Südpack Bioggio invests in short runs with Bobst MW 80 gravure press
Südpack Bioggio has invested in dedicated short run gravure package printing with the installation of a Bobst MW 80, as it seeks to respond to growing demand for short runs of non-repeat jobs.
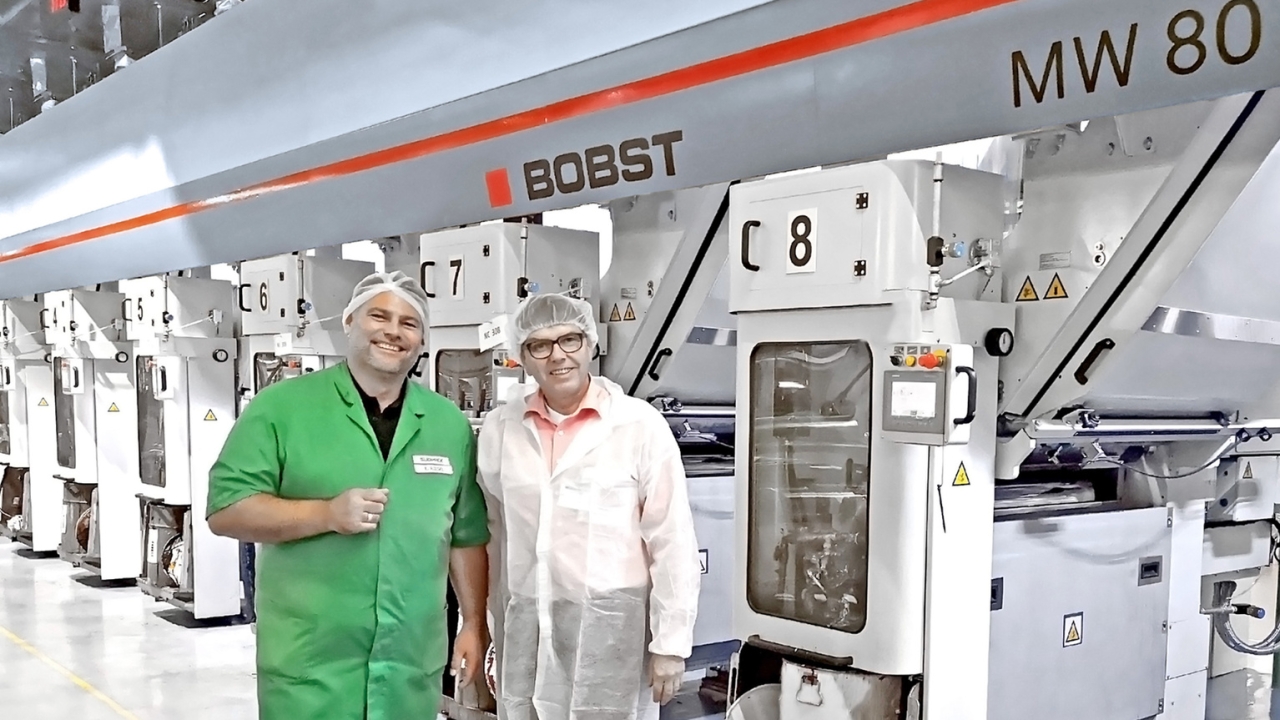
Südpack Bioggio is Südpack Verpackungen’s center for gravure printed packaging. Südpack Verpackungen is a Germany-headquartered film manufacturer for foodstuff, non-food and medical packaging.
The company’s gravure production so far has been served by three wide web Bobst gravure printing presses, whose technical features have enabled printing of a variety of job lengths, including short orders. However, the increased specialization of the company in added value special packaging jobs and the need to increase gravure printing capacity motivated the choice in the MW 80 gravure printing press.
Enrico Riesel, managing director at Südpack Bioggio, said: ‘Our customers are demanding short runs of non-repeat jobs more and more frequently, often with the addition of special visual and tactile finishing effects that enhance the attractiveness of the packaging at points of sale. Finding a way to meet these requests without increasing production costs can be challenging especially on gravure equipment that has thrived in handling mostly medium to long runs.’
The Bobst MW 80 installed by Südpack Bioggio has an 850mm web width with a configuration and features fully dedicated to short run production. It is a non-trolley press fully operated from floor level. The inking system and the impression sleeves are easily and rapidly replaced from the front of the printing units without tools and without and loss of web tension.
In taking stock of performance so far since the press was installed, Südpack Bioggio has identified ink consumption as one of the most striking differences of moving to the MW 80’s new production logic.
Riesel commented: ‘The inking system of the MW 80 combined with the press web width and working speed results in a minimum quantity of ink in circulation compared to a wide web conventional press. Furthermore, purchasing less stock of the non-common inks for the kind of special jobs that we run on the press, has improved our competitiveness.’
Riesel concluded: ‘If packaging converters want to play a role in the market, they need to be as flexible as the market requires them to be in terms of quality, special applications, speed of turn-around. But they are also under a lot of pressure to be competitive and therefore need to find ways to reduce production costs internally. The secret to full efficiency for us has been identifying the right dedicated machine for dedicated job types.’
Stay up to date
Subscribe to the free Label News newsletter and receive the latest content every week. We'll never share your email address.