SPGPrints launches RotaPlate Dev & Dry
SPGPrints has introduced the RotaPlate Dev & Dry developer-dryer to standardize quality and accelerate throughput in nickel rotary screen pre-press workflows.
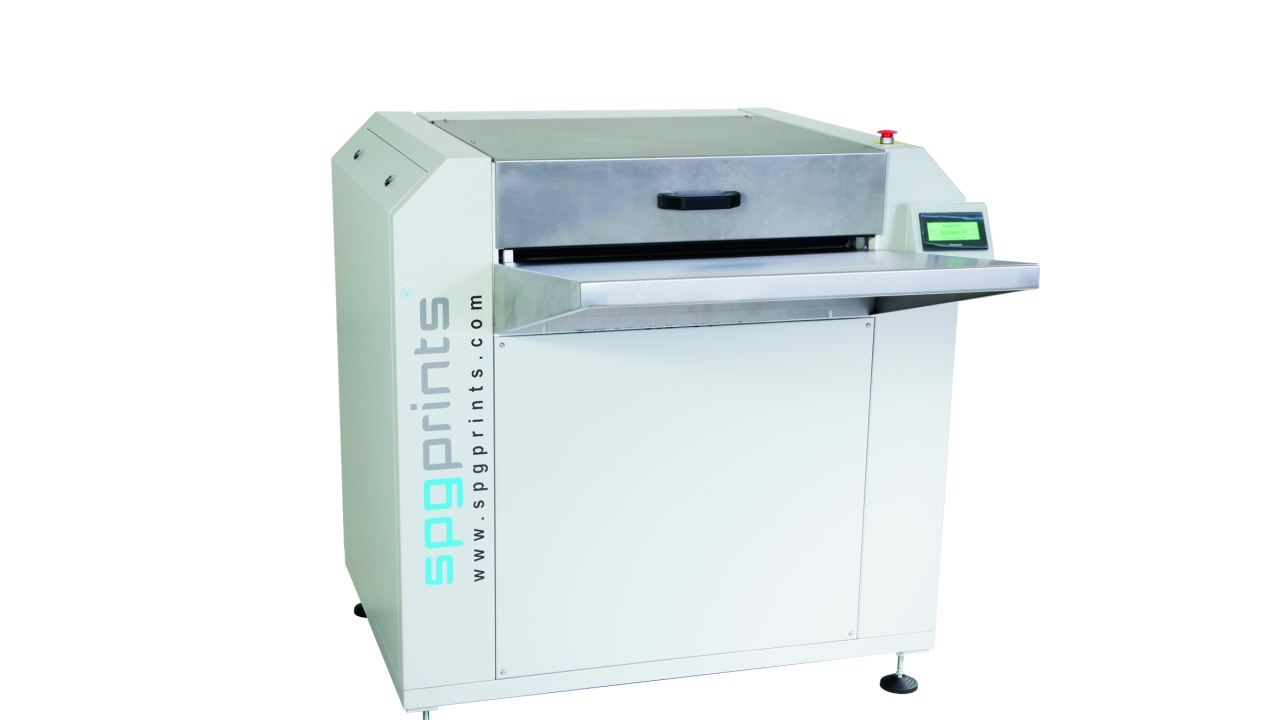
The RotaPlate Dev & Dry system is said to provide a fast, ergonomic and automated means of developing and drying RotaPlate nickel rotary screens, for narrow web applications, in a one-step, quality-assured process.
In a cycle lasting between three and four minutes, the exposed mesh is thoroughly washed out with recyclable water, then automatically air-dried without manual intervention. Once the process is complete, the screen is immediately ready for final assembly.
SPGPrints claims this is four times faster than the manual washing process, with time savings per cycle estimated to be up to 12 minutes. Automated developing and drying ensures uniformity of screen quality, and frees operators to focus on higher value activities, stated SPGPrints. Replacing the use of a water gun that, in some cases, can contribute to wrist strain, is a further claimed benefit. The two sqm unit also includes a water filtering and recycling system, and requires no drainage or exhaust: only electricity and compressed air are needed for use.
Thanks to variable speed modes, RotaPlate Dev & Dry accommodates the complete range of RotaPlate meshes. An intuitive human-machine interface requires only the push of the touchscreen to activate.
Hank Guitjens, commercial manager, label printing at SPGPrints, commented: ‘Screen washout is a repetitive and often monotonous job, and one where quality is difficult to control. RotaPlate Dev & Dry is a complete, sustainable system that integrates with advanced imaging devices, to provide optimum quality rotary screens in a standardized workflow for repeatable, high-quality results. This device is a perfect complement to a modern, clean, lean pressroom, where human intervention is minimized.’
Stay up to date
Subscribe to the free Label News newsletter and receive the latest content every week. We'll never share your email address.