Carini pioneers Rhino
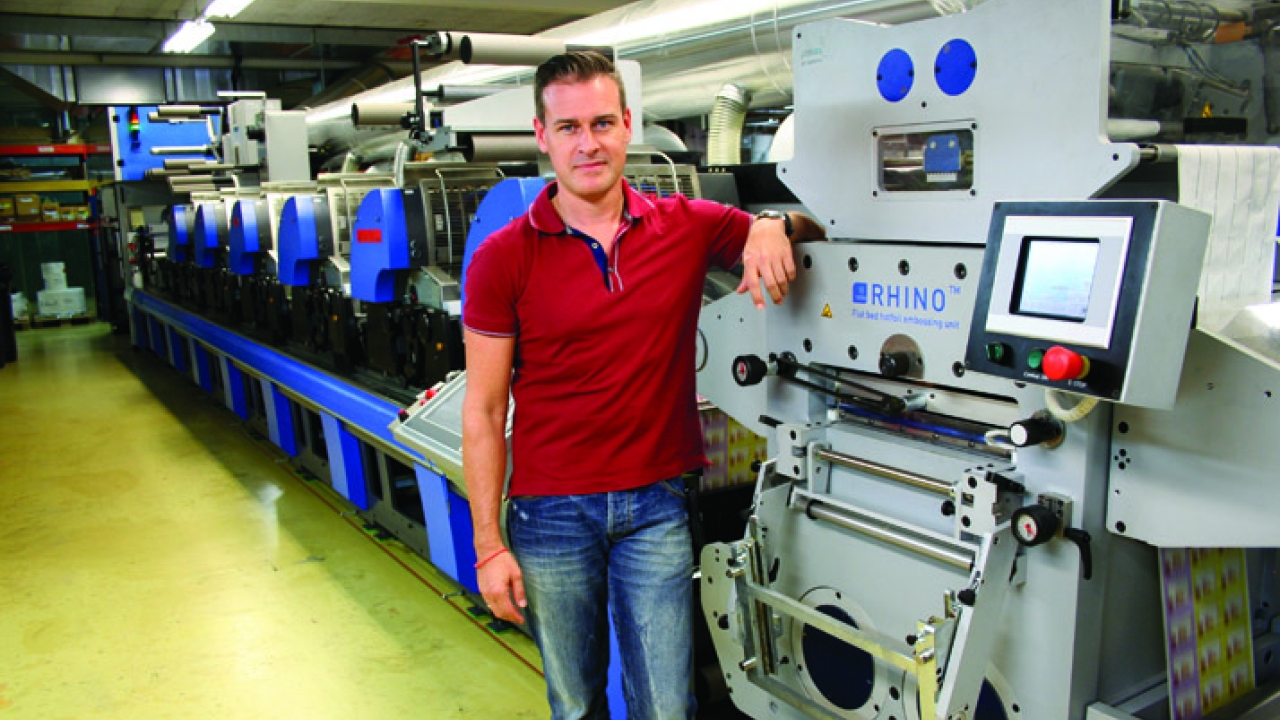
Leading Austrian label converter Etiketten Carini was the first to install Pantec’s in-line flatbed stamping/embossing unit on a Gallus RCS330. Andy Thomas reports
In the premium product sector of the labels market, end users are demanding labels which reflect the added value of their brands. This has driven the development of technology designed to enhance decoration possibilities in-line on narrow web presses.
A good example is the Rhino technology developed by Switzerland-based Pantec, which combines the advantages of flatbed – additional dwell time, pressure and accuracy – with in-line processing.
This article follows the installation of a Pantec Rhino at Austrian converter Carini. As this article was written, it was announced that Carini had won a gold medal at the prestigious Brigl & Bergmeister annual awards for a label converted using the Rhino unit.
Etiketten Carini was founded in Vienna in 1939 by Mario Carini, moving six years later to its current location in Lustenau, a fast-growing town in the Vorarlberg Rhine Valley at the western tip of Austria. In 1963 Siegfried Erne joined the company, which he managed until 1999 when he handed the management to his daughter Andrea, his son-in-law Thomas and his brother Edgar Sohm, who run the company today. Carini’s success can be seen in its blue chip customer list.
The company runs two Gallus RCS330 UV offset combination presses, both with auto unwinders (Kocher & Beck URS and Martin Automatic), Gallus Screeny UV screen stations and UV flexo coaters.
In addition there are UV-letterpress, UV flexo, screen and HP digital presses, all driven by an Esko workflow. The Rhino unit was installed on one of the RCS330 presses in April 2011 – the first time this combination had been attempted. The Rhino unit is located after the seventh print unit and followed by two flexo varnish units.
‘We needed the ability to hot foil and emboss in the same unit,’ says Andreas Larcher, technical manager at Carini. ‘Previously we were carrying out this operation on a Gallus TCS 250, but this was very slow.’
There was a steep learning curve. ‘This was two hard months for me but it was a successful project,’ recalls Larcher. ‘One of the toughest things was getting right the heavier pressure for micro-embossing, but then using less heat and pressure for the best negative text.’
Another key advantage was the ability to build the height of the emboss, which is always made with one stroke. Multiple stroking allows the placement of one foil on top of another. Alternatively foiling can be combined with blind embossing as well as foil embossing using independent strokes. ‘The beauty is that all is on one single plate. The register remains perfect,’ says Larcher. ‘The structure does not deform through the nip because the Rhino is heated, so the paper keeps its 3-D shape.’
At the same time the pressure of the Rhino creates structure in the paper, which saves having to buy textured paper. ‘You can put structure where you want using micro-embossing.’
Larcher adds that the combination of hot foil and micro embossing gives ‘a fantastic 3-D look’, while micro-embossing looks like a hologram. ‘We encourage designers to use these capabilities to design things that other brands can’t do.’
The RCS330 presses are run on a true ‘pit stop’ basis and can print runs as short as 1,000ft. ‘The short makeready time of the Rhino is therefore very important for us,’ says Larcher. ‘You can change the tooling very quickly and there is no additional waste once the press starts. We run the unit at up to 50-60 m/min depending on the number of strokes.’
How does the Rhino’s flatbed foil/embosser compare to a rotary system? ‘On our TCS it was a two-step process on two different modules to hot foil and emboss, so there is always the possibility of a misregister,’ explains Larcher. ‘With the Pantec system it is physically impossible to get a registration error, because it is a one piece tool and it would break. Also because the embossed material is heated first to deform the material, then cools quickly, it "burns in" the shape. On the TCS we have had an embossed line disappear before.’
Having the Rhino in-line also means it can be combined with screen effects, opening up further design possibilities.
Environmental profile
Practical Sustainability is a key metric at Carini. The company is a partner of the Cycle4green liner recycling network sponsored by Finat, and was one of only 25 companies in Austria to win the government’s "klima:aktiv" award recognizing sustainable industrial operations.
During the reconstruction and enlargement of its production facilities, a new heating and cooling exchange system allowed the company to reduce its CO2 output by 12 tonnes.
Another key sustainability issue for Carini is ongoing staff training, and the company enrolls all 130 employees in its Carini training academy.
What is Rhino?
Pantec’s Rhino flatbed hot foil embossing system allows converters to take advantage of the benefits of a flatbed system – increased dwell time and reduced cost tooling – along with a quick tool change cassette, but in an in-line configuration.
The tooling head can be turned to apply foil and emboss in either the machine or cross web directions. This allows saving of materials when the foil is only required for a small part of the image area.
Maximum operating speeds are claimed by Pantec to be up to 120 m/min (360ft), and 60m/min for two strokes. The multi-stepping stamping tool ensures perfect registration using a single die on a stamping length up to 410mm (16in).
Applications include single stroke foil and embossing with multi-height 3D shapes, micro embossing and debossing – with no possibility of register error between foil and embossing. The Multistep facility, with two, three or four strokes, allows the use of multiple foils, embossing, micro embossing and debossing with all strokes aligned on the single die. An example showed by Pantec at Labelexpo Americas demonstrated the use of four foils and included debossing, embossing and micro-embossing on the same label.
Pictured: Andreas Larcher, technical manager at Etiketten Carini, standing by the Pantec Rhino unit on a Gallus RCS330
This article was published in Labels & Labeling issue 1, 2013
Stay up to date
Subscribe to the free Label News newsletter and receive the latest content every week. We'll never share your email address.