Double die-cutting delivers dual-shape labels
Italy’s Grafiche Amadeo has used a first-of-its-kind Omet XFlex X2 370 flexo press to create special labels produced using double die-cutting, without backing removal.
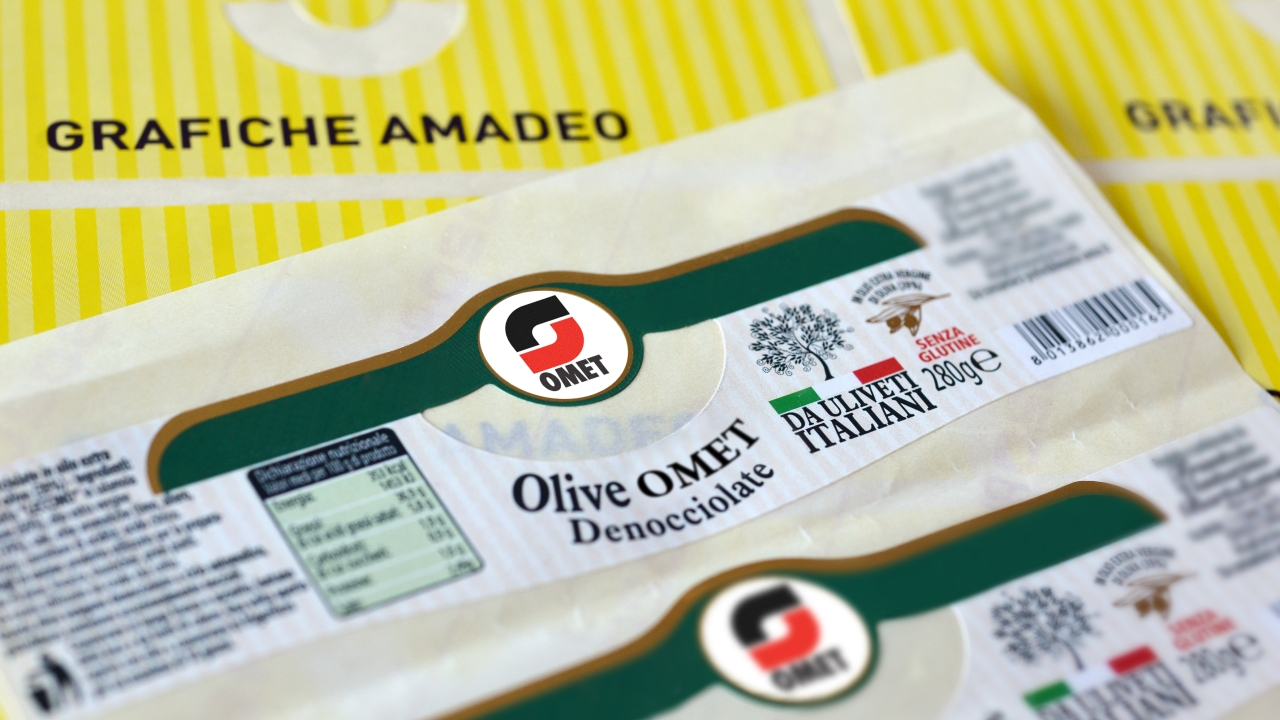
Grafiche Amadeo entered the label business with the purchase of two Omet narrow web flexo presses in three years. The second XFlex X2 was equipped with components developed at the specific request of the customer, including for the production of dual-shape labels based on the addition of a die-cutting station in between the flexo units and accurate use of adhesives.
The machine was especially designed with a particular layout that enables the removal of the internal part of the label, by cutting and removing it before the stripping unit. The die-cutting unit installed in between the last two printing groups cuts the shape meant to be removed, without touching the backing, so preventing the support from being punched, explained Omet.
Andrea Delfino, responsible for the label business at Grafiche Amadeo, added: ‘After the cutting process, we use a cold foil and a flexo unit to apply a layer of UV glue on the shape already die-cut, to facilitate its removal. The label and the filmic substrate are coupled by means of a nip roll, the UV lamp activates the glue and the removable shape sticks to the plastic film that strips it away. The following steps consist in traditional die-cutting process and matrix rewinding to obtain a special label with both internal and external die-cutting shapes.’
Omet had already integrated this special configuration with the die-cutting unit in between two printing groups on an XFlex X6, fully automatic and high-performance machine. Yet, Grafiche Amadeo’s X2 is the first machine to implement this application on a completely mechanical platform.
The 8-color XFlex X2 370 configured for this job runs at up to 130m/min, and Omet explained that the application of a layer of ‘glue killer’ under the shape to be removed is integral to the success of the job. When the adhesive material is separated from the backing, this particular substance is spread onto the area corresponding to the removable shape, weakening the strength of the glue in order to facilitate the stripping process. Without this special glue killer, the maximum printing speed would be dramatically slower.
Stay up to date
Subscribe to the free Label News newsletter and receive the latest content every week. We'll never share your email address.