Iggesund inaugurates new biomass CHP plant at Workington mill
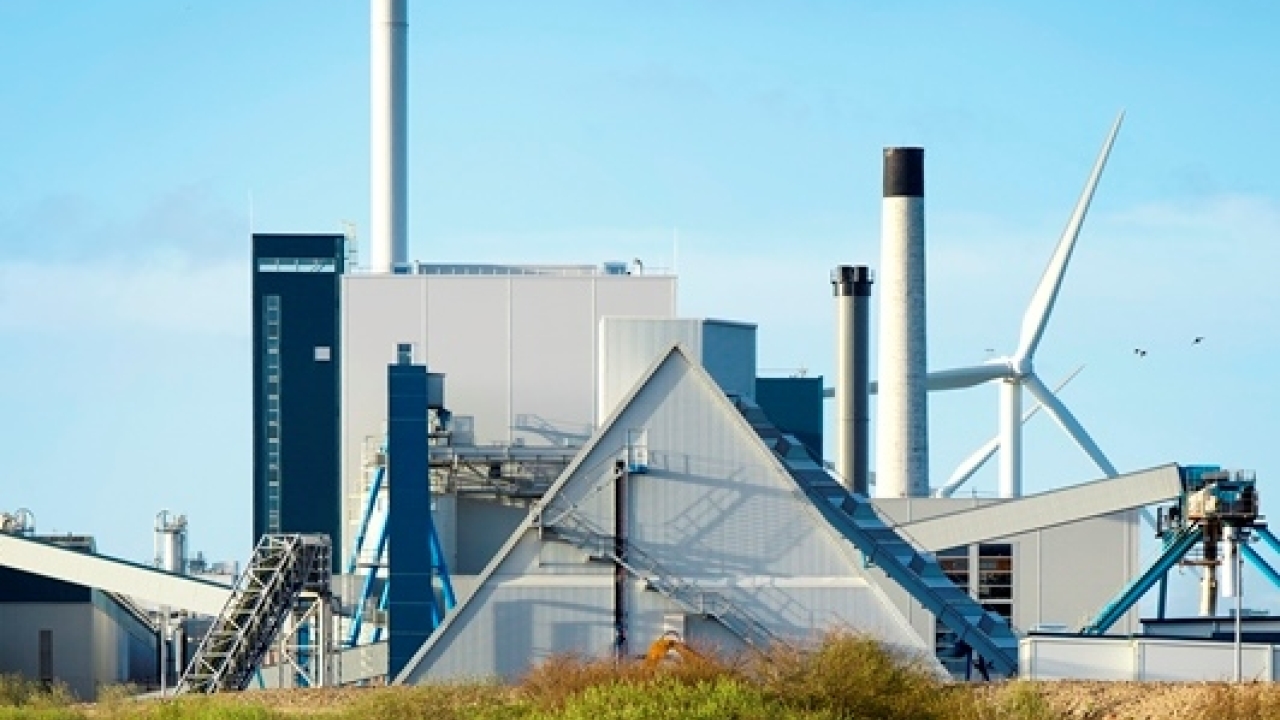
Material supplier Iggesund Paperboard has today (May 28) inaugurated its new biomass CHP plant in Workington, England.
The plant came online in March but was inaugurated at the end of May in the presence of the board of directors of the Holmen Group, the forest industry group to which Iggesund Paperboard belongs.
With the biomass CHP plant, Iggesund Paperboard has switched its energy source from fossil natural gas to biomass. The new biomass boiler involves an annual reduction of fossil carbon emissions equivalent to the emissions from more than 58,000 cars, each driven 20,000km per year.
As well as now being self-sufficient in electricity and heat, the mill will also be able to supply both green electricity and heat to local residents. It is also Cumbria’s tallest building.
The Iggesund Paperboard mill in Workington is the UK’s only producer of folding box board. Incada, the paperboard made at the mill, is constructed of a central layer made of mechanical pulp produced on site, which gives a low weight combined with high stiffness. The outer layers are made of purchased chemical pulp to create high whiteness and good printability.
Incada is used for packaging, book and brochure covers, and other graphical applications.
Ola Schultz-Eklund, the mill’s managing director, said: ‘For more than a decade now Iggesund Paperboard has invested to raise the standard of what was originally a very ordinary paperboard mill to one that is state-of-the-art.
‘Including the £108 million spent on the CHP plant, we have invested more than £200 million in this transformation.
‘In our investment in this new biomass CHP plant, profitability and reduced climate impact go hand in hand. We know that the cost of fossil-based energy will increase faster than that of biomass, so we regard this investment as a way to stabilise our energy costs.
‘At the same time our emissions of fossil carbon dioxide from the production process have now fallen to almost zero, which should reasonably make us an even more interesting option for the large end users, who have more or less promised consumers that they will both declare and reduce the emissions created by the products they sell.’
Schultz-Eklund concluded: ‘We base our production on a renewable raw material that can later be recycled either in material or energy form. Our manufacturing process meets high environmental standards and our paperboard is an excellent fit in a society which is increasingly moving towards greater sustainability.’
Read more about environmental topics here
Stay up to date
Subscribe to the free Label News newsletter and receive the latest content every week. We'll never share your email address.