Master Rótulo expands production capabilities with Kongsberg C64
Spanish digital print specialist Master Rótulo has invested in a Kongsberg C64 cutting table from Esko to improve finishing quality, boost overall production capacity and shorten time to market.
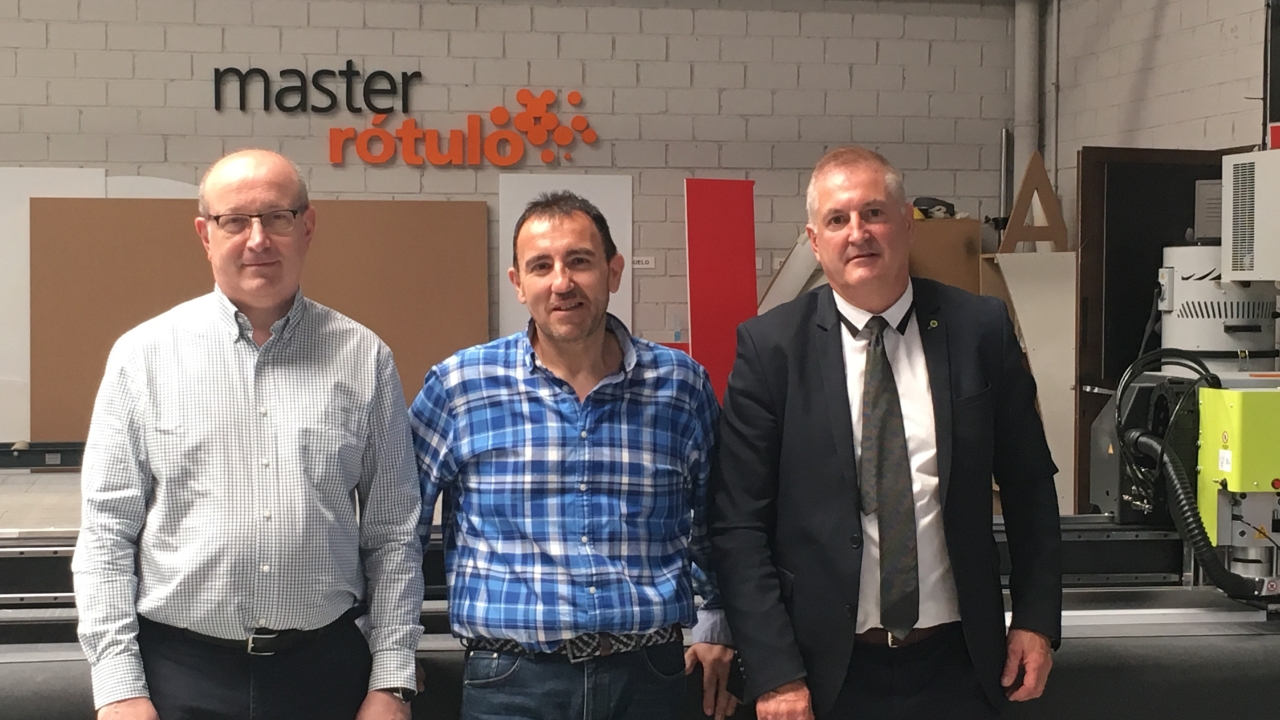
Master Rótulo, established in 1997 and specializing in label manufacturing, has recently expanded its sign and display, and POS presence. Today, the company works with a broad range of clients including advertising agencies, stand builders and architects, managing the entire production process from order to completion. The Madrid-based full-service digital print provider already operates an Esko Kongsberg XL 44. The Kongsberg C64 is a state-of-the-art, 3210 x 3200mm digital cutting table with a carbon-composite traverse beam, which is unique to Esko.
Vicente Adán, Master Rótulo manager, said: ‘We needed a digital cutter to produce random shapes to support different market demands. We have three digital Rho printing machines from Durst and needed a solution that could flexibly and efficiently address our finishing needs.
‘We liked the productivity of the 100m/min system and its ability to cut a wide range of materials from textiles, vinyl, rigid materials and flexible materials, to cardboard and corrugated cardboard. Its cutting width of 3.2 meters means we can adapt cutting capacity to complete production from our three Durst printers. The Kongsberg platform is also easy to use, and the Corruspeed tool allows us to cut cardboard at 100 percent speed. The tool heads’ downward pressure of 500N is unique in the market and truly makes a difference in quality finishing of heavier materials, while the 3kW milling router assures high quality milling results for the heaviest materials like wood, aluminum and plexiglass.
‘The ability to print and cut higher volumes will allow us to expand our production capabilities and guarantee our delivery commitments,’ continued Adán. ‘We have a feeder and a roll feeder with the Kongsberg C64 to help us deliver jobs more quickly. We can also balance the work load and material options between the XP44 and C64 to maximize productivity.
‘Our next planned project is to review how to improve and optimize cutting processes and create a global vision for planning and production. We would like to minimize material waste and errors and look at ways to improve lead times. We are confident we will be able to achieve these goals.’
Stay up to date
Subscribe to the free Label News newsletter and receive the latest content every week. We'll never share your email address.