Skanem Bangkok focuses on reducing costs
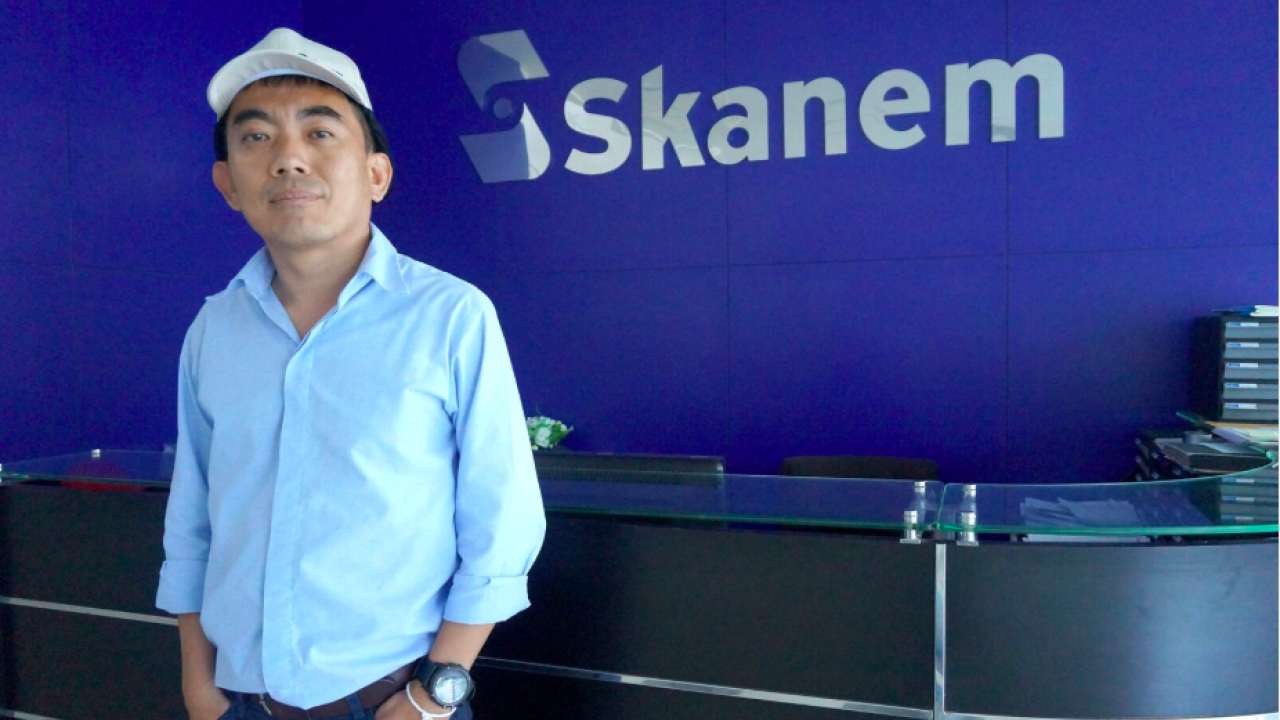
Saton Samerphark, managing director at Skanem Bangkok, says: ‘We started with two 9-color Nilpeter FA-4 presses in July 2007 and today run four. We have always opted for 420mm web width for the flexibility it offers to print bigger sizes of labels.’
The company primarily caters to the FMCG, healthcare and lubricant markets in Thailand. ‘We will have to expand our market reach with another press coming in to ensure production and sales go hand-in-hand. We will have to diversify to in-mold labels and/or shrink sleeves to meet market demand and achieve five to seven percent volume growth year-on-year. We are studying machine capability and market forecasts,’ Samerphark adds.
Currently, the company mainly supplies labels to the Thai market in Southeast Asia. ‘We cater to multinational companies with offices in Thailand. Labels are supplied to local offices and then exported to neighboring countries such as Vietnam and Indonesia. So, we have limited direct export as of now,’ explains Samerphark.
Skanem Bangkok primarily prints long run jobs of 1,500 linear meters and above, because multinational companies normally cater to fast-moving consumer goods that require huge volume. Lubricant labels, however, are often short run jobs printed on labelstock.
The plant prints mainly on labelstock, PE white and filmic materials. It boasts stringent quality checks and in-house inspection with AVT missing label detection systems installed on each slitting machine.
Reducing costs
Despite good infrastructure and service, many companies today are affected by shrinking margins due to a highly competitive market, rising raw material prices and shortage of skilled labor. Thailand is no different in these respects.
‘The market is very competitive. Customers demand competitive pricing for quality labels which is very challenging. Functional and smart labels with QR codes and other security features are demanded but the challenge is that they want more features at less price. Thus, we have implemented cost saving projects in-house to continue to run profitably,’ Samerphark explains.
The team at Skanem Bangkok ensures accurate information of the correct ink, substrates, thickness, and quantity before the job is sent on a press. ‘We thereby print error free labels in one go and waste less, which helps us control our costs,’ he continues.
The company also requests larger substrate rolls so a press printing long-run jobs doesn’t have to be stopped unnecessarily to change rolls.
It is now working on signing up multiple vendors for raw materials so as to receive material and ink in time for a job. ‘This will enable us to negotiate better on price. It is possible to get better returns if we use multiple vendors who offer quality products. Sometimes, brand owners want labels to be printed on materials from a specified company, in which case the printer can charge the extra cost that is being incurred by the business. However, for most other jobs, it is possible to control cost,’ Samerphark elaborates.
Skanem Bangkok is evaluating local suppliers for materials and has started using some samples in trials. ‘We need a vendor to supply quality product in time and at a good price,’ he says.
Sustainability is high on company’s agenda. It not only uses thinner materials but also ensures its corrugated boxes are used multiple times. ‘We are working on brand owners to start using certified materials as well,’ Samerphark says.
‘We have managed to save a considerable percentage by following these steps. Though we can see the immediate effect of some projects, others take several months to show results.’
Stay up to date
Subscribe to the free Label News newsletter and receive the latest content every week. We'll never share your email address.