Outlook Group achieves 20 percent productivity gain with Esko Automation Engine
Outlook Group has invested in boosting its pre-press efficiency with the addition of Esko Automation Engine, a complete pre-press automated workflow software.
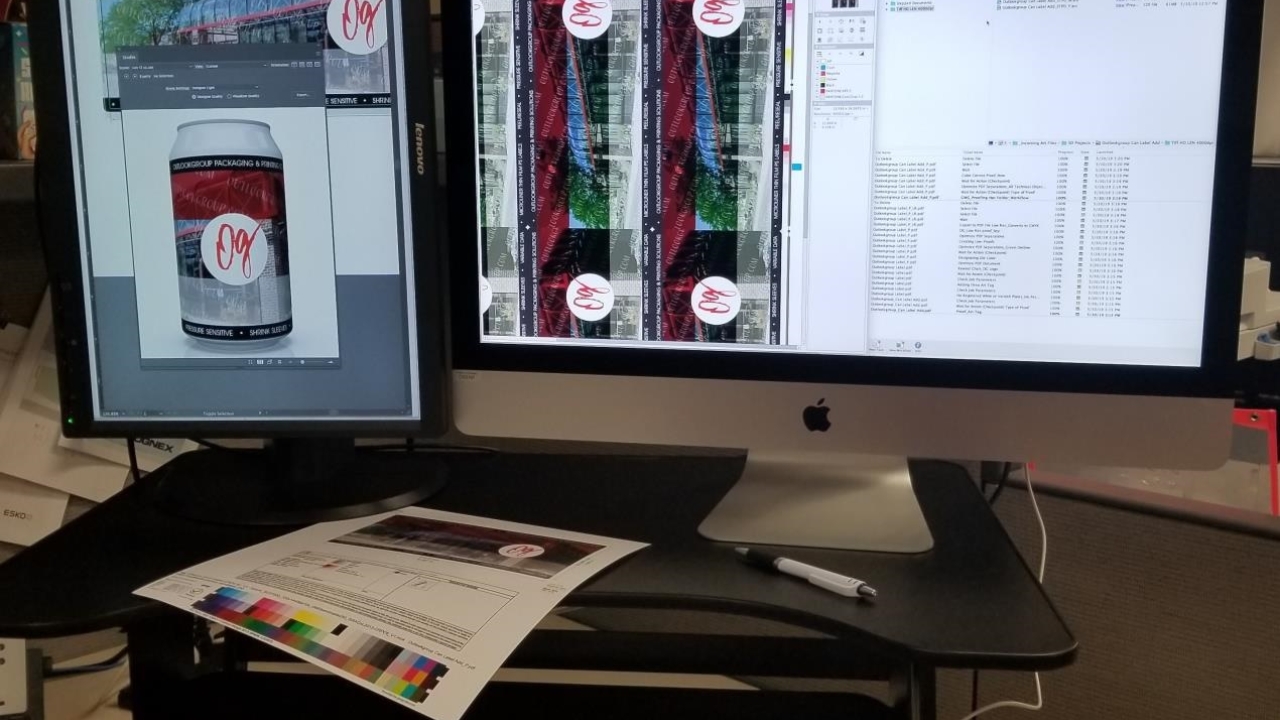
Headquartered in Neenah, Wisconsin, Outlook Group is a packaging manufacturer with more than 40 years’ experience in custom product packaging and printing. Approximately 300 associates produce over $60 million USD in products and services in 400,000+ square feet to clients across the globe.
Outlook Group serves customers in the food and beverage, private label, personal care, consumer healthcare packaging, consumer products, and contract packaging markets with innovative packaging including labels, shrink sleeves, folding cartons, flexible packaging and fulfillment.
Outlook Group had used a manual workflow process which allowed it to RIP once and plot files to any of its imagers and proofers. ‘When our workflow was discontinued by our software vendor, we looked for something else,’ said Wyatt L. Benz, Outlook Group pre-press manager. ‘We invested a lot of money upgrading the pre-press department. Part of that included looking for an automated software solution which would provide us with more benefits than we had before.’
‘Automation Engine has made us faster, more efficient, and our work is very consistent. We import one-up files, and trap and check the color in Automation Engine,’ said Benz. ‘If it all looks good, the workflow builds the step and repeats and press settings. We can automate smart marks, step and repeat, ink coverage and tag lines all in one workflow, without any manual work. From there, the files can go directly to the proofing system on the fly.’
Previously, Outlook Group used Adobe Photoshop to look at its 1-bit TIFF files, one color at a time.
‘Now with the 1-bit TIFF viewer we can QC all of the LEN or TIFF files much more efficiently, looking for stray dots and checking minimum dot areas. Our operators like the measuring tools in the viewer because they now have the ability to measure the minimum dot area and check line screen view traps using the actual files that are used to image plates. This also enables our team to go over the layout one last time before handing off to the plate room.’
It is also easier for Outlook Group to transfer files back and forth between Esko users.
‘One of our customers goes elsewhere for its prepress work and another does a lot of one-up work on its Esko system for a major consumer brand. We can take their normalized PDF files, complete the step and repeat, and jobs are done in minutes,’ said Benz. ‘The other system could do the step & repeats as well, but I suspect passing off files might not be as efficient.’
Studio 3D has already paid for itself by impressing Outlook Group’s new and existing customers with virtual 3D proofs of pouches, bags and cartons.
‘We are much more efficient. As press runs get shorter, we have had to shuffle our staff a bit to other areas; for example, to the plate room and mounting area, where they are needed more,’ said Benz. ‘For a small department with a dozen people - which includes three main operators, a color management person, and one who works back and forth as an interface with the customer support rep - we are pushing jobs through a lot faster. I’d estimate that we have 20 percent more throughput than our old system.
He continued: ‘We have a customer that has hundreds of short run files that must be processed quickly. It used to take about 15 minutes longer to prepare the files. Now, using Automation Engine and the workflows we have built, we have the ability to change from a conventional flexo press over to the digital press in minutes. Reviewing your work and finding commonality when building workflows takes advantage of our Esko Automation, which makes these processes extremely quick. Without the automated step and repeat, this would be very tedious. Now, when launching a workflow to process a job we are able to take that one-up file through automation and create a PDF with our tagline, another PDF to support our AVT at press, step and repeat the file to the press layout adding all press marks and send that layout file off to the proofer. We also can connect this to run through the screener to create 1-bit TIFFs and over to plating, all in one fell swoop.
‘Esko Automation Engine is powerful and very efficient. Everything is there, and it connects not only with other Esko software we’ll use in the future, but with our customers. It has added capacity by approximately 20 percent to our pre-press department. We look forward to expanding our efforts with the Esko software platform.’
Stay up to date
Subscribe to the free Label News newsletter and receive the latest content every week. We'll never share your email address.