Packaging Graphics installs Eco-Eagle
Packaging Graphics has installed an Eco-Eagle cold foil system from Eagle Systems to increase its cold foil efficiencies and effectiveness.
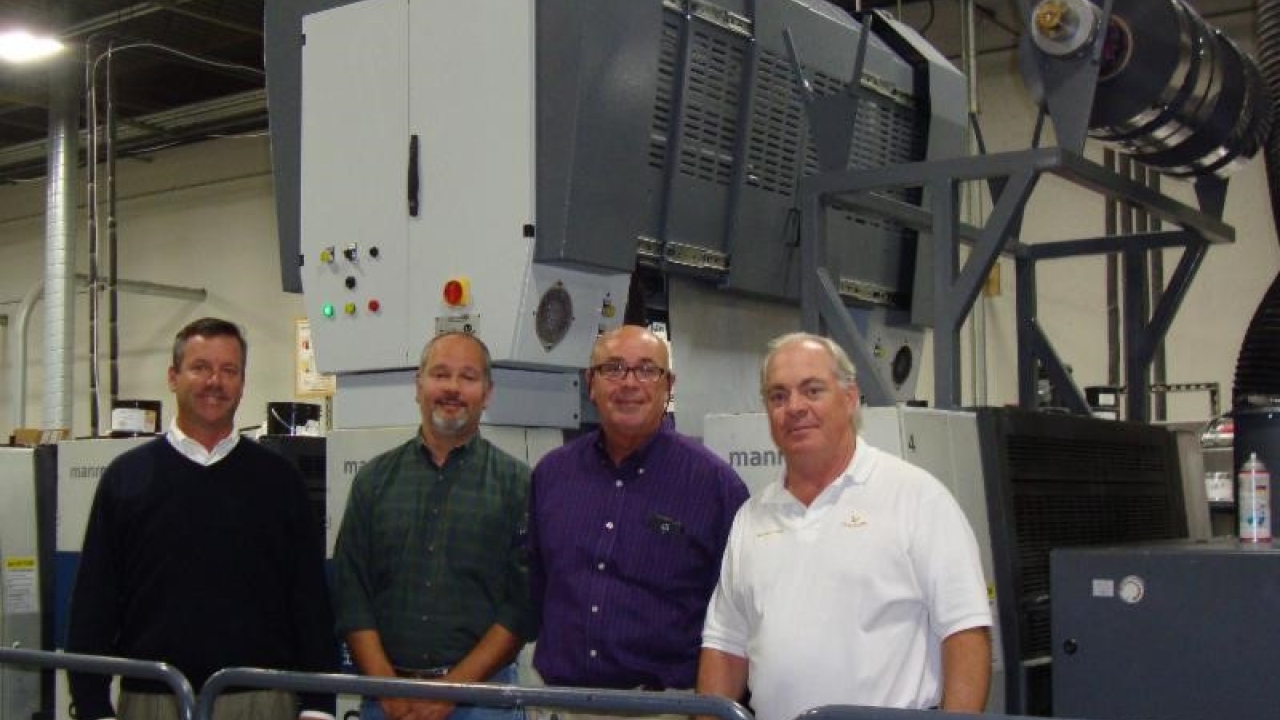
Based in Pawtucket, Rhode Island, Packaging Graphics is a manufacturer of blister cards, folding cartons, thermoformed blisters, trays and clamshells, and produces high-end consumer packaging value-added offerings through in-line capabilities and eye catching inks, coatings and designs.
The Eco-Eagle cold foil system is a value-added finishing technique for cold foil applications. The add-on system can retrofit to new or existing 28-80in sheet-fed offset presses from most major press manufacturers. It offers users the flexibility to apply a single 40in width of foil or multiple widths of foil, in any combination, as narrow as two inches. This ability greatly reduces foil cost and consumption.
In addition, the cold foil system operates on about the same amount of electricity as a 1,500-watt hair dryer, reducing energy demands in production environments. This year, Eagle Systems has added the ability to use a 16,000k foil roll which allows for less change over during a job run.
The Eco-Eagle cold foil system was installed early last week, and now operates in unison with the company’s manroland press.
‘Our clients choose Packaging Graphics for many reasons, but the one-stop packaging solution seems to be high on the list,’ said Greg Iannuccillo, vice-president of sales at Packaging Graphics. ‘We have a 300,000 sq. ft self-contained facility which houses engineering, pre-press, the manufacturing of print, die-cutting, windowing, gluing and EAS tag application, as well as all thermoforming operations.
‘The facility also stores our make-and-hold finished goods and raw material inventory. The Eagle system allows even our sophisticated operation to run lower quantities without sacrificing efficiencies. With the ever changing world of speed-to-market, the Eagle system enables us to be more productive and make-ready conscious while controlling costs.’
‘Previously, we had a different cold foil unit installed on the press [manroland Prindor],’ Iannuccillo said, ‘but with the Eagle system, we expect to expand our services, as well as be more responsive to the immediate needs of our growing client base.
‘One key advantage the system offers us is the use of narrow webs of foil, which in turn delivers significant material savings. And, its ease-of-use greatly reduces our learning curve, while integrating seamlessly with our workflow.’
Iannuccillo concluded: ‘Our research and direct interviews with other Eagle users really convinced us. Even after committing to the system, we were comforted to see videos of our new system as it was being manufactured. With the installation completed in just days, we’re eager to introduce our clients to how much more we can now offer them.’
Pictured (from left): Packaging Graphics’ John Gaffney, Mario Lemos, and Kevin Tranor join Eagle Systems’ president and chief executive officer Mike King to celebrate the install of their new Eco-Eagle cold foil system.
Stay up to date
Subscribe to the free Label News newsletter and receive the latest content every week. We'll never share your email address.