowing employees to see and experience personally the benefits brought about by a modern management system, ‘so they will gradually accept it, carry it out and finally maintain it themselves.’
Wong says this management system is now becoming firmly established.
‘The number of our employees has been reduced from over 170 to currently 160 without affecting our annual output growth at all,’ says Kwong. ‘Our goal for next year is 140 employees.’
Both Pulisi and Weigang will be demonstrating printing equipment at Labelexpo Asia 2023 in Shanghai this December.
Stay up to date
Subscribe to the free Label News newsletter and receive the latest content every week. We'll never share your email address.