HP launch marks package print revolution
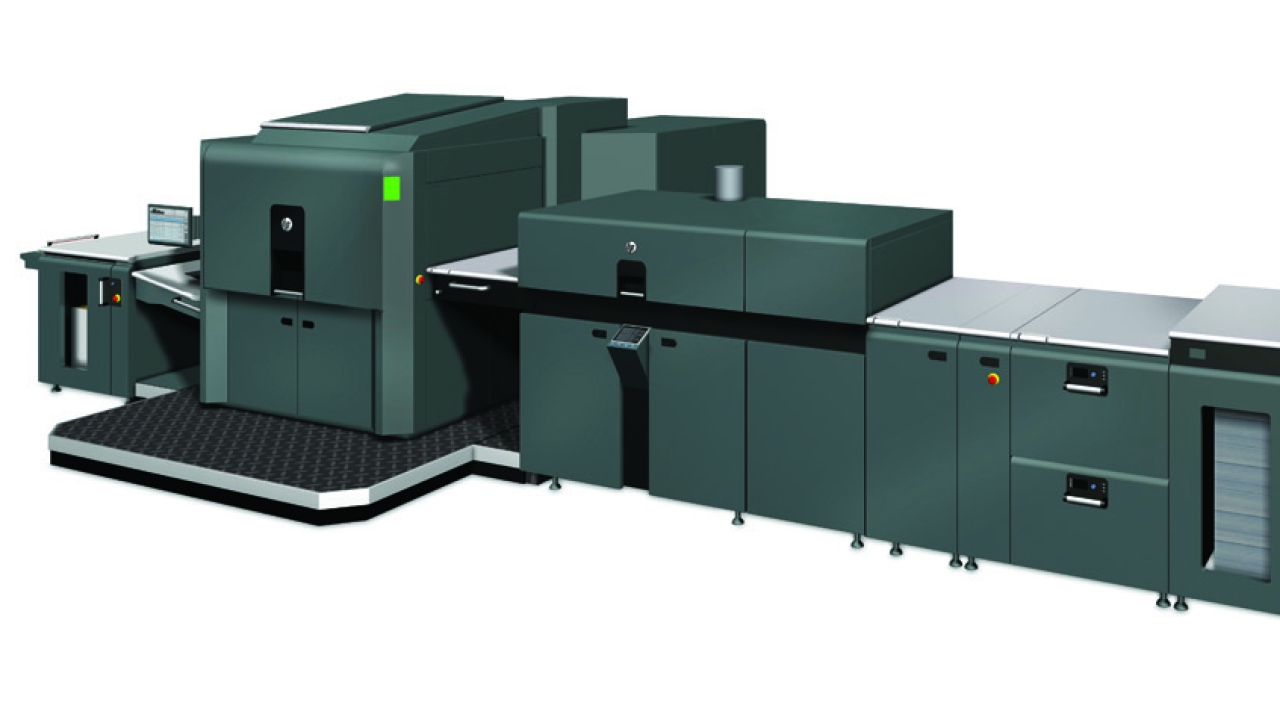
HP Indigo has leveraged the technical and market strength of its digital technology to develop a new generation of dedicated flexible packaging and carton presses. Andy Thomas reports
HP Indigo is developing two digital presses with a robust build and larger format size to meet the requirements of mainstream flexible packaging and folding carton production.
The 762mm (30in) wide, web-fed HP Indigo 20000 Digital Press and the 750mm (29.5in) wide, sheet-fed HP Indigo 30000 Digital Press use the same ‘one-shot’ 7-color imaging technology – scaled to twice the size – as the WS4600/WS6600 series presses but have new, industrial strength workflow systems capable of handling standard format packaging substrates.
Some 400 engineers are engaged in this project, which has involved building a new B2+ sheetfed digital press at the same time as developing these two packaging variants, making it one of HP’s biggest global R&D projects.
Christopher Morgan, senior vice president, Graphics Solutions Business at HP, was quite clear that packaging is a long-term strategic market for HP. ‘With these new presses, we can help packaging printers offer their customers the benefits of digital printing and redefine what is possible for the brands they serve.’
Alon Bar-Shany, vice president and general manager at HP’s Indigo digital press division, reinforced that message. He told journalists that packaging and labels already accounts for 20 percent of the company’s global business. ‘By 2016 a large part of our business will be based on these new presses, and the percentage of HP Indigo’s business in packaging will increase.’
New capabilities
The carton and flexible packaging presses will take advantage of a range of new capabilities unveiled for the HP Indigo WS6600 press launched at Labelexpo Europe. These will include in-line priming (ILP) – as well as in-line corona treating – integrated in the press infeed units. Michelman recently released a new water-based primer for the ILP unit – Michem ILP040 primer – which extends the ILP’s media compatibility from paper-based substrates to synthetic media. This will enable the presses to handle all standard package printing materials without pre-coating.
Another significant innovation is Enhanced Productivity Mode. This boosts press throughput by one-third by printing in CMY and dropping the black separation.
With toner-based systems this can often leave a somewhat ‘dirty’ or ‘brown’ black, but the print examples seen by this writer at the HP Indigo development facility were truly impressive and hard to tell apart from the CMYK version. Press speed is increased – since each separation requires another rotation of the imaging drum – and total print cost is reduced.
For the pharma market a significant new release is HP’s security print package, SecurePack, initially made available for HP Indigo WS6600 and HP Indigo WS4600 model presses, which provides ‘a controlled and monitored environment for efficient production of pharmaceutical and security applications’. This will be available to both the package print presses.
The 20000 up close
Scheduled for commercial availability in late 2013, the HP Indigo 20000 is a roll-to-roll digital press designed primarily for flexible packaging.
The press’s 762mm (30in) media width and 1,100mm (44in) repeat length should accommodate most format sizes in these market sectors. The HP Indigo 20000 runs at 27 linear meters (88.6 linear feet) in five-color mode – full process color plus white – and at 45 linear metres (147.6 linear feet) per minute when running in Enhanced Productivity Mode. Material range is from 10 to 250 microns (0.4 –10pt). The integrated rotogravure-based priming unit will allow the press to print on paper, flexible packaging film and aluminum substrates as well as prime labels, shrink sleeves and laminate tubes, all without pre-coating. Materials printed on the press are compatible with dry lamination and form-fill-seal machinery and comply with indirect contact food packaging regulations when used with good manufacturing practices.
Flexible packaging applications require both surface printing on opaque materials and reverse printing on clear materials, and the press’ color switching technology allows changing of color and color sequence on the fly. HP’s ink scientists have demonstrated a new, more opaque white, which matches up well to current UV flexo whites as a first down without a double bump.
The HP Indigo 20000 press will incorporate an EskoArtwork-driven print server and upstream prepress tools and third-party options are being developed to provide complementary capabilities such as web-to-print, MIS services and inspection/verification of printed content.
For converters wishing to set up dedicated production lines for short-run work, there will be qualified finishing options for the new press. Pouch-making equipment manufacturer Totani has joined the HP SmartStream Solutions Partner program, for example, and is developing a range of flexible packaging finishing solutions.
Carton special
The sheet-fed HP Indigo 30000 Digital Press offers a 750 x 530mm (29.5 x 20.9in) format size compatible with existing B2+ offset printing presses used for mainstream folding carton production. Scheduled for commercial availability in late 2013, the press offers up to 7-color printing on carton stocks up to 600 microns thick. The press can run up to 4,600 sheets per hour in Enhanced Productivity Mode and 3,450 sheets per hour with regular 4-color process printing. After printing the sheet is immediately available for post-print finishing since there are no drying or set-off issues.
As mentioned, the press will incorporate an in-line priming unit at the infeed and will be equipped with a heavy duty offset press style pile feeder and vacumm transport.
The HP Indigo 30000 features the same EskoArtwork-driven print server and upstream prepress tools as the 20000. Additional production components, such as digital finishing solutions from HP SmartStream Solutions Partner program members, are also promised – including post-print in-line varnishing.
Scaling up
At the pre-drupa event, HP Indigo focused attention on the launch of the 10000 sheetfed press, which showcases many of the imaging innovations used in the packaging press print engines.
A glance inside the B2+ format HP Indigo 10000 digital press shows how HP has handled the bigger photo-imaging plate (PIP) and blanket required for the larger print format. The operator’s life is made much easier with the PIP automated replacement system (PARS) and automated blanket replacement (BARS). The latter works much like a semi-automatic plate changer on an offset press: the leading edge is fed into a socket on the cylinder, automatically wrapped around the drum, then the trailing edge is locked down. A key advantage of automatic blanket replacement is that the unit does not have to cool down between blanket changes, greatly reducing press downtime.
The writing speed of the imaging head’s 28 lasers has been increased to over 2,000 megapixels a second to cope with the wider format. The ink cabinet has been moved to the rear of the press and the capacity of the ink containers doubled.
Significant automation has been added to the 10000 press including automatic color registration on paper, color calibration with a built in spectrophotometer, and full sheet checking of content against an original using the vision scanner. It will be interesting to see how these elements are integrated into the new packaging presses.
Pictured: The HP Indigo 20000
This article was published in L&L issue 2, 2012
Stay up to date
Subscribe to the free Label News newsletter and receive the latest content every week. We'll never share your email address.