OKI press fits digital gap
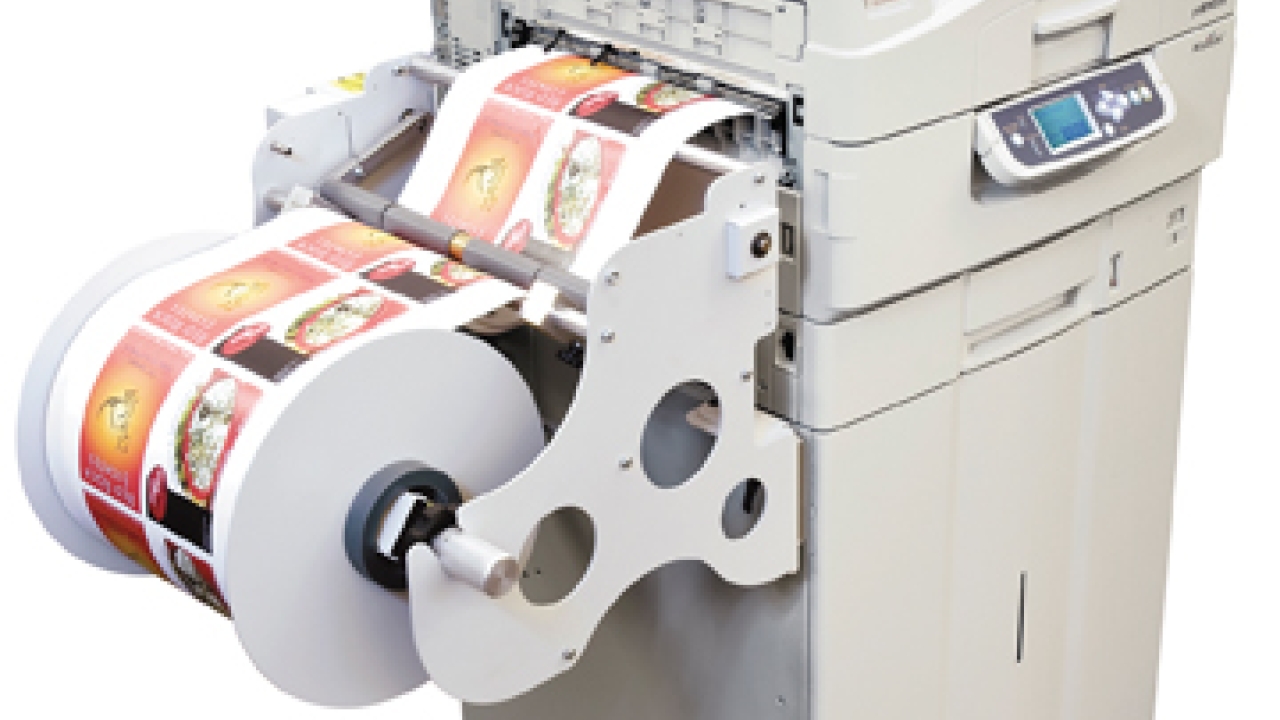
Launched last year, OKI’s proColor pro510DW digital press has found a niche between the entry level and bigger industrial digital label presses. Danielle Jerschefske reports on an early installation
OKI Data Americas has reported the first installations of its proColor pro510DW roll-fed digital label press – part of the proColor Series of digital printers – launched in mid-2011.
Electrophotography is the core foundation of OKI Data digital print technologies, as it is with both HP Indigo and Xeikon. The press uses a drum and toner model with LED imaging for smaller dot production and print clarity. Its consumables are based on OKI dry toner that adheres to a drum roll where the image area charge is neutralized by small LED printheads. The image is then transferred from the drum to the media. The company’s Microfine Spherical Toner chemistry is claimed to deliver a high gloss and smooth tonal gradations.
The OKI pro510DW digital web press has four color stations and a print width up to 12.9 inches. It runs up to 30 ft/min (10 m/min) with fully variable data where required. A three inch core holds up to 300 feet of material.
The press is equipped with auto insertion hardware and software that allows converters to ‘cut-on-the-fly’, so when multiple jobs are run on a single roll, each can be cut and cored while the material is automatically held and set for the next run. This frees up the operator from manual intervention.
Currently machines are delivered with a Compose front end based around a Harlequin RIP, which handles color management, workflow, media type and cost estimates. It can print pre-converted labels or labels can be finished on a wide range of off-line cutting systems.
‘With a small footprint and low investment cost, this OKI system can bring great value to a small converting business,’ says Rich Egert, GM of strategic technology partnerships (STP), part of the new business development group that leads the graphic arts and production division of OKI Data Americas. ‘The pro510DW is ideal for promotional runs within a full service flexo house giving the capability to complete short run, profitable, high quality solutions for less than 15,000 labels.’
Profitable ROI
Tim Newton is the manufacturing director for Thomco Specialty Products & Converting in Suwanee, Georgia, a company that distributes a wide variety of materials for industrial markets like automotive, aerospace, offset printing, signs and graphics and metal shops. The company also creates complex custom converting solutions for applications including testing, design, prototypes, and manufactured parts.
Thomco currently uses Roland UV and solvent inkjet technology to print small quantities of decals on vinyl substrates, mostly for prototype and testing work, using tool-less dies to cut the materials. This business has expanded exponentially for Thomco over the last five years, and led the company to expand its digital offering with an OKI Data pro510DW digital web press to support its flexographic label production.
Most of the work coming off the OKI press is sheeted, with cutting done off-line using a tool-less die flatbed plotter. The converter estimates that it must be printing 700-1,000 feet of labels to justify the cost of finishing labels in rolls.
Explaining the thinking behind his digital investment, Newton says, ‘We had to be able to justify the spend on the equipment. The OKI system and its technology are appropriate for our current needs and the investment cost fair for the expected ROI.’
Thomco ran an assessment between a Xeikon system and the OKI platform using the same image before a decision was made. ‘When we reviewed the two runs, we felt the quality was eighty percent of a Xeikon, while the cost of the OKI system is only 10 percent of the price of a Xeikon. And while the OKI press isn’t high speed – it’s a similar speed to entry level competitive systems and about half the speed of higher end models in the marketplace – we don’t really care about that right now.’
The pro510DW is producing runs at Thomco up to 5,000 feet, in three- and four-color process work with multiple SKUs that are simply too costly to take-on with flexo. The converter has been able to call on small accounts where it previously could not compete – for example producing 250 labels for a chemical spray, with three flavors that required three-color work. Thomco has validated and standardized substrates into five general groups: board eight to 13pt, matte paper, gloss poly, matte poly and matte vinyl.
Newton concludes that the OKI system does a very good job, and is likely to pay for itself within six to 12 months of operation, given current workload and usage.
Pictured: OKI pro510DW digital web press for labels
This article was published in L&L issue 3, 2012
Stay up to date
Subscribe to the free Label News newsletter and receive the latest content every week. We'll never share your email address.