New recovery boiler starts work at Iggesund Mill
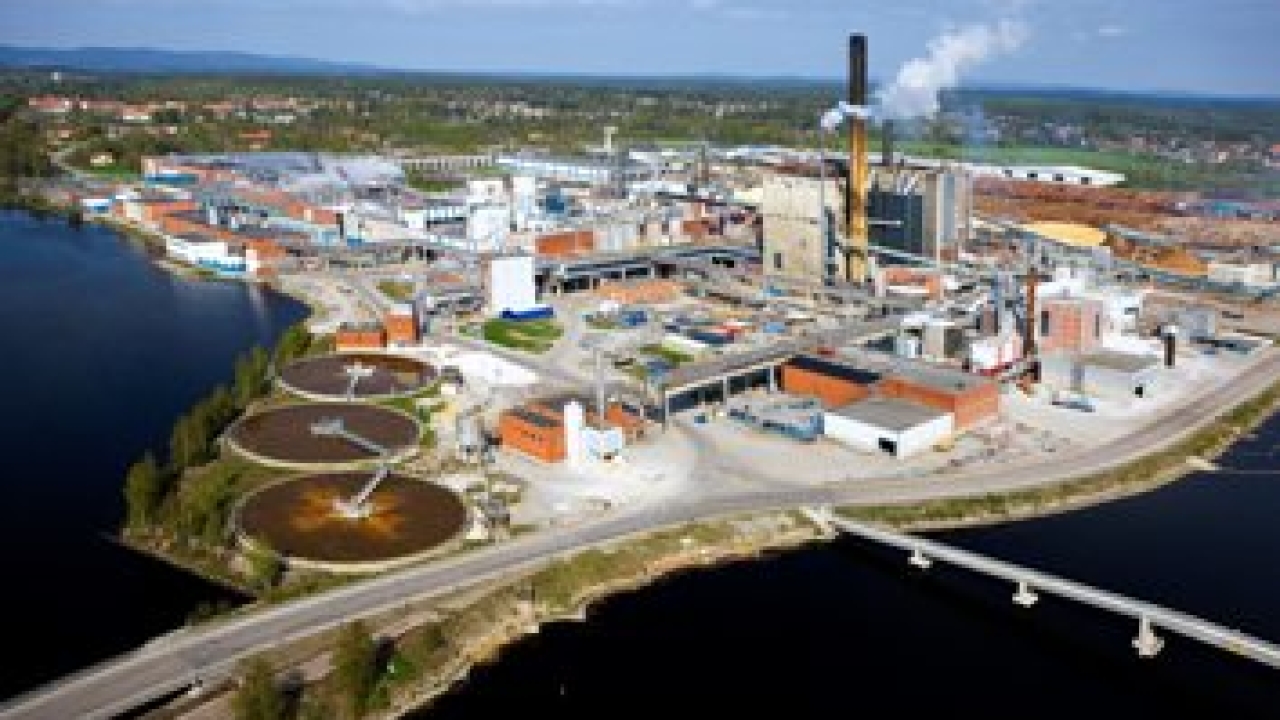
- At heart of sulphate pulp mill producing Invercote paperboard
- Investing further €123m in biomass boiler at Workington
Material supplier Iggesund switched on its new recovery boiler and turbine in Sweden earlier this month, the mill’s largest investment ever at €240 million.
The new recovery boiler is built to withstand higher pressure than any other recovery boiler in Europe, and will work with a steam pressure of 110 bar. This increased pressure makes it possible to generate more electricity.
Self-sufficient facility
The new turbine should be able to supply 520 GWh per year and in the longer term also make Iggesund Mill completely self-sufficient in electricity, although the timescale for this development is variable as it will depend on how pulp production develops.
Currently the mill has a permit to produce 355,000t of pulp annually, but has applied for permission to increase yearly production to 420,000t.
Investing for the future
The recovery boiler is the center of a sulphate pulp mill and serves this function at Iggesund Mill in Sweden, which produces the Invercote paperboard product.
Iggesund instantaneously switched from two old recovery boilers on June 12 to the new one without any interruption in the production process.
Iggesund Mill director Staffan Jonsson said: ‘We’re building for the future step by step.
With increased pulp production we can also grow our paperboard production as we continue to eliminate bottlenecks and fine-tune our board machines.’
Competitive advantage
Iggesund is also investing €123 million in a biomass boiler at its Workington, England facility. Both investments will help reduce fossil carbon emissions from the mills.
Iggesund Mill has received some of the highest levels of investment in the world for a paperboard mill. What lies behind this willingness to invest, explains Jonsson, is the company’s desire to attract and keep the most demanding customers with the most exacting quality requirements:
He said: ‘Our location in Sweden means we can never compete with the cheapest raw materials or lowest paid workforce.
‘Instead, our competitive tool is a product that provides the greatest possible efficiency in our customers’ processes, top-class environmental features and, of course, printing and converting properties which mean that the end products – packaging or printed materials – have a power of attraction that creates superior shelf appeal.’
Read more on substrates here
Read more on environmental matters here
Stay up to date
Subscribe to the free Label News newsletter and receive the latest content every week. We'll never share your email address.