Microscan launches LVS-9585 handheld barcode verifier for printed labels and direct part marks
Microscan, a manufacturer of barcode readers, verifiers and machine vision inspection systems for traceability and quality control in industrial manufacturing, has developed the LVS-9585 handheld portable barcode verifier.
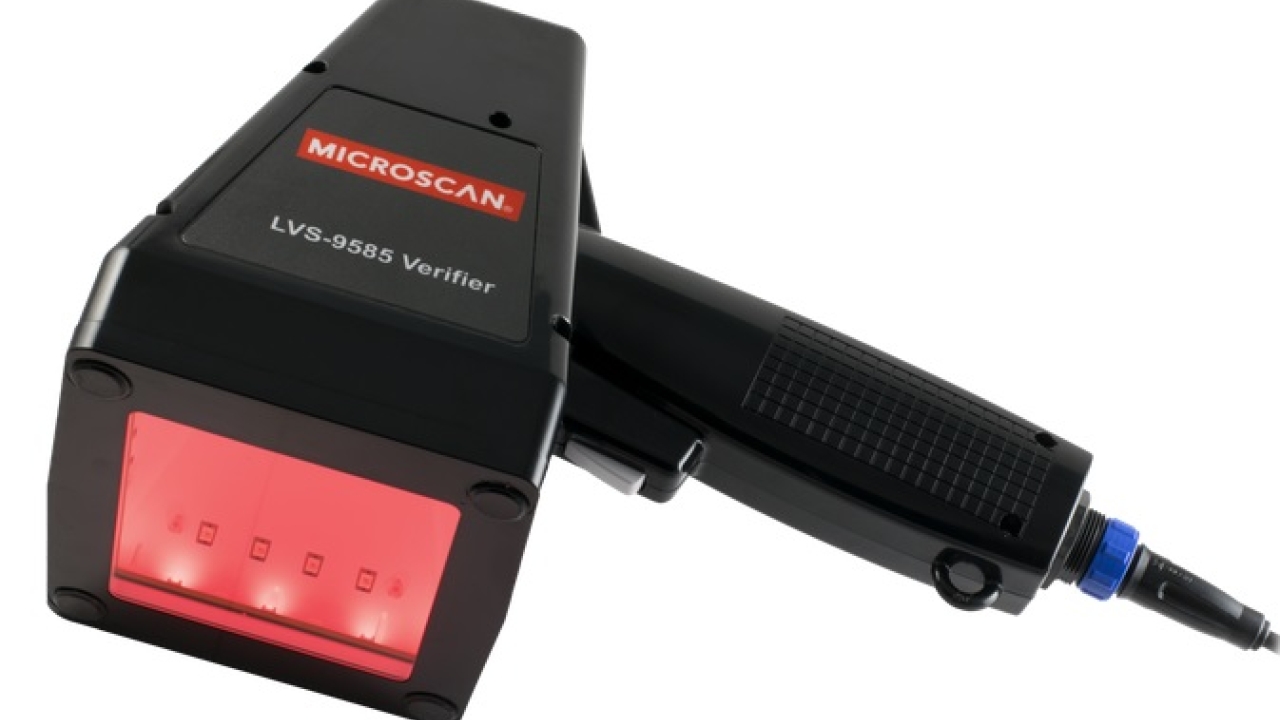
LVS-9585 provides verification of both printed labels and direct part marks. 1D and 2D direct part marks are created using methods such as laser etching, chemical etching, and dot peen marking on a variety of surfaces, including metals, plastics, ceramics and composite materials. They provide a rugged and permanent mark that enables product identification in applications ranging from medical devices to electronic components, as well as automotive, aerospace, and military hardware. To ensure that a part can be accurately and consistently read with a barcode scanner over its operating life, Microscan explained that it is critical that the initially applied mark meets minimum readability requirements.
LVS-9585 verifies the readability, quality and data integrity of 1D and 2D printed labels and direct part marks to internationally accepted standards including GS1, ISO 15415/15416, ISO/IEC 29158 TR, and MIL-STD-130N. Microscan’s GS1 certification provides assurance that the LVS-95XX-series verifiers can help users comply with the US FDA’s Unique Device Identification (UDI) requirements for medical device labels.
PC-based analysis software allows users to see pass/fail data and to identify potential problems before they compromise reliable identification of product barcodes. A large field of view allows verification of larger marks, while a mounting stand accessory allows large parts with direct part marks to be positioned efficiently for fast verification.
For direct part mark applications, the software automatically finds the symbol, cycles through red dome, white dome, and 30-degree angle lighting, selecting the optimal lighting for the material and marking method that are used. The user can then select the optimal lighting for a given part, which Microscan said further optimizes the verification process.
Printed reports and a verification testing data archive featuring both .csv data export and an SQL database interface provide data integration with a user’s quality monitoring system.
Stay up to date
Subscribe to the free Label News newsletter and receive the latest content every week. We'll never share your email address.