Italian brands secure sustainable goals
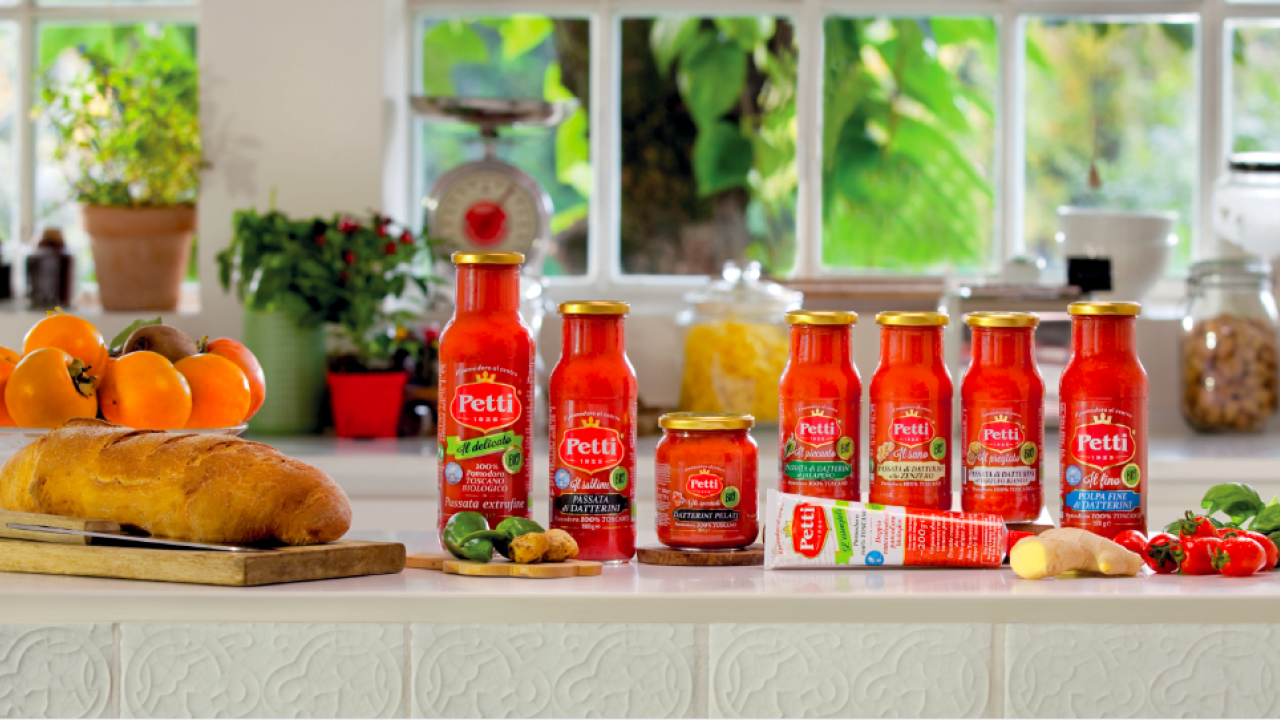
Italsilva, founded in Seregno in 1908 by Ambrogio Silva, is a major player in the Italian detergents sector, while Petti has been active as a food preserves producer since 1925. Peti is focused on the tomatoes which form the basis of Italian cuisine and Pasquale Petti represents the fourth generation to head the group. Its focus is on wholesome ingredients, environmental respect and packaging innovation.
‘These two projects emphasized sustainable development, minimizing waste, lowering costs and, more than anything else, attaining production with the least possible impact on the environment,’ says Nuceria general director Guido Iannone.
Italsilva group worked with C4G (Cycle for Green), which promotes the retrieval and processing of glassine liner waste as an alternative to landfill, incineration and down-cycling. C4G co-operates with an Austrian paper mill which de-siliconizes paper release liners. This has allowed C4G to create a closed loop that turns the waste into cellulose-based recycled material to be fed back into the production cycle. Each year Italsilva generates around 180 tonnes of liner waste and C4G calculates that its recycling leads to a lowering of CO2 emissions by about 360 tonnes a year.
Sustainable growth
Nuceria Group acted as a bridge between the two companies and the driver of the project. ‘The project implemented for the Italsilva group was designed from the beginning to be in compliance with the European Union’s recently announced directive on the circular economy,’ says Guido Iannone. ‘It was inspired by a model of sustainable growth that aims at zeroing waste thanks to the reuse of resources. Waste silicone backing paper has been turned into a resource for Italsilva and for the other companies who receive it as a secondary raw material to be fed back into the production cycle.’
In the case of Petti, Nuceria Group took on the project of restyling the company’s product line with the core concept to ‘make the invisible visible’. The Petti brand name evokes the centrality of the tomato on the packaging, as well as in the Italian food tradition and the Mediterranean diet, and the transparency builds a ‘relationship of faith’ with the consumer.
The packaging process was at the same time optimized by increasing application speed and reducing machine stoppages, while preventing the formation of unsightly air bubbles.
Petti also required a ‘green orientation’ and this came both through the collection and recycling of the company’s PET liner waste, and through increased production efficiency based on using a filmic liner.
‘The advantages of PET liner are often underrated by the labeling industry,’ says Iannone. ‘Compared to silicon paper liner, which is usually disposed of as mixed waste, PET presents many advantages in terms of recyclability and production efficiency.’
Continues Iannone: ‘The most important difference between the two materials concerns the gauge, considerably reduced in PET liner, with various advantages. The amount of liner discarded is less and the cycles between the roll changes are longer because each roll contains at least 20 percent more labels. Hence there is a consequent reduction in transportation costs and the storage space taken up by the rolls of labels.
‘In terms of performance, PET liner is sturdier, and hence guarantees less breakages and greater speed in the label application stage. As well as that, being a plastic material, it ensures a greater cleanliness on the packaging line.’
Nuceria placed the Petti group in contact with Romei, a longstanding specialist in the recovery of industrial waste from polymer producers and converters. Petti’s liner waste was collected and sent for recycling into new industrial-grade polymer. The material is treated at extremely high temperatures (over 2,000 deg C) and the ashes and the heavy metals are incorporated back into the end product. Petti is paid 50 euros/t for the collected liner waste.
Nuceria supported Petti both in pre-production and production stages. In 2016 alone, for an output of around 18.2 million pieces, Nuceria had generated a total cost saving – between direct and indirect costs – of nearly 40,000 euros.
Stay up to date
Subscribe to the free Label News newsletter and receive the latest content every week. We'll never share your email address.